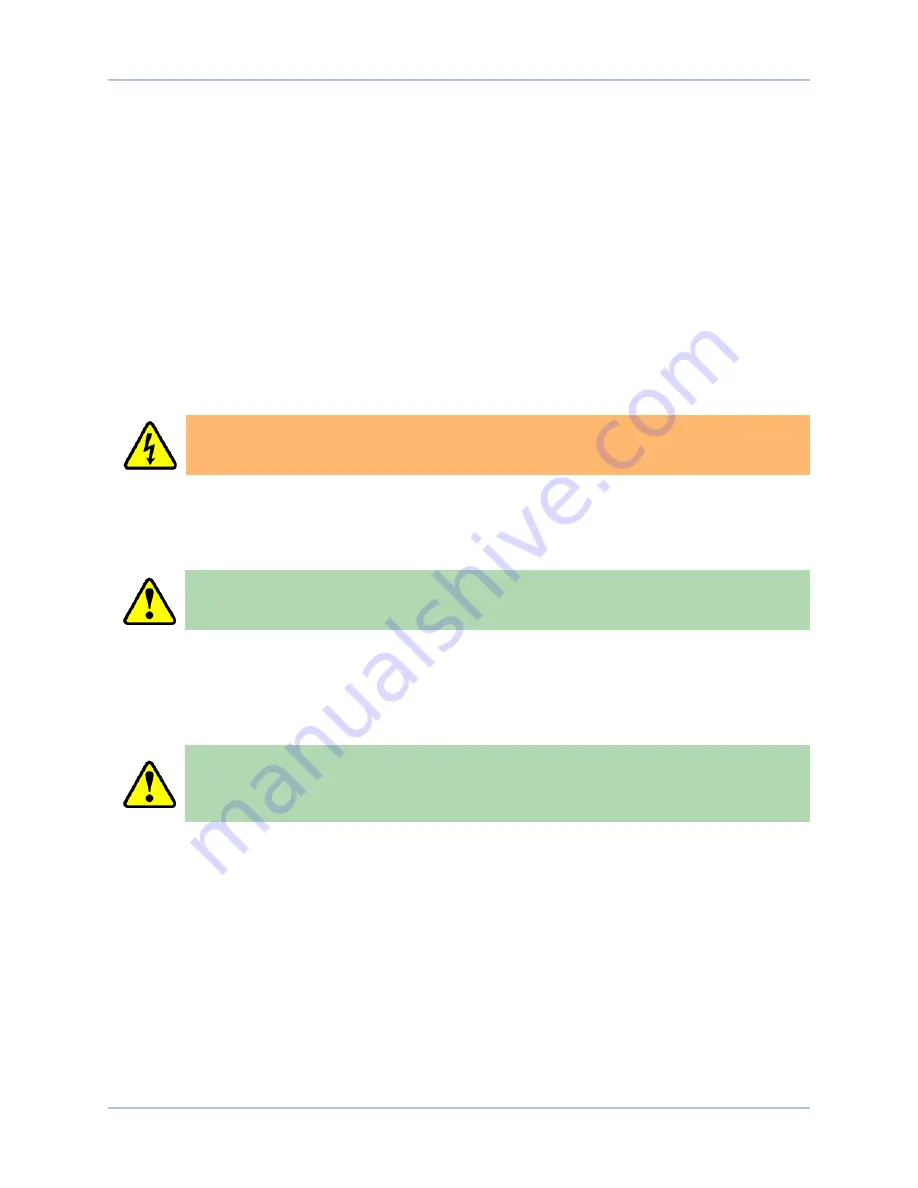
Maintenance
PRO560LM Hardware Manual
4.2. Cleaning and Lubrication
When cleaning and/or lubricating components of the PRO560LM series stages:
1. Be sure to use a clean, dry, soft, lint-free cloth for cleaning.
2. Before using a cleaning solvent on any part of the PRO560LM, blow away small particles and dust with
clean, dry, compressed air.
3. Take the opportunity during the lubrication procedure to inspect the motion guides or bearings for any
damage or signs of wear.
4. In applications that have multiple stages bolted together to form multi-axis systems, the orthogonality
may be lost if the stage tables of the support stages are loosened. Precision aligned stages should not
be loosened or disassembled.
5. Further disassembly of the stage is not recommended because proper assembly and calibration can
only be done at the factory . In addition, an autocollimator is required for post assembly verification to
maintain warranties. Contact Aerotech for more information.
D A N G E R : To minimize the possibility of bodily injury or death, disconnect all electrical
power prior to performing any maintenance or making adjustments to the equipment.
Cleaning
If a solvent is necessary for cleaning the stage, Aerotech recommends using isopropyl alcohol. Harsher
solvents, such as acetone, may damage the plastic and end caps on the bearing trucks.
W A R N I N G : Make sure that all solvent has completely evaporated before attempting to
move the stage.
Lubrication
Aerotech recommends that you use only Kluberplex BEM 34-132 as the standard lubricant for second
generation PRO560LM stages. Second generation stages can be distinguished from first generation stages
by the curved hardcover on the second generation stage.
W A R N I N G : First generation stages were manufactured with THK AFE-CA grease as the
standard lubricant. THK AFE-CA grease is not chemically compatible with Kluberplex BEM 34-
132 and the two should not be used interchangeably. First generation stages in the field should
continue to use THK AFE-CA grease for regular maintenance lubrication.
For high-speed applications (i.e., near maximum speed at a duty cycle of 50%), frequent maintenance with
standard lubricants is required.
If the application process uses only a small portion of travel for most of the duty cycle, periodically drive the
stage through full travel to redistribute the lubrication in the bearings.
42
Chapter 4
www.aerotech.com