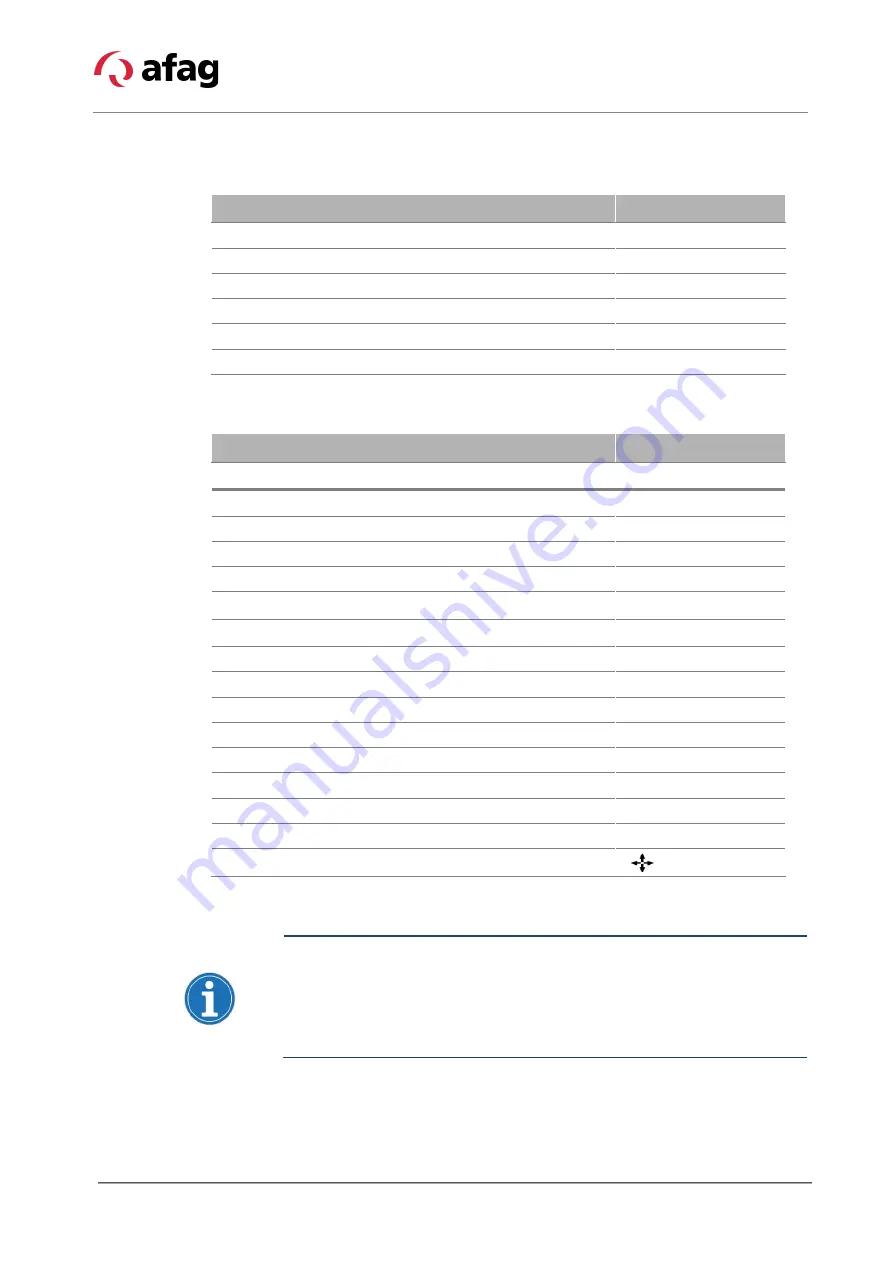
Technical data
20 – 50
Assembly instructions EN
DG 16
Edition 07/2020
Rev. 3.0
3.4 Technical data DG 16 (zero position 90°)
DG 16 (zero position 90°)
Attachment grid
30 mm
Operating pressure
6 ± 1 bar
Air connection P
M3
Operating temperature
10 – 40 °C
Storage temperature
0 – 50 °C
Air humidity
< 90 %
DG 16 (zero position 90°)
Order Number
50407663
Jaw stroke
2 x 3 mm
Net weight
0.275 kg
Max. payload
0.5 kgcm
2
Grip force
35 N
C
ylinder
⌀
gripper
16 / 4 mm
C
ylinder
⌀
rotation
20 / 10 mm
Monitoring of gripping
Open
Monitoring of rotation
0° / 180° or 90°
Angle of rotation
180°
Min. swivel time 180°
0.19 sec.
Noise level
< 65 dB(A)
Repeat accuracy
+/- 0.03 mm
Angle accuracy
+/- 0.05°
Torque
0.4 Nm
Assembly position
The technical data refer to a nominal pressure of 6 bar and the Afag standard
test conditions.
The gripper module can be operated with both oil-free and oiled
compressed-air.
Cleanroom class ISO 14644-1, class ISO 7.