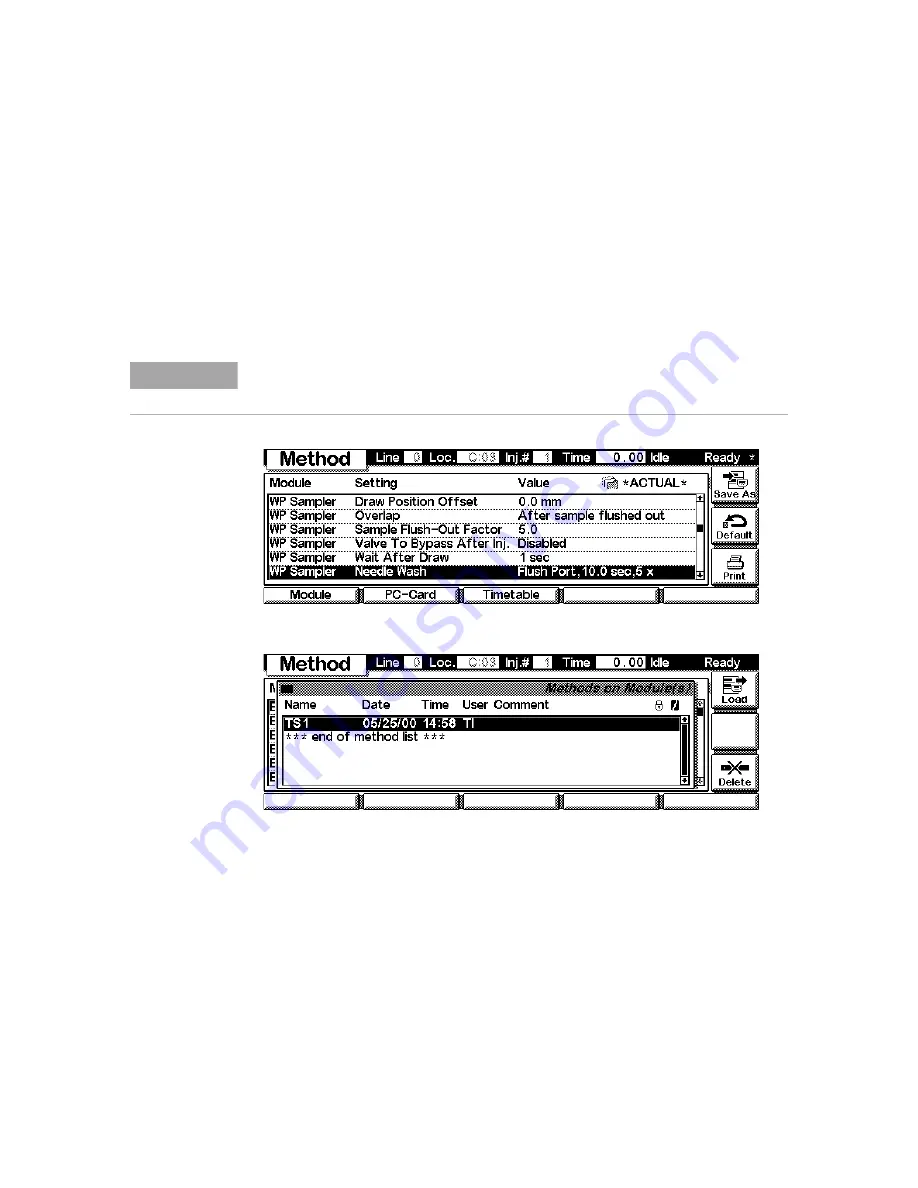
Control Module Screens of the Well-plate Samplers
8
1100 Series WS MWS Reference Manual
257
Method screens
Use
Esc
to return to the
Analysis
screen. Use the
F3
-key (
Method
) to view the
parameters in a method. Use the
F8
-key (
Save As
) to save the method in the
mdodule(s). The PC-Card-key is only active when a PCMCIA card is inserted in
the control module.
Use
F2
-key (
PC-Card
) to save a method on a PCMCIA card.
N O T E
The PCMCIA card must have been inserted into the control module prior to the last start-up
in order to be recognized.
Summary of Contents for G1367A
Page 1: ...s1 Agilent 1100 Series Well plate Sampler Micro Well plate Sampler Reference Manual...
Page 4: ...4 1100 Series WS MWS Reference Manual...
Page 42: ...42 1100 Series WS MWS Reference Manual 1 Installing the Sampler...
Page 156: ...156 1100 Series WS MWS Reference Manual 4 Repairing the Sampler...
Page 196: ...196 1100 Series WS MWS Reference Manual 5 Parts and Materials...
Page 214: ...214 1100 Series WS MWS Reference Manual 6 Introduction to the Well plate Sampler...
Page 240: ...240 1100 Series WS MWS Reference Manual 7 Theory of Operation...
Page 276: ...276 1100 Series WS MWS Reference Manual 9 Specifications...
Page 284: ...284 1100 Series WS MWS Reference Manual Index...
Page 285: ......