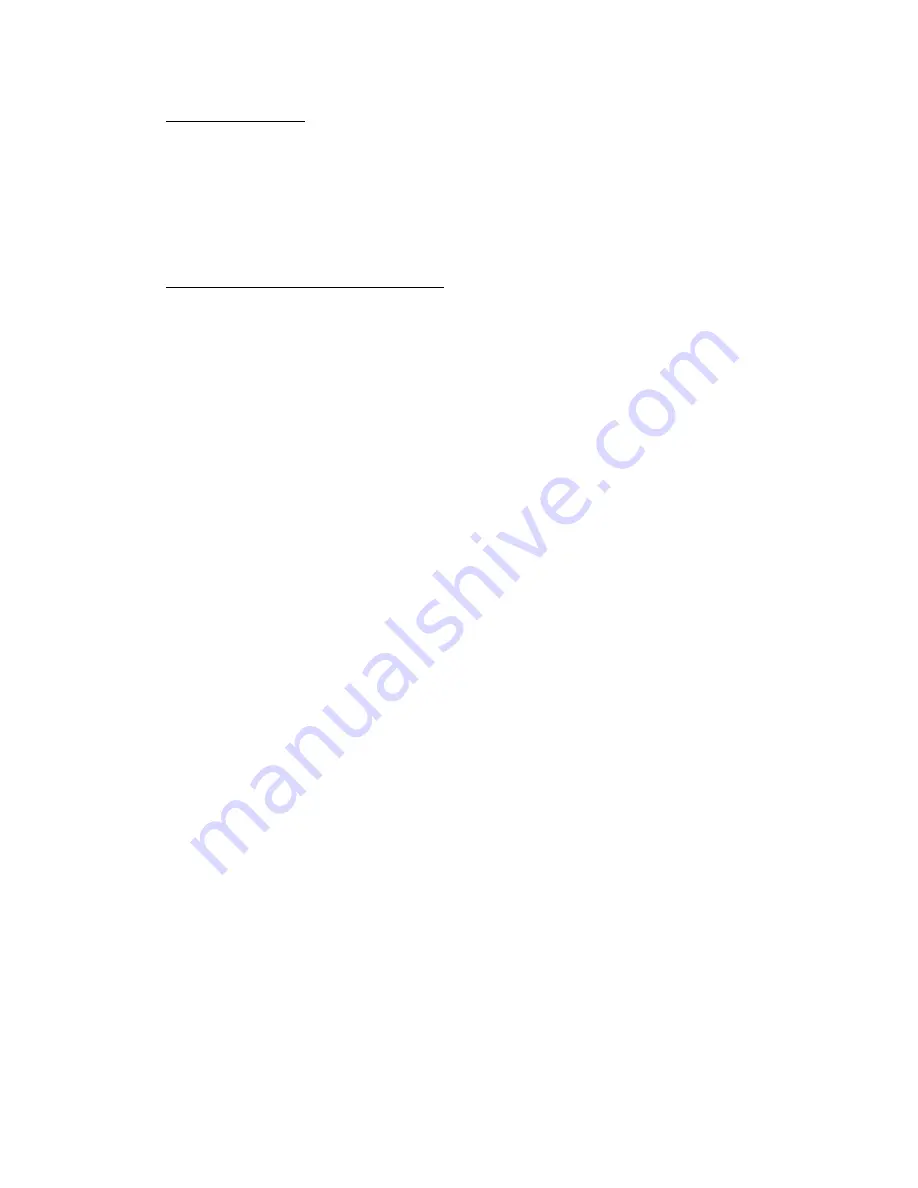
:
ANAPURNA L/XL
OPERATOR MANUAL
A
B]]]]]]]]]]]]]]]]]]]]]]]]]]]]]]]]]]]]]]]]]]]]]]]]]]]]]]]]]]]]]]]]]]]]]]]]]]]]]]]]]]]]]]]]]]]]]]]]]]]]]]]]]]]]]]]]]]]]]]]]]]]]]]]]]]]]]]]]]]]]]]]]]]]]]]]]]]]]]]]]]]]]]]]]]]]]]]]]]]]]]]]]]]]]]]]]]]]]]]]]]]]]]]]]]]]]]]]]]]]]]]]]]]]]
19
]
8/09/2006
]
7.3. Maintenance
- Always make sure, when printing “borderless”, that the belt is masked,
so printing on the belt is reduced to a minimum.
- When you have printed onto the Conveyor belt, try to remove the ink with a
cleaning solution.
7.4. Replacement of Conveyor belt
- Vacuum can become insufficient when the belt is completely printed.
The Conveyor belt therefore is a Spare Part, and can be ordered as such.