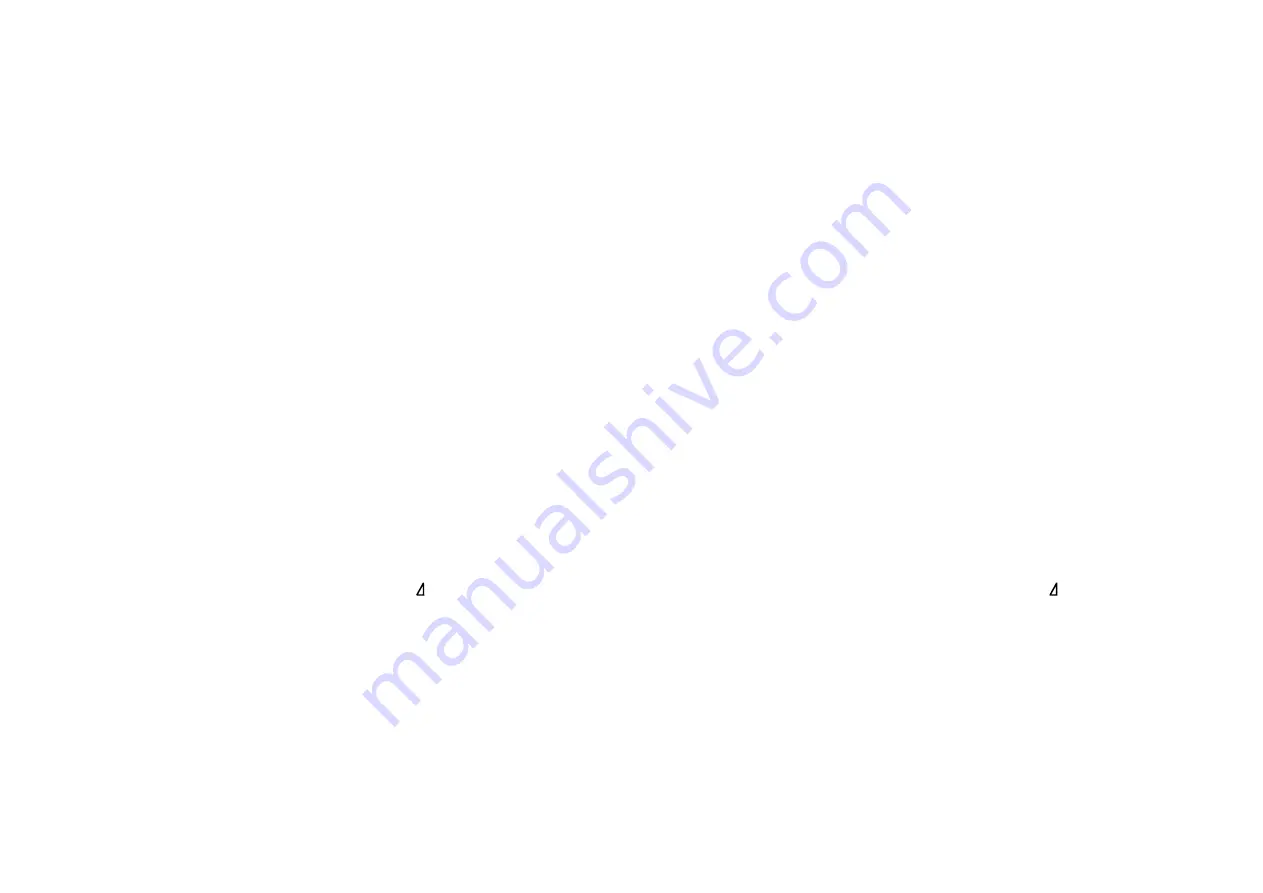
3-6
K65C/K75C/K95C
3-6
K65C/K75C/K95C
o
3.2.11 Hydraulic system
- Contents
100 l
- Hydraulic oil reservoir
70 l
- Flow rate
61 l/min
- Max. operating pressure
230 bar
- 2 lifting cylinders
Ø 80/50 mm
- 1 tilt cylinder
Ø 100/60 mm
- 1 steering cylinder
Ø 85/35 mm
- Times acc. to DIN ISO 7131
- Lift (with payload)
5.8 s
- Lower (without payload)
3.8 s
- Dump 90°
1.2 s
- Tilt 45°
1.0 s
3.2.12 Fuel supply system
- Contents
fuel tank
70 l
3.2.13 Heating and ventilation system
- Oil heater
COBO
- Type
2/9008/COMB-10/A45
- Heat output,
3-stage
Q
80
max. 10.5 kW at V
oil
30 l/min
- Fan power,
3-stage
max. 785 m³/h
3.2.14 Return-flow suction filter
- Filter mesh
15 µm abs.
- By-pass activation pressure
p = 2.5 bar
- Pretension
0.5 bar
3.2.15 Electrical contamination indicator
- Activation pressure
p = 2 bar
3.2.16 Oil cooler with temperature-controlled fan
- Power
max. 15 kW
- Flow rate
23 l/min
o
3.2.11 Hydraulic system
- Contents
100 l
- Hydraulic oil reservoir
70 l
- Flow rate
61 l/min
- Max. operating pressure
230 bar
- 2 lifting cylinders
Ø 80/50 mm
- 1 tilt cylinder
Ø 100/60 mm
- 1 steering cylinder
Ø 85/35 mm
- Times acc. to DIN ISO 7131
- Lift (with payload)
5.8 s
- Lower (without payload)
3.8 s
- Dump 90°
1.2 s
- Tilt 45°
1.0 s
3.2.12 Fuel supply system
- Contents
fuel tank
70 l
3.2.13 Heating and ventilation system
- Oil heater
COBO
- Type
2/9008/COMB-10/A45
- Heat output,
3-stage
Q
80
max. 10.5 kW at V
oil
30 l/min
- Fan power,
3-stage
max. 785 m³/h
3.2.14 Return-flow suction filter
- Filter mesh
15 µm abs.
- By-pass activation pressure
p = 2.5 bar
- Pretension
0.5 bar
3.2.15 Electrical contamination indicator
- Activation pressure
p = 2 bar
3.2.16 Oil cooler with temperature-controlled fan
- Power
max. 15 kW
- Flow rate
23 l/min
Summary of Contents for AL 65
Page 8: ...Safety regulations...
Page 29: ...Signs...
Page 38: ...Technical data...
Page 60: ...Description...
Page 72: ...Operation...
Page 83: ...Attachments...
Page 91: ...Rescue towing lashing lifting by crane...
Page 100: ...Maintenance...
Page 120: ...Malfunctions causes and remedies...
Page 123: ...Protection against theft...
Page 126: ...Appendices...
Page 127: ......
Page 128: ......
Page 131: ......
Page 134: ...K65C K75C K95C K65C K75C K95C B B...
Page 135: ...K65C K75C K95C K65C K75C K95C C C...
Page 136: ...K65C K75C K95C K65C K75C K95C D D...
Page 137: ...K65C K75C K95C K65C K75C K95C E E...
Page 138: ...K65C K75C K95C K65C K75C K95C F F...