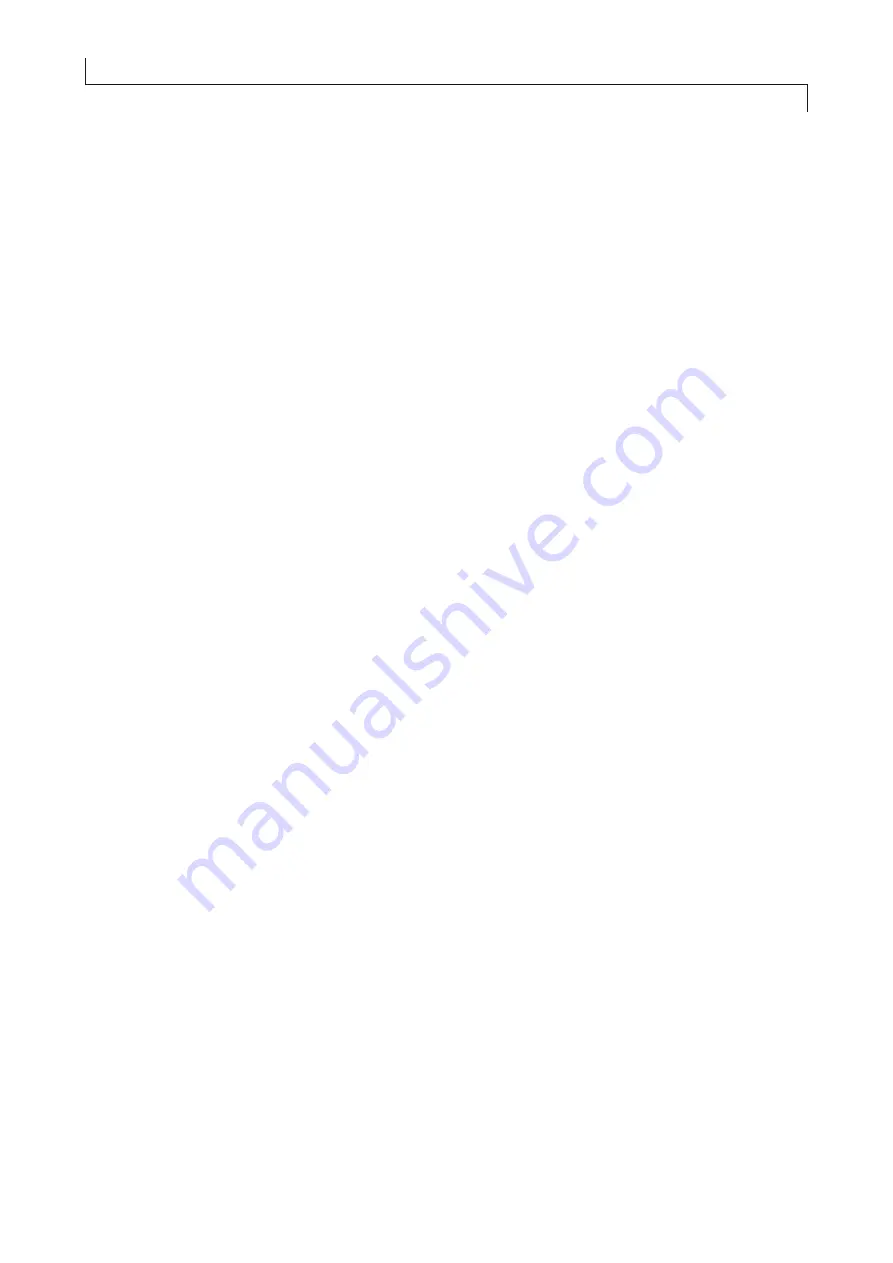
- 11 -
English
Chapter 2
SAfETy INforMATIoN
2.4.
Safety WarninGS related tO
incOrrect uSe
incorrect use that can be reasonably expected
– The predictable incorrect use consists of:
“the use of the machine
different from the indications given in the manual, that may
stem from the easily predictable human behaviour”.
the machine should be used only for bending the four lower
flaps of the cardboard box.
‒ The machine must be used ONLY for the uses intended by the
manufacturer.
‒ Do not allow the machine to be used by operators that are not
properly trained, informed and unauthorised.
‒ Packages that contain liquid or inconsistent products must ensure
that they do not leak.
‒ Do not use the machine as a workbench.
‒ Do not use or let the machine be used for purposes or in ways not
provided by the manufacturer.
‒ Do not use or make use of machines with defective, deactivated
and/or not perfectly installed safety devices.
‒ Do not continue to use the machine if malfunctions have been
detected.
Stop the machine immediately and restart it only after the normal
conditions of use have been restored.
‒ Never carry out an intervention with the machine enabled but only
after having stopped it properly, under safety conditions.
‒ Never use the machine without wearing the personal protective
devices indicated by the manufacturer and required by current
workplace laws.
‒ Never use the machine if the scheduled maintenance interventions
have not been carried out accordingly.
‒ Do not clean or wash the machine with aggressive products to
avoid damaging the components.
‒ Do not replace the components with non-original spare parts or
with different design and constructive features.
‒ Do not leave the machine unattended at the end of the work without
shutting it down first in safety conditions.
employer obligations
– The operator must be trained to acquire the skills required for the
packaging machine or an equivalent machine.
Upon completion of training, make sure the operator has understood
the contents in the use manual, especially the information regarding
safety.
– The operator must possess the required training and meet the
suitable conditions for carrying out the activities in safety conditions.
– The employer must inform the operator on the INCorrECT USES
predictable and on the persistent residual risks.