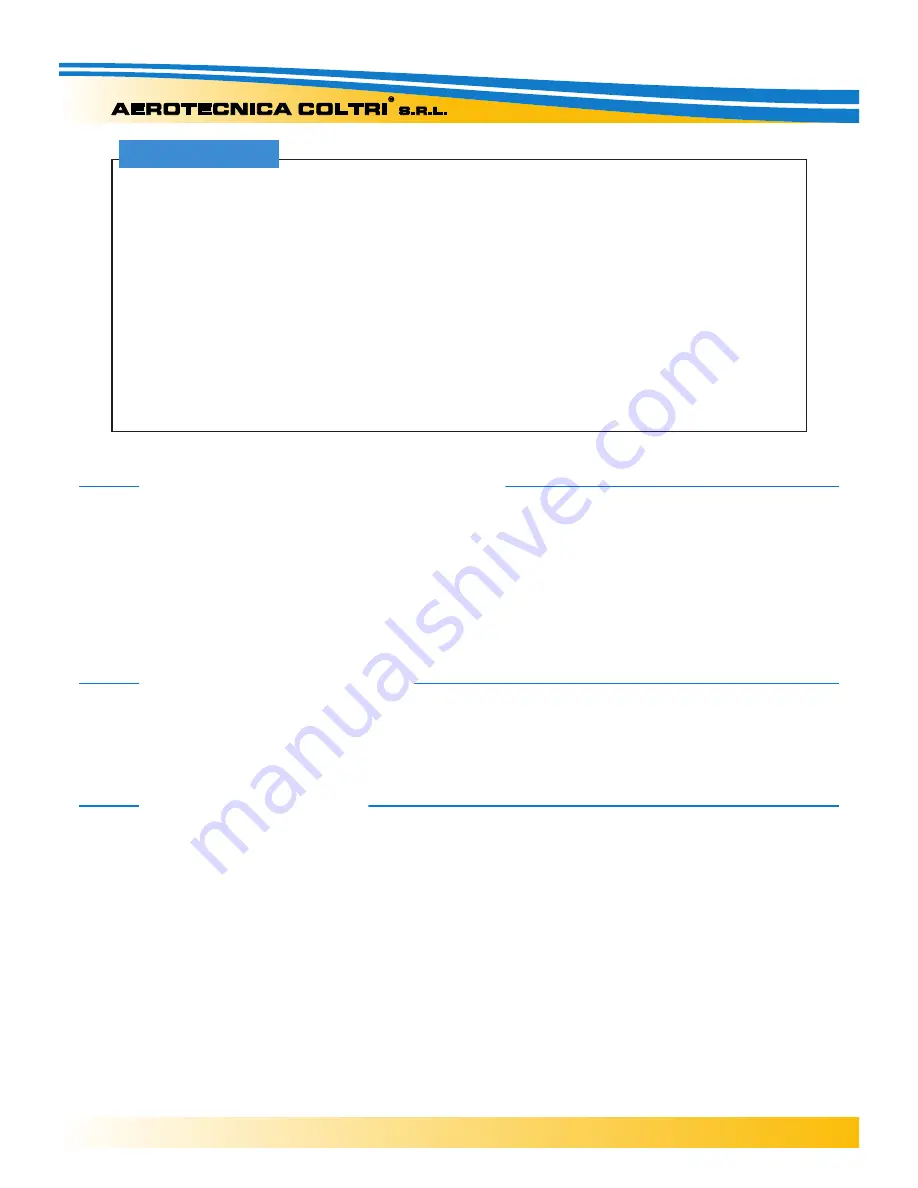
Cap.3 _ Safety regulations
pag.
20
Use and maintenance manual
MCH-36
- Never place hands or introduce screwdrivers, keys or other tools into moving parts.
- Never clean with flammable fluids.
- Periodically check the info plates/labels and restore/replace them where necessary.
- The workplace must be kept clean, tidy and free from objects that might hinder movement.
- Operators must avoid carrying out “awkward” tasks in uncomfortable positions that might cause
imbalance.
- Operators should be aware of the risk of entrapment caused by clothes or hair getting caught up
in moving parts; wear a cap to contain long hair.
- Necklaces, bracelets and rings can also be a source of danger.
- Workplace lighting must be adequate for the work in progress. Insufficient or excessive lighting
can generate risks.
- Always observe the instructions, accident prevention regulations and the warnings contained in
this manual.
IMPORTANT:
The compressor has been designed and built according to the state of the art and complies with technical
regulations in force concerning compressors for the production of high pressure breathing air. The laws,
regulations, standards and directives in force for such machines have been complied with.
Materials, parts, production procedures and quality controls all comply with the strictest safety and reliability
standards.
Using the compressor for the purposes described in this manual, handling it with due diligence and carrying
out maintenance and overhauls according to proper working practices will ensure long lasting performance
and functionality.
3.2.1 - IMPORTANT SAFETY INFORMATION
The manufacturer cannot be held liable for accidents that occur during use of the compressor as a result of the
user’s non-observance of the laws, regulations, standards and directives in force for high pressure compressors.
The compressor has been designed for use in weather conditions as described on page 15.
The constructor cannot be held liable for malfunction or damage if the compressor:
- is used for purposes other than that for which its is intended;
- is not handled or maintained according to the instructions specified in this manual;
- is not periodically and continually maintained as instructed or if non-original spare parts are used;
- machine parts are modified or replaced without written authorisation from the manufacturer, especially
where the efficiency of safety devices has been reduced or eliminated;
- where it is used outside the admissible temperature range.
3.2.2 - ACCIDENT PREVENTION
3.2.3 - WORKING SAFETY