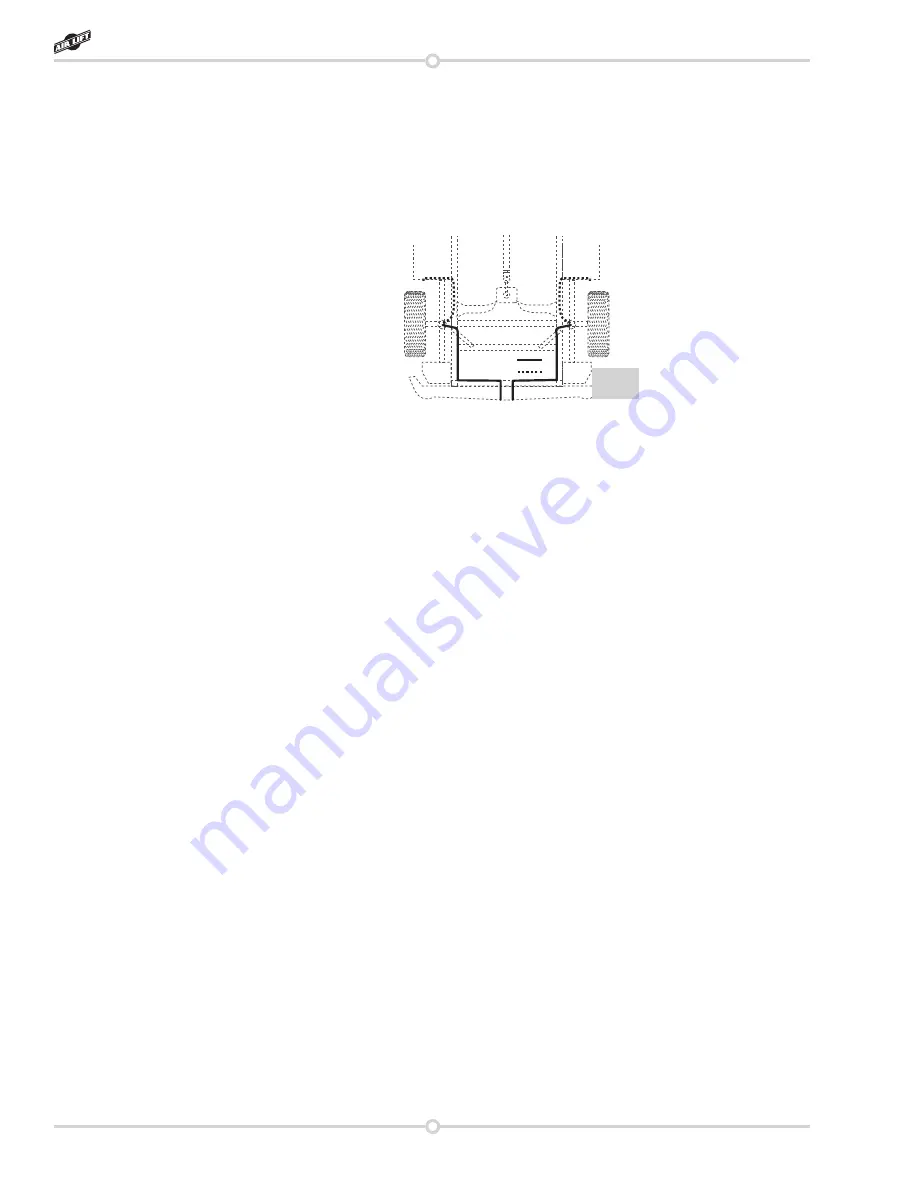
8
MN-282
5. Push the inflation valve through the hole and use the rubber washer, flat washer, and
another 5/16” nut. Tighten the nuts to secure the assembly in place (fig. 8).
6. Route the air line along the frame to the air fitting on the air spring (fig. 9). Keep AT
LEAST 6” of clearance between the air line and heat sources, such as the exhaust pipes,
muffler, or catalytic converter. Avoid sharp bends and edges. Use the plastic tie straps
(BB) to secure the air line to fixed, non-moving points along the chassis. Be sure that
the tie straps are tight, but do not pinch the air line. Leave at least 2” of slack to allow for
any movement that might pull on the air line.
7.
Cut off air line leaving approximately 12” of extra air line. A clean square cut will ensure
against leaks (see fig. 7). Insert the air line into the air fitting. This is a push to connect
fitting. Simply push the air line into the 90° swivel fitting until it bottoms out (9/16” of air
line should be in the fitting).
ALIGNING THE AIR SPRING
1.
VERY IMPORTANT
- With the top and bottom still loose, inflate the air springs to
approximately 10 p.s.i. Use the slots in the brackets to correctly align the air spring
between the upper and lower brackets. This can be accomplished by tapping it inboard
or outboard for proper alignment. There should be symmetrical cushion of air around
the base of the air spring when correctly positioned.
CHECKING FOR LEAKS
1. Inflate the air spring to 30 p.s.i. and spray all connections and the inflation valves with
a solution of 1/5 liquid dish soap and 4/5 water to check for leaks. Spot leaks easily by
looking for bubbles in the soapy water.
2. After the test, deflate the springs to the minimum pressure required to restore the normal
ride height, no less than 5 p.s.i.
3.
Check the air pressure again after 24 hours. A 2-4 p.s.i. loss after initial installation is
normal. Retest for leaks if the loss is more than 5 lbs.
FIXING LEAKS
1. If there is a problem with the swivel fitting:
a. Check the air line connection by deflating the spring and removing the line by pulling
the collar against the fitting and pulling firmly on the air line. Trim 1” off the end of
the air line. Be sure the cut is clean and square (see fig. 7). Reinsert the air line into
the push-to-connect fitting.
b. Check the threaded connection by tightening the swivel fitting another ½ turn. If it still
leaks, deflate the air spring, remove the fitting, and re-coat the threads with thread
sealant. Reinstall by hand tightening as much as possible, then use a wrench for an
additional two turns.
2. If there is a problem with the inflation valve, then:
a.
Check the valve core by tightening it with a valve core tool.
b. Check the air line connection by removing the air line from the barbed type fitting.
Option 1
Option 2
fig. 9
RideControl