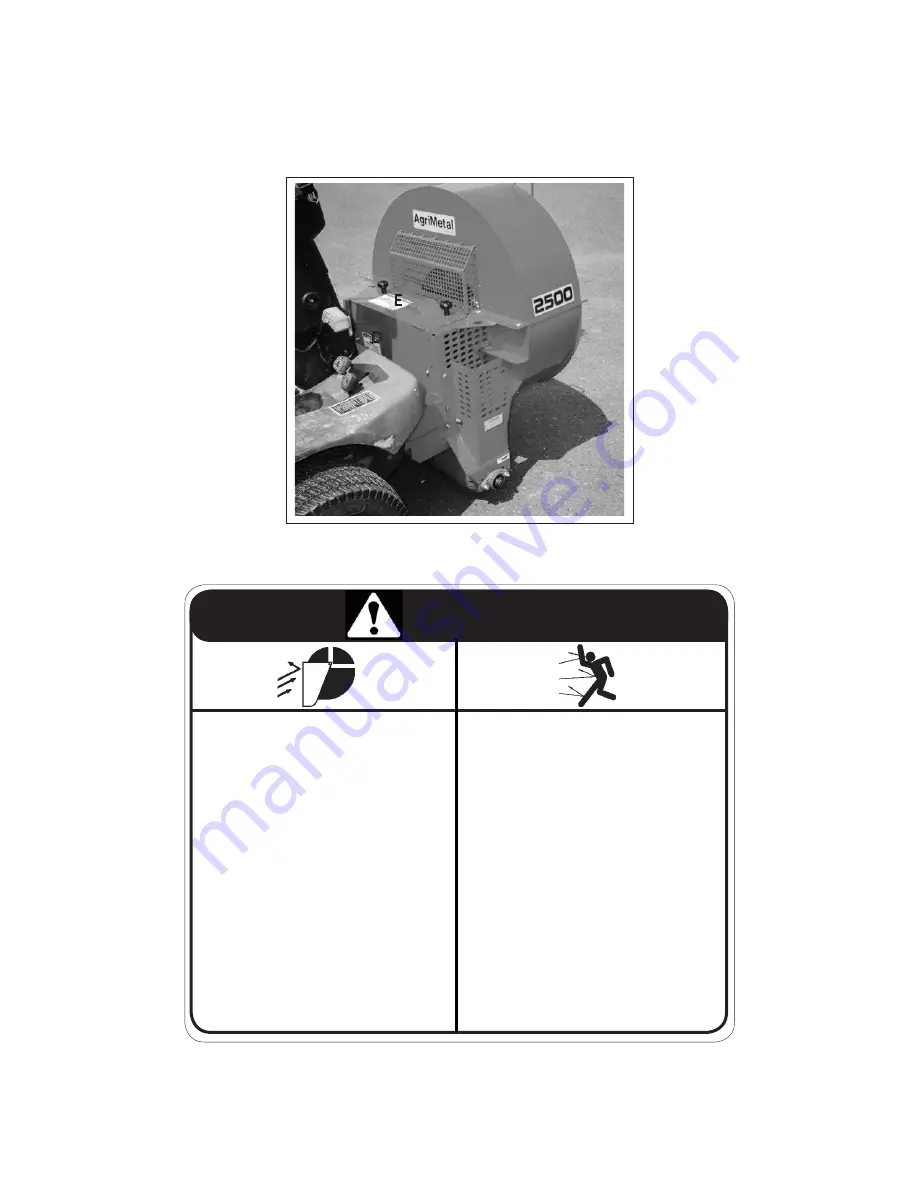
11
The types of safety signs and locations on the equipment are shown in the illustrations that follow. Good
safety requires that you familiarize yourself with the various safety signs, the type of warning and the
area, or particular function related to that area, that requires your SAFETY AWARENESS.
• Think SAFETY! Work SAFELY!
REMEMBER - If safety signs have been damaged, removed, become illegible or parts replaced without
safety signs, new signs must be applied. New safety signs are available from your authorized dealer.
B
DANGER
RISQUE D'OBJETS PROJETÉS
À défaut de suivre ces instructions,
cela pourrait entraîner de sérieuses
blessures ou même la mort.
1.
Arrêter le moteur, placer tous les
contrôles à la position "neutre", enlever
la clé du contact et attendre que toutes
les places soient au point mort avant
de faire tout ajustement, réparation ou
de débloquer la machine.
2.
Afin d'éviter tout risque d'accident
grave, ne jamais souffler en direction
des gens, des animaux ou vers les
propriétés. Le port des équipements
de sécurité est obligatoire lorsque vous
opérez la machine.
3.
Garder les gens éloignés de la ma
chine.
To prevent serious injury or death
from a thrown object:
1. Stop engine, place all controls in
neutral, set park brake, remove igni-
tion key and wait for all moving parts
to stop before servicing, adjusting,
repairing or unplugging machine.
2. Do not direct discharge chute toward
people, animals or property. Always
wear appropriate safety gear. Keep
hands and feet out of discharge open-
ings.
3. Keep others away.
THROWN OBJECT HAZARD
NC13-33-0110
E
D