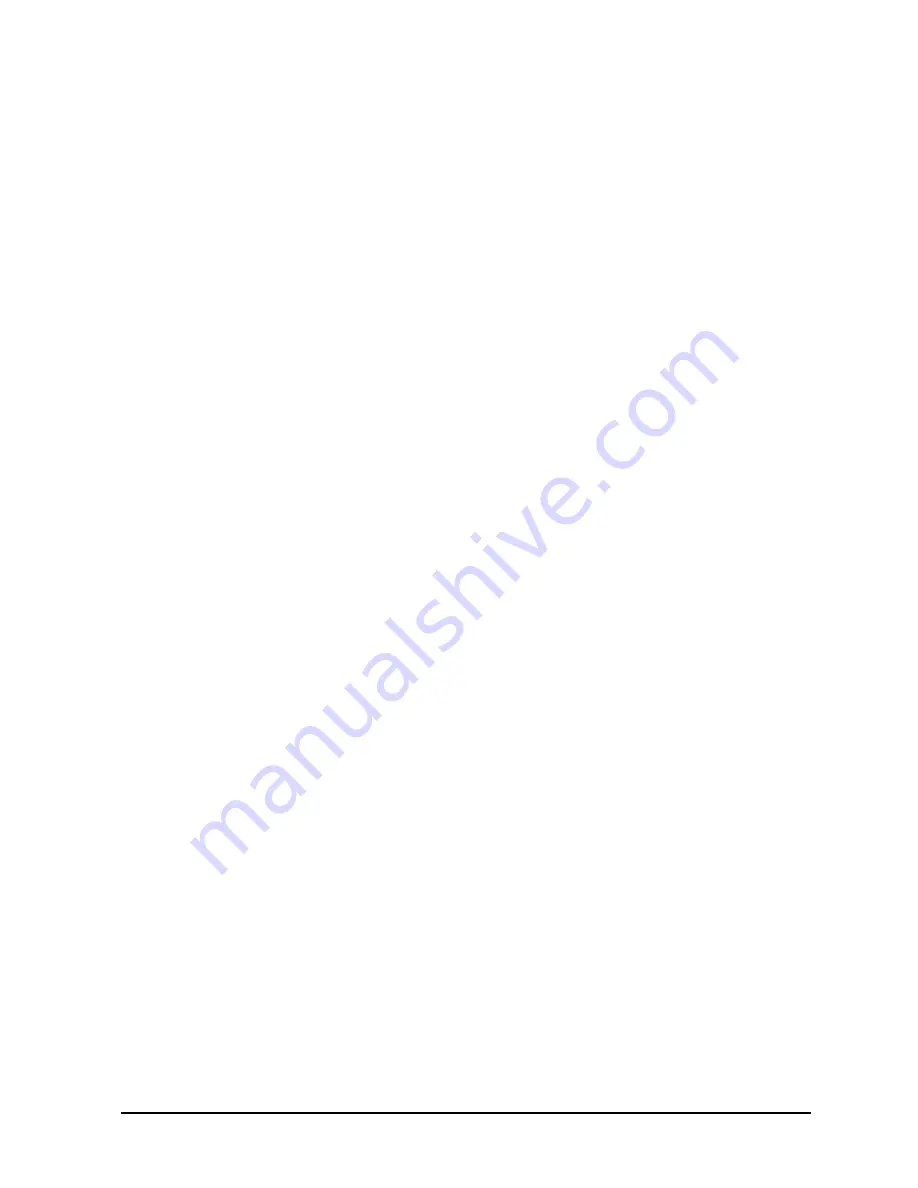
Service Guide E8364-90001
4- 45
PNA Series Microwave Network Analyzers
Troubleshooting
E8362A, E8363A, E8364A
Measurement System Troubleshooting
Checking the A20 LODA Output
Perform this test if you observe a problem in all bands on a single channel.
1. Refer to the block diagram at the back of this chapter and to
.
Locate cables W11, W12, W13, and W14, at the A20 LODA.
2. Using a 5/16-inch torque wrench, disconnect the cable associated with the faulty
channel (W11, W12, W13, or W14) and connect the spectrum analyzer to the A20 LODA
connector.
3. Set the network analyzer to any one of the frequencies listed in
4. Set the spectrum analyzer to measure the corresponding A18 output frequency listed in
5. If the signal is not present, replace the A20 LODA. Refer to
6. If the signal is present, reconnect the cable, and go to
“Checking the Receiver Group” on
Checking the A11 Phase Lock YTO Tune Output
1. Perform the Serial Bus Test. Refer to
“Serial Bus Test” on page 4-32
.
2. Examine the “Phase Lock, Node 315” entry in the test results.
3. If the result at Node 315 passes the test, the A12 source 20 is faulty; replace it. Refer to
“Removing and Replacing the A12 Source 20” on page 7-22
.
4. If the result at Node 315 fails the test, the A11 phase lock board is faulty; replace it.
Refer to
“Removing and Replacing the A11 Phase Lock Board” on page 7-20
Summary of Contents for E8362A
Page 11: ...Service Guide E8364 90001 1 1 1 Safety and Regulatory Information ...
Page 19: ...Service Guide E8364 90001 2 1 2 General Product Information ...
Page 29: ...Service Guide E8364 90001 3 1 3 Tests and Adjustments ...
Page 79: ...Service Guide E8364 90001 4 1 4 Troubleshooting ...
Page 139: ...Service Guide E8364 90001 5 1 5 Theory of Operation ...
Page 169: ...Service Guide E8364 90001 6 1 6 Replaceable Parts ...
Page 215: ...Service Guide E8364 90001 7 1 7 Repair and Replacement Procedures ...
Page 287: ...Service Guide E8364 90001 A 1 A Error Terms ...
Page 303: ...Service Guide E8364 90001 B 1 B Option Enable Utility ...
Page 309: ...Service Guide E8364 90001 C 1 C Firmware Upgrades ...
Page 313: ...Service Guide E8364 90001 D 1 D Operating System Recovery ...