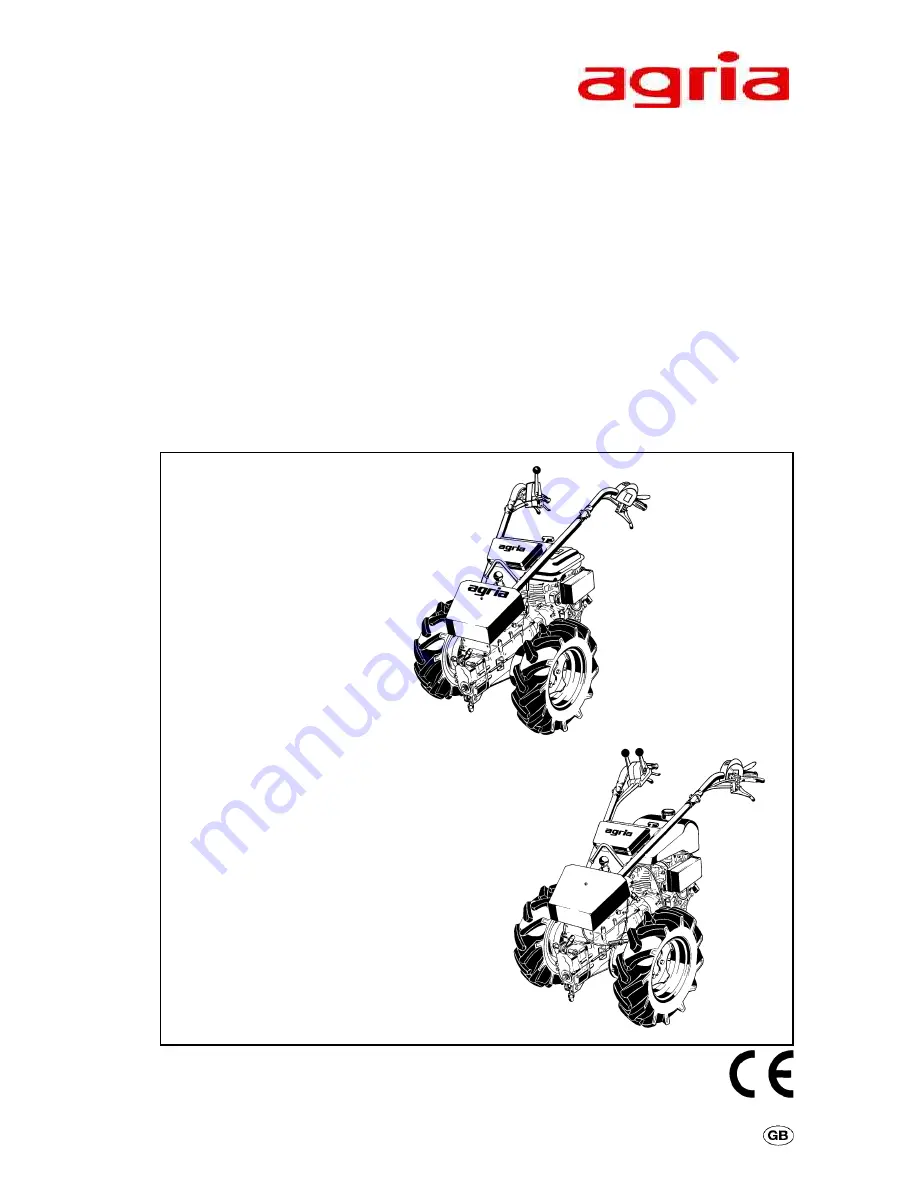
Before commissioning the machine, read operating
instructions and observe warnings and safety instructions!
Operating Instructions No. 998 766-B
03.12
&
Tool Carrier
5500 Grizzly
- compact
- comfort
- premium
Operating Instructions
Translation of the original operating instructions
4436, 4672_1
compact:
- Differential
- Safety hillholder
- Petrol engine EH 25 D
comfort:
- Differential
- Safety hillholder
- Petrol engine EH 34 D
premium:
- Steering brake clutch
- Brake central
- Petrol engine EH 25 D
- Petrol engine EH 34 D