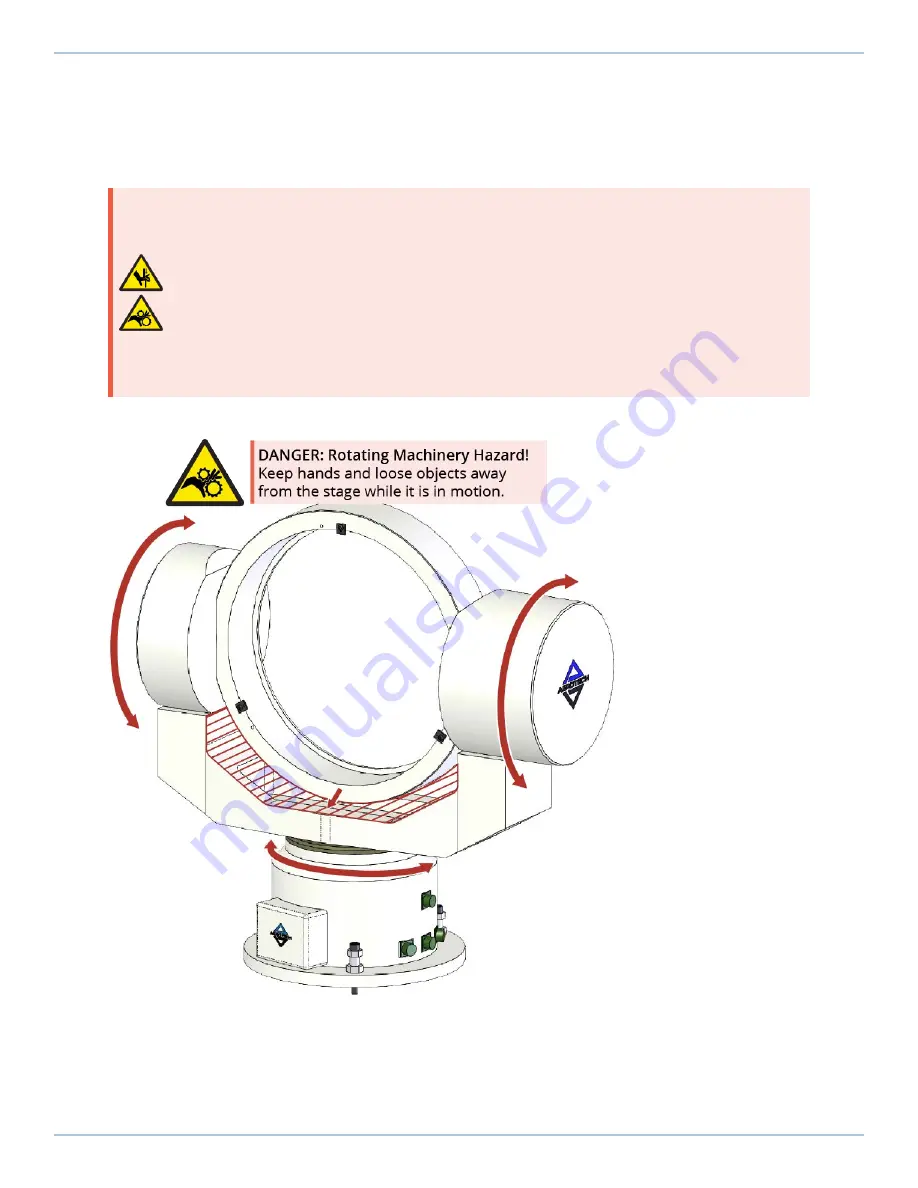
Pinch Points
A pinch point is a mechanical hazard that can occur when there are exposed parts of the stage or
system that can move. For example, the travel of a stage tabletop could expose the user to a pinch
point between the tabletop and the stage housing. The images that follow will show you typical
external and internal pinch point locations.
DANGER: Mechanical Hazard!
l
System travel can cause crush, shear, or pinch injuries.
l
Only trained operators should operate this equipment.
l
Do not put yourself in the travel path of machinery.
l
Restrict access to all motor and stage parts
o
when the system moves under power (during normal operation, for example).
o
when the system is moved manually (during the installation process or when you
do maintenance, for example).
l
Motors are capable of very high speeds and acceleration rates.
Figure 1:
Typical Pinch Point Locations
AOM360D
Hardware Manual
12
www.aerotech.com
Summary of Contents for AOM360D Series
Page 1: ...Revision 2 00 AOM360D Series Direct Drive Gimbals HARDWARE MANUAL ...
Page 20: ...This page intentionally left blank AOM360D Hardware Manual 20 www aerotech com ...
Page 22: ...Figure 2 2 AOM360D 300 Dimensions AOM360D Hardware Manual 22 www aerotech com ...
Page 23: ...Figure 2 3 AOM360D 400 Dimensions Hardware Manual AOM360D www aerotech com 23 ...
Page 24: ...Figure 2 4 AOM360D 500 Dimensions AOM360D Hardware Manual 24 www aerotech com ...
Page 26: ...Figure 2 5 View of AOM360DShowing Mounting Holes AOM360D Hardware Manual 26 www aerotech com ...
Page 28: ...This page intentionally left blank AOM360D Hardware Manual 28 www aerotech com ...
Page 34: ...Figure 3 2 Feedback Interconnection Drawing AOM360D Hardware Manual 34 www aerotech com ...
Page 40: ...This page intentionally left blank AOM360D Hardware Manual 40 www aerotech com ...
Page 46: ...This page intentionally left blank AOM360D Hardware Manual 46 www aerotech com ...