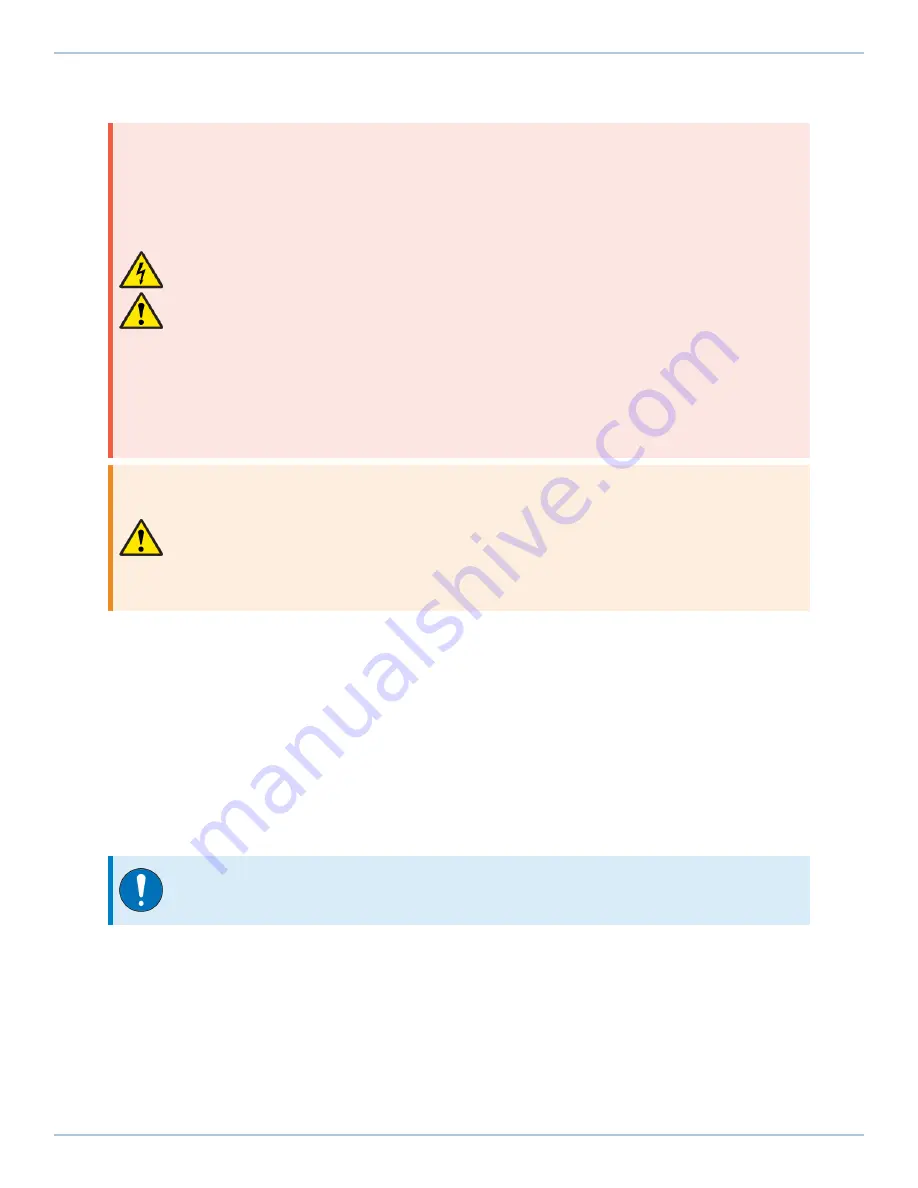
Chapter 3: Electrical Specifications and Installation
DANGER: Electrical Shock Hazard!
l
Restrict operator access to the base and tabletop while the system is connected to a
power source.
l
Stage motor phase voltage levels could be hazardous live.
l
Personnel are protected from hazardous voltages unless electrical interconnections,
protective bonding (safety ground), or motor/stage enclosures are compromised.
l
Do not connect or disconnect stage/motor interconnections while connected to a live
electrical power source.
l
Before you set up or do maintenance, disconnect electrical power.
l
It is the responsibility of the End User/System Integrator to make sure that stages are
properly connected and grounded per Engineering Standards and applicable safety
requirements.
l
It is the responsibility of the End User/System Integrator to configure the system
drive or controller within the Aerotech motor/stage electrical and mechanical
specifications.
WARNING: General Hazard Warning!
Applications that require access to the HEX500-350HL must be restricted to qualified
and trained personnel. The system integrator or qualified installer is responsible for
determining and meeting all safety and compliance requirements when they integrate
the HEX500-350HL into a completed system. Failure to do so could expose the operator
to electrical or mechanical hazards.
Electrical installation requirements will depend on the ordered product options. Installation
instructions in this section are for Aerotech products equipped with standard Aerotech motors
intended for use with an Aerotech motion control system. Contact Aerotech for further information
on products that are otherwise configured.
Aerotech motion control systems are adjusted at the factory for optimum performance. When the
HEX500-350HL is part of a complete Aerotech motion control system, setup should only require that
you connect the hexapod to the appropriate drive chassis with the cables provided. Labels on the
system components should indicate the appropriate connections.
If system level integration was purchased, an electrical drawing that shows the system interconnects
has been supplied with the system (separate from this documentation).
The electrical wiring from the motor and encoder are integrated at the factory. Refer to the sections
that follow for standard motor wiring and connector pinouts.
IMPORTANT
: Refer to the controller documentation to adjust servo gains for optimum
velocity and position stability.
Hardware Manual
HEX500-350HL
www.aerotech.com
29
Summary of Contents for HexGen HEX500-350HL
Page 1: ...Revision 2 01 HexGen HEX500 350HL Hexapod Six DOF Positioning System HARDWARE MANUAL...
Page 16: ...This page intentionally left blank HEX500 350HL Hardware Manual 16 www aerotech com...
Page 22: ...This page intentionally left blank HEX500 350HL Hardware Manual 22 www aerotech com...
Page 40: ...This page intentionally left blank HEX500 350HL Hardware Manual 40 www aerotech com...
Page 44: ...This page intentionally left blank HEX500 350HL Hardware Manual 44 www aerotech com...
Page 48: ...This page intentionally left blank HEX500 350HL Hardware Manual 48 www aerotech com...