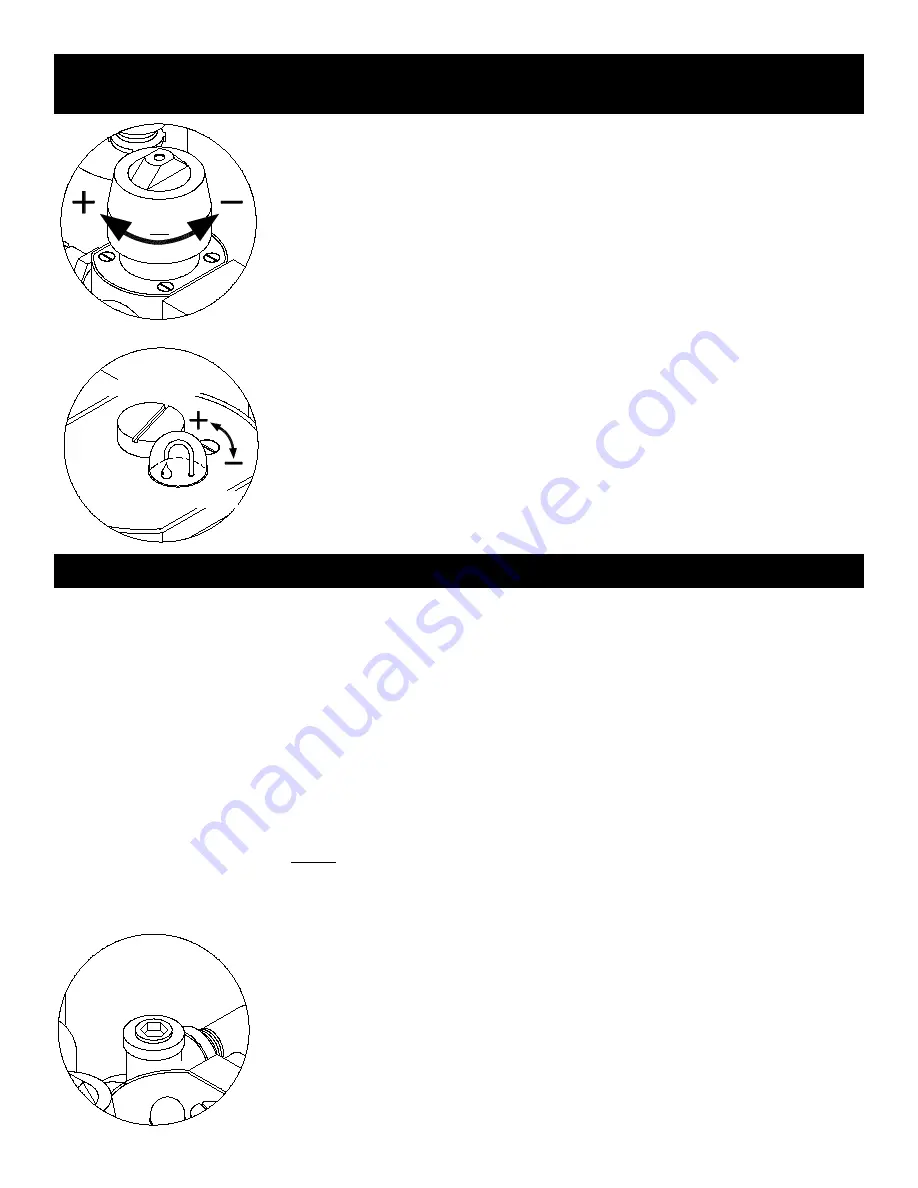
StEP 5)
Adjust pressure regulator clockwise to increase, counterclockwise to decrease motor
speed. This adjustment will increase or decrease the air flow.
Note: Available air pressure (psi) and volume (cfm) will determine blower
performance.
StEP 6)
The proper amount of oil mist has already been factory preset. However, depending on
the viscosity of the oil being used, slight adjustments may be necessary. With the blow-
er running, the proper oil mist should be one drop/min. The oil mist adjustment screw is
located next to the oil fill cap. Turn this screw clockwise to decrease or counterclockwise
to increase oil flow.
Note: Approximately 1 drop per minute can be achieved by turning the adjust-
ment screw fully clockwise, then counterclockwise 1 1/2 turns.
SIGHT GLASS
OIL FILL CAP
Keep blower motor dry and free from contaminants and dust.
Check periodically to ensure moving parts are free from obstructions.
Change filter (Part# WL040B) located in regulator after approximately 300–500 hours.
Factory recommended oil is SAE #10 non-detergent automotive engine oil or lighter. (Petroleum based only,
do not use synthetic oils)
Clean muffler assembly every 100–300 hours with safety solvent (Part #BAC–1001).
Flush air motor every 100 hours with safety solvent (#BAC–1001) through maintenance port (see below).
Remove air exhaust filter before flushing and reinstall after several minutes of running unit. Flush unit
after every 200 hours or after storing for long periods.
Air Motor FlUSHiNG ProCEDUrE
Use Air Systems’ Part #BAC-1001 safety solvent.
Do not use a flammable solvent or a solvent with a
toxicity rating of 500ppm or greater to flush the unit.
Note: Eye protection should be worn when flushing the unit.
StEP 1)
To flush the motor, turn blower off and remove exhaust filter element.
StEP 2)
Open the maintenance port. Spray 1-2 ounces of safety solvent into the maintenance port.
Close the maintenance port. Run the blower in an open area away from sparks and flames
for a minimum of five minutes before reinstalling the exhaust filter.
10
General Setup & operation
Model: SVB-A8
Maintenance