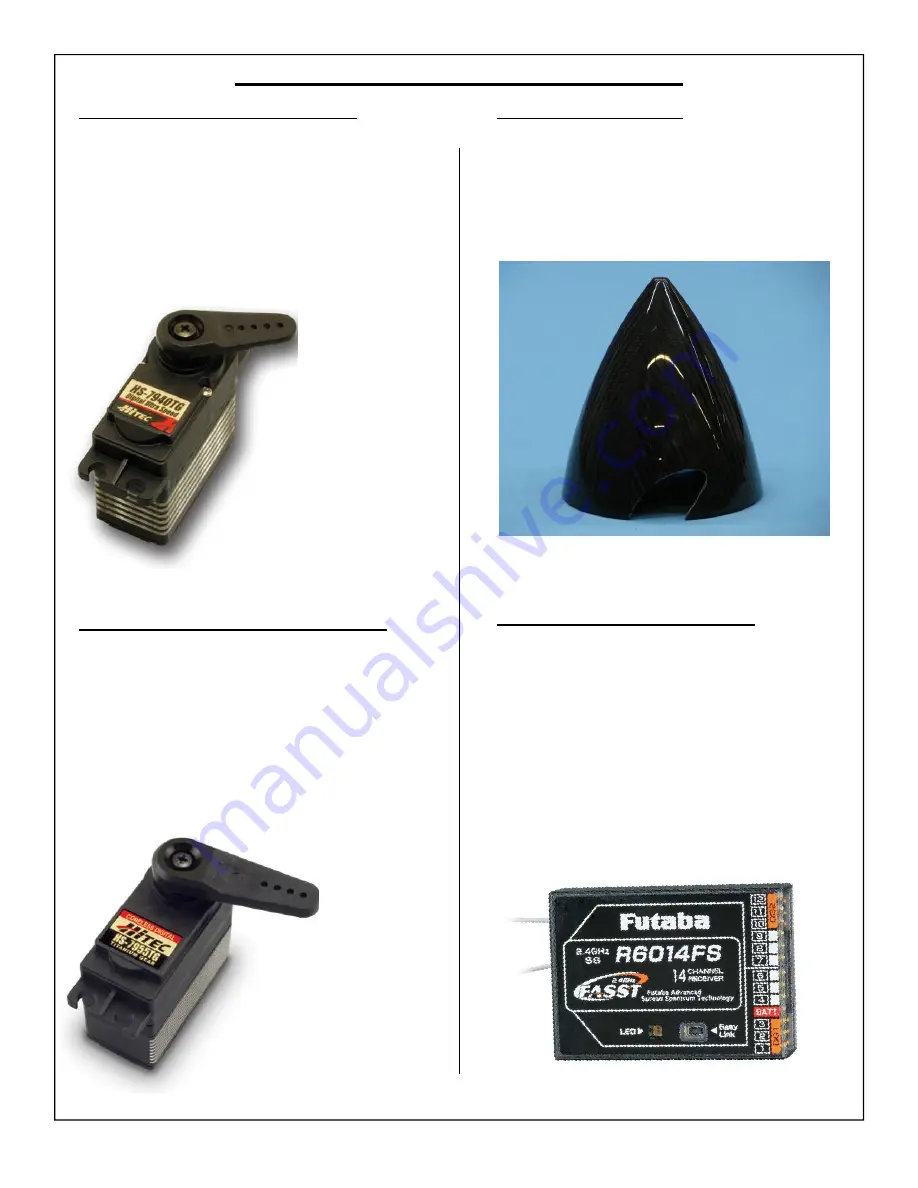
10
Servo Option 1 : Sport Performance
HARDEWARE NEEDED TO COMPLETE
Hitec 7940TG Servos may be used for sport flying.
If flying more aggressive aerobatics please see servo
option two below.
Note:
Servos available through Aeroworks
◊
8 - Hitec 7940TG Servos for flight surfaces
◊
1 - Hitec 5625MG Servo for throttle
Servo Option 2: Unlimited Performance
Hitec 7955TG Servos are recommended for unlim-
ited flying. These servos will provide the best per-
formance possible.
Note:
Servos available through Aeroworks
◊
7 - Hitec 7955TG Servos for flight surfaces
◊
1 - Hitec 5625MG Servo for throttle
Recommended Spinner:
◊
1 - 4” Spinner- Carbon Fiber Recommended
Note:
Spinner available from Aeroworks
Electronic Accessories : Receiver
A 12 or 14 channel receiver is recommended, using a
receiver with 12-14 channels will allow the builder to
mix both the aileron and elevator servos together in the
radio. Mixing these functions will result in a great flying,
well trimmed airplane.
◊
1 - 12-14 Channel 2.4 GHz or PCM Receiver
◊
4 - Aileron
◊
2 - Elevator
◊
2 - Rudder
◊
4 - Aileron
◊
2 - Elevator
◊
1 - Rudder