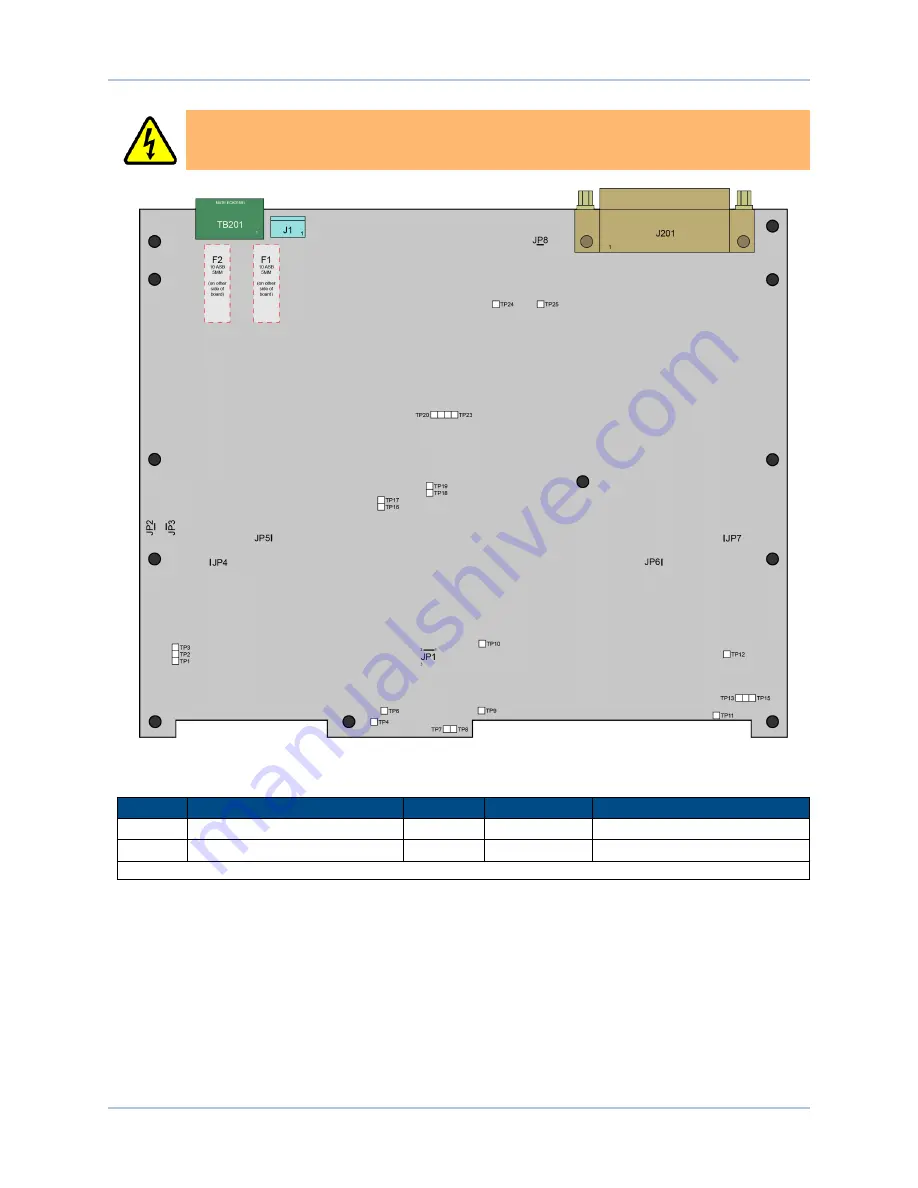
Maintenance
Ndrive FCL Hardware Manual
D A N G E R : Always disconnect the Mains power connection before opening the Ndrive FCL
chassis.
Figure 3-2:
Power Board Assembly
Table 3-4:
Power Board Fuses
Fuse
Description
Size
Aerotech P/N
Manufacturer's P/N
F1
Motor Bus Supply
10 A S.B.
EF01020
Littelfuse 215010.P
F2
Motor Bus Supply
10 A S.B.
EF01020
Littelfuse 215010.P
NOTE: F1 and F2 are located on the bottom of the board.
46
Chapter 3
www.aerotech.com