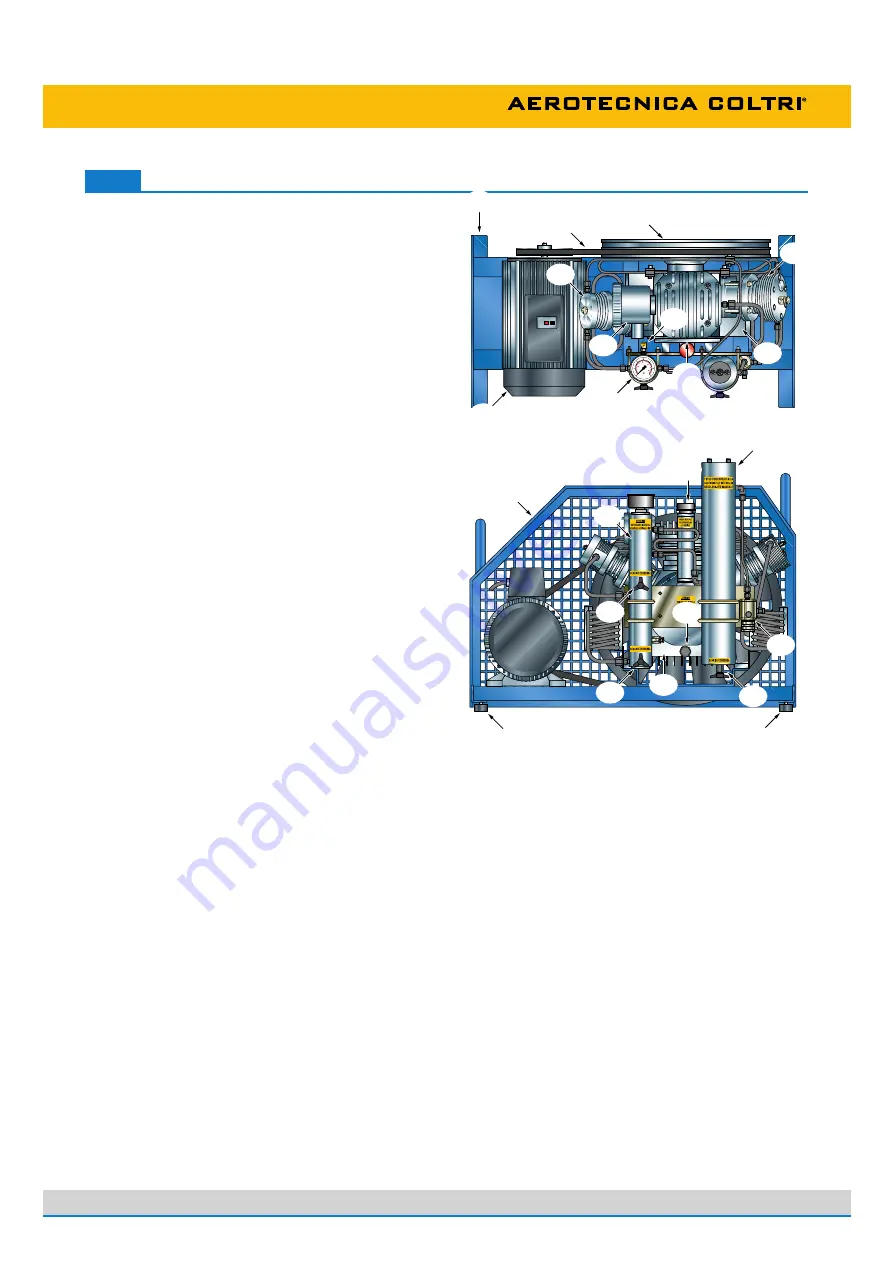
pag.
29 di 64
Use and Maintenance Manual
M
MCCHH88--1111//EEM
M -- M
MCCHH1133--1166//EETT
Standard
Cap.4 _ Technical data
MACHINE PARTS
4.2
1
Frame
2
Cover
3
Motor (electric or internal combustion type)
4
Compressor
5
Pressure gauge
6
Intake filter
7
Final condensate separator
8
Active carbon air filter / molecular sieve
9
1
st
stage
10
2
nd
stage
11
3
rd
stage
12
Monobloc
13
Oil filler plug
14
Safety valve
15
Maintenance valve
16
Cooling fan
17
Belt
18
Anti-vibration device
19
Condensate discharge taps
20
Oil drain plug
1
2
3
5
6
7
8
4
11
9
10
12
13
14
15
16
17
18
18
19
19
19
20