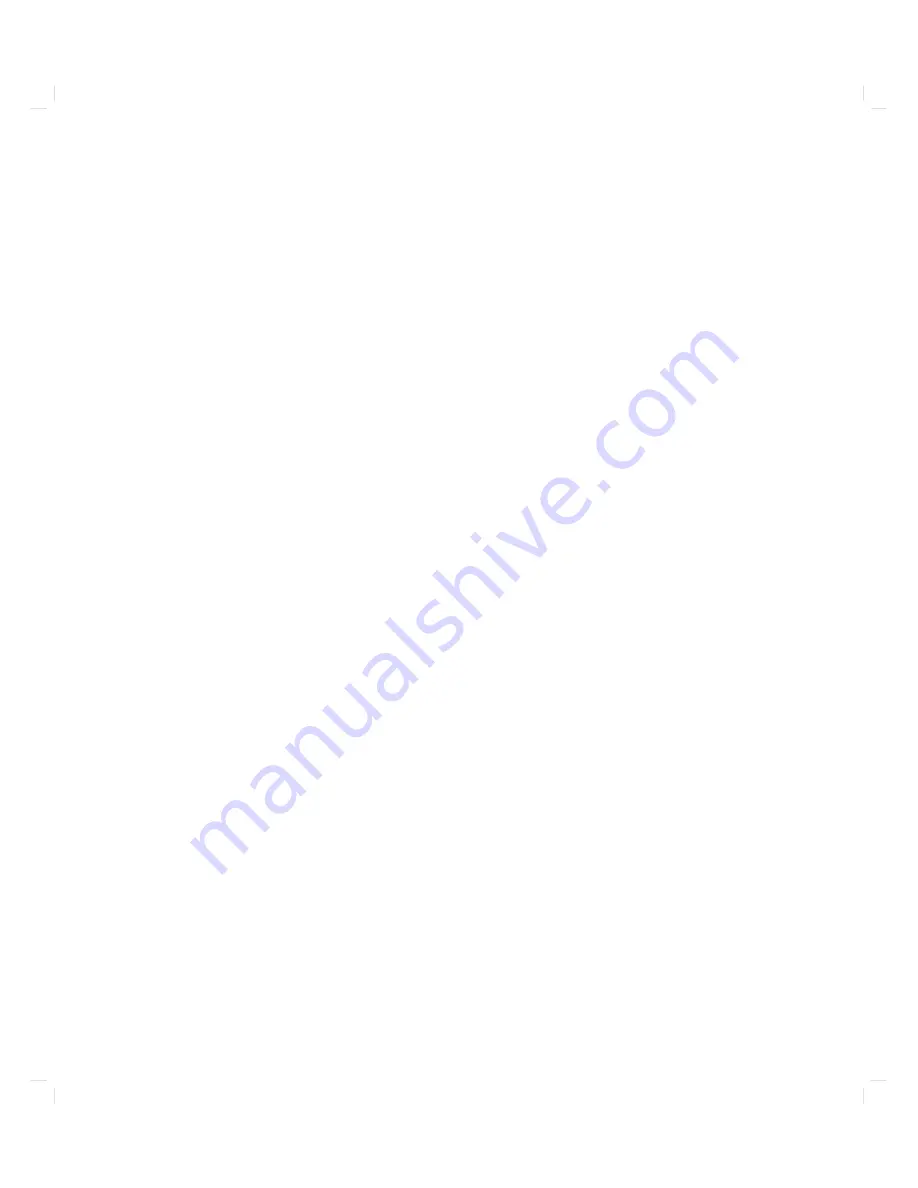
Line
P
ower
Module
The
line
power
module
includes
the
line
power
switch,
voltage
selector
switch,
and
main
fuse
.
The
line
power
switch
is
activated
from
the
front
panel.
The
voltage
selector
switch,
accessible
at
the
rear
panel,
adapts
the
analyzer
to
local
line
voltages
of
approximately
115V
or
230V
(with
350
V
A
maximum).
The
main
fuse
,
which
protects
the
input
side
of
the
preregulator
against
drawing
excessive
line
current,
is
also
accessible
at
the
rear
panel.
Refer
to
the
HP
8752C
Network
Analyzer
Installation
and
Quick
Start
Guide
for
line
voltage
tolerances
and
other
power
considerations
.
Preregulated
V
oltages
The
switching
preregulator
converts
the
line
voltage
to
several
DC
voltages
.
The
regulated
+5V
digital
supply
is
routed
directly
to
the
motherboard.
The
following
partially
regulated
voltages
are
routed
through
A15W1
to
the
A8
post
regulator
for
nal
regulation:
+70V
+25V
+18V
018V
+8V
08V
Regulated
+5V
Digital
Supply
The
+5VD
supply
is
regulated
by
the
control
circuitry
in
the
A15
preregulator
.
It
is
routed
directly
to
the
motherboard,
and
from
there
to
all
assemblies
requiring
a
low
noise
digital
supply
.
A
+5V
sense
line
returns
from
the
motherboard
to
the
A15
preregulator
.
The
+5V
CPU
is
derived
from
the
+5
VD
in
the
A8
post
regulator
and
goes
directly
to
the
A19
GSP
.
In
order
for
the
preregulator
to
function,
the
+5V
digital
supply
must
be
loaded
by
one
or
more
assemblies
,
and
the
+5V
sense
line
must
be
working.
If
not,
the
other
preregulated
voltages
will
not
be
correct.
Shutdown
Indications:
the
Green
LED
and
Red
LED
The
green
LED
is
on
in
normal
operation.
It
is
o
when
line
power
is
not
connected,
not
switched
on,
set
too
low
,
or
if
the
line
fuse
has
blown.
The
red
LED
,
which
is
o
in
normal
operation,
lights
to
indicate
a
fault
in
the
+5V
supply
.
This
may
be
an
over/under
line
voltage
,
over
line
current,
or
overtemperature
condition.
Refer
to
the
troubleshooting
chapters
for
more
information.
Theory
of
Operation
12-7
Summary of Contents for 8752C
Page 22: ...Before Applying Power 15 6 Servicing 15 6 Index Contents 16 ...
Page 38: ......
Page 43: ...Figure 2 1 Measurement Uncertainty Window System Veri cation and Performance Tests 2 5 ...
Page 116: ......
Page 122: ...Figure 3 1 Location of Major Assemblies 3 6 Adjustments and Correction Constants ...
Page 176: ......
Page 192: ...4 16 Start Troubleshooting Here ...
Page 193: ......
Page 195: ...Figure 4 7 HP 8752C Overall Block Diagram 3 of 4 Option 006 4 20 Start Troubleshooting Here ...
Page 197: ......
Page 221: ...5 24 Power Supply Troubleshooting ...
Page 222: ......
Page 271: ...Figure 7 21 A14 Generated Digital Control Signals Source Troubleshooting 7 31 ...
Page 302: ......
Page 366: ......
Page 378: ...Figure 11 4 Typical ED Re ection Test Port 11 12 Error Terms ...
Page 380: ...Figure 11 5 Typical ES Re ection Test Port 11 14 Error Terms ...
Page 382: ...Figure 11 6 Typical ER Re ection Test Port 11 16 Error Terms ...
Page 386: ...Figure 11 9 Typical ET 11 20 Error Terms ...
Page 407: ...Figure 12 5 High Band Operation of the Source Theory of Operation 12 21 ...
Page 410: ...Figure 12 6 Receiver Functional Group standard and Option 003 12 24 Theory of Operation ...
Page 411: ...Figure 12 7 Receiver Functional Group Option 003 and 004 Theory of Operation 12 25 ...
Page 412: ...Figure 12 8 Receiver Functional Group Option 006 12 26 Theory of Operation ...
Page 413: ...Figure 12 9 Receiver Functional Group Option 004 and 006 Theory of Operation 12 27 ...
Page 416: ......
Page 419: ...Figure 13 1 Module Exchange Procedure Replaceable Parts 13 3 ...
Page 423: ...Major Assemblies Replaceable Parts 13 7 ...
Page 425: ...Front Panel Assemblies Replaceable Parts 13 9 ...
Page 427: ...Rear Panel Assemblies Replaceable Parts 13 11 ...
Page 429: ...Cables Top View Replaceable Parts 13 13 ...
Page 431: ...Front Panel Cables and Attaching Hardware Replaceable Parts 13 15 ...
Page 433: ...Rear Panel Cables and Attaching Hardware Replaceable Parts 13 17 ...
Page 435: ...Source and Sampler Parts Standard and Option 003 Replaceable Parts 13 19 ...
Page 437: ...Source and Sampler Parts Option 004 006 Replaceable Parts 13 21 ...
Page 439: ...Source and Sampler Parts Options 004 and 003 004 Replaceable Parts 13 23 ...
Page 441: ...Source and Sampler Parts Option 006 Replaceable Parts 13 25 ...
Page 443: ...Display Bezel Assembly Replaceable Parts 13 27 ...
Page 445: ...Chassis Parts Replaceable Parts 13 29 ...
Page 447: ...Top View of Attaching Hardware and Post Regulator Fuses Replaceable Parts 13 31 ...
Page 449: ...Bottom View of Attaching Hardware Replaceable Parts 13 33 ...
Page 488: ......