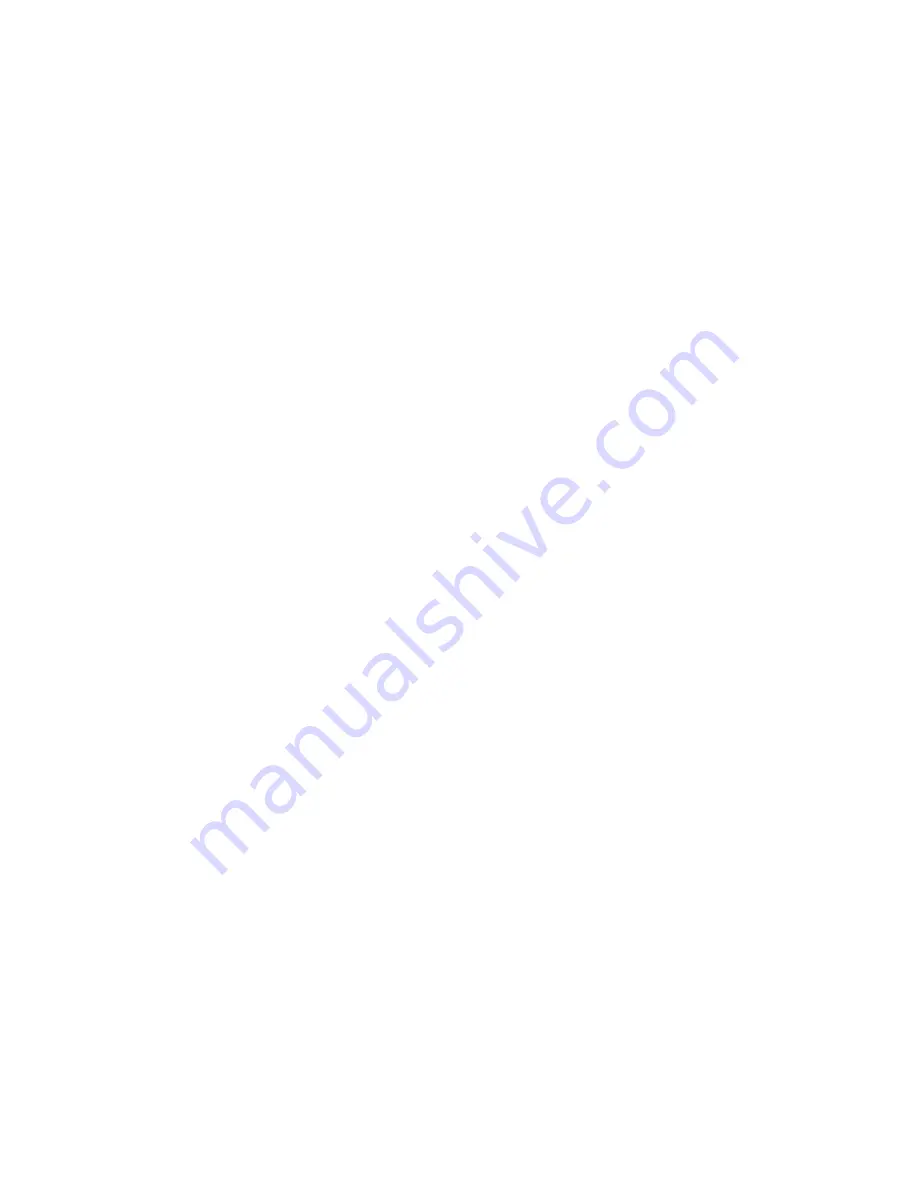
Alignment Procedures
97
Alignment Program (continued)
1050 !
1060 !
1070 !
1080 DEF FNDci(I_range)
! Function to read current
1090 COM
/Vm/
@Vm
1100
COM /Shunt/ Shunt_r
1110
IF I_range=2 THEN
! 2A must read across shunt
1120
Amps=FNDcv/Shunt_r
! Convert shunt voltage to Amps
1130
ELSE!
! <2A read direct from DMM
1140
OUTPUT @Vm;"DCI"
! Set DMM to read DC current
1150
TRIGGER @Vm
! Take a current reading
1160
ENTER @Vm;Amps
! Enter the current
1170 END
IF
1180
RETURN Amps
! Return the current reading
1190 FNEND
1200 !
1210 !
1220 !
1230 SUB Output_on
! Subprogram to turn ON outputs
1240
COM /Ps/ Chan,Other_chan, @Ps, Model$[7]
1250
COM /Outputs/ No_of_outputs
1260
OUTPUT @Ps; OUT l,l;OUT 2,1
! Turn on outputs 1 & 2
1270
IF No_of_outputs=4 THEN OUTPUT @Ps;"OUT 3,1;OUT 4,1"
1280
! Turn on outputs 3 & 4
1290 SUBEND
1300 !
1310 !
1320 !
1330 SUB Output_off
! Subprogram to turn OFF outputs
1340
COM /Ps / Chan, Other_chan, @Ps, Mode1$ [ 7 ]
1350
COM /Outputs/ No_of_outputs
1360
OUTPUT @Ps;"OUT 1,0,OUT 2,0"
! Turn off outputs 1 & 2
1370
IF No_of_outputs=4 THEN OUTPUT @Ps; “OUT 3,0;OUT 4,0”
1380
! Turn off outputs 3 & 4
1390 SUBEND
1400 !
1410 !
1420 !
1430 Cal_voltage : SUB Cal_voltage(V_range)
! Subprogram to cal voltage
1440
COM /Ps/ Chan,Other_chan,@Ps,Model$ [7]
1450 !
1460
IF V_range=50 THEN GOTO Cal_v
! Skip setup instructions
1470
Output_off
! Turn off all outputs
1480
Clear_screen
1490
PRINT "Set up output";Chan;"for voltage calibration
1500
1510
PRINT " Use Fig A-1 of the Operating Manual"
1520
1530
PRINT “ 3458A input is connected to VOLTAGE terminals”
1540
1550
PRINT " The current shunt is NOT used"
1560
Summary of Contents for 6625A
Page 10: ......
Page 24: ......
Page 30: ......
Page 44: ......
Page 62: ......
Page 68: ...Remote Operation 68 Figure 5 2 Sheet 1 of 2 Syntax Forms For Power Supply Commands ...
Page 69: ...Remote Operation 69 Figure 5 2 Sheet 2 of 2 Syntax Forms For Power Supply Commands ...
Page 90: ......
Page 94: ...Alignment Procedures 94 Figure A 3 Figure A 4 Figure A 5 ...
Page 116: ......
Page 120: ......