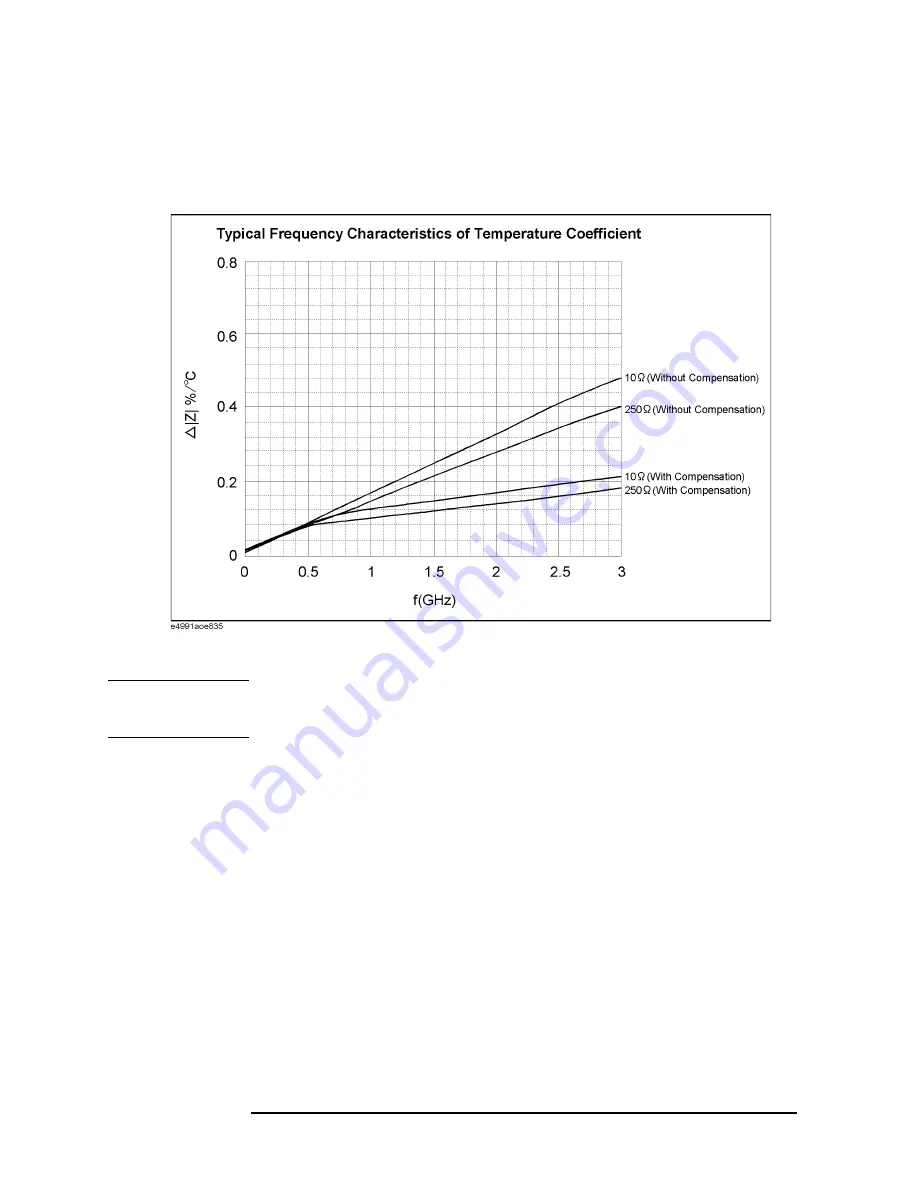
284
Chapter 11
Specifications and Supplemental Information
Option 007 Temperature Characteristic Test Kit
Figure 11-35
Typical frequency characteristics of temperature coefficient,
/
, when
|Zx|=10
Ω
and 250
Ω
,
are assumed.
NOTE
Read the value of |Z|%/
°
C at the material measurement frequency and multiply it by
to derive the value of
when
.
E
c
E
d
+
(
) Δ
T
E
ah
Z
sh
Y
oh
0
=
=
=
Δ
Δ
T
E
c
E
d
+
(
)
E
ah
Z
sh
Y
oh
0
=
=
=
Summary of Contents for E4991A
Page 6: ......
Page 24: ...18 Contents ...
Page 80: ...74 Chapter3 Setting Measurement Conditions Averaging Measurement Results ...
Page 220: ...214 Chapter9 Setup and Use of Control Management Functions System Recovery ...
Page 338: ...332 AppendixB Probe Station Connection Kit Option 010 OPEN SHORT LOAD Calibration ...
Page 428: ...422 AppendixD Menu References Menu References ...
Page 482: ...476 AppendixI Messages Wait measuring comp standard ...