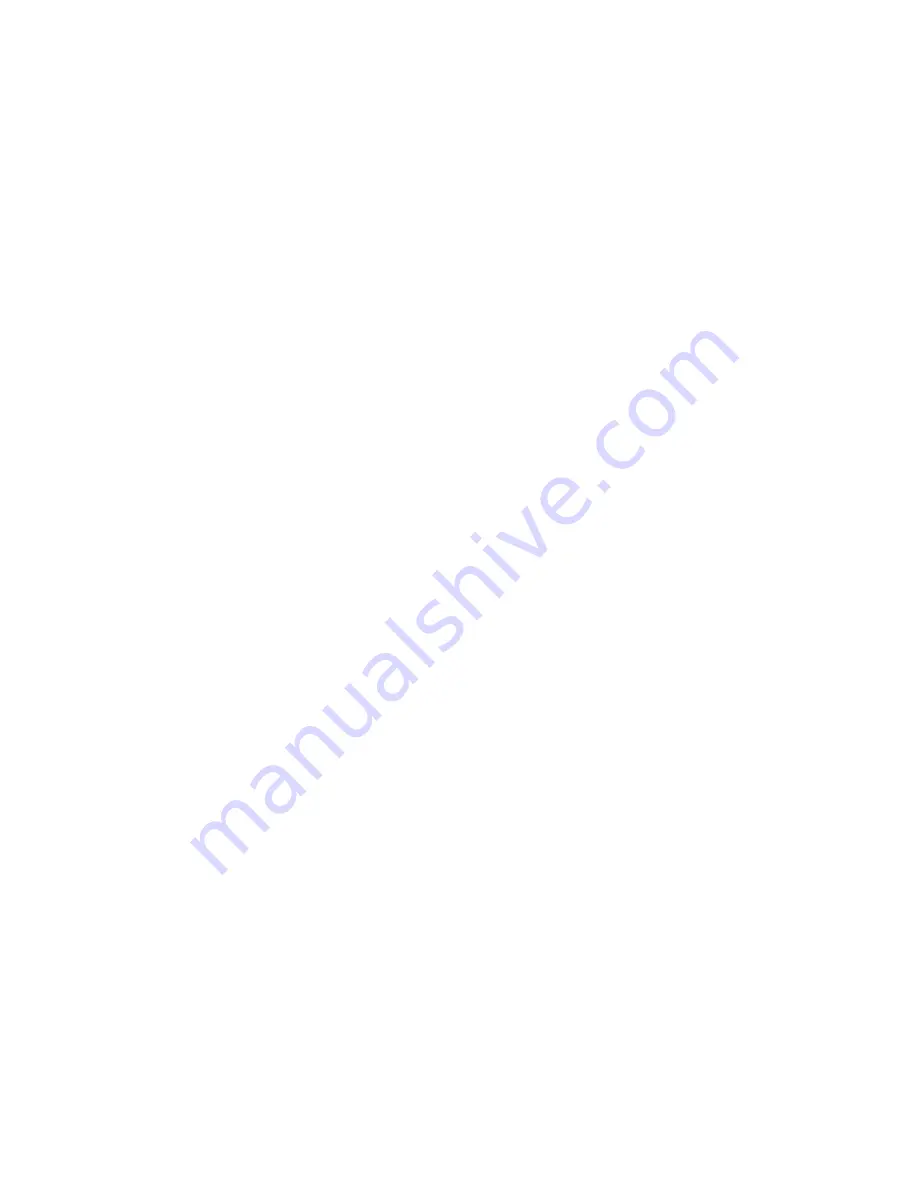
507148-01
Page 13 of 14
Issue 1406
Heat exchanger cleanout kit #ABRSH380-3 is available for
purchase.
Emergency Replacement Motor Operation
If the variable speed motor in this furnace needs to be
replaced in an emergency situation (such as “no heat”) and
an exact replacement motor is not immediately available,
a standard PSC motor of equivalent frame size, voltage,
rotation, and horsepower can be
temporarily
installed until
the correct replacement motor can be obtained.
Connect the desired speed taps to the HEAT and COOL
terminals and the neutral tap to the neutral terminal on the
control board (refer to the furnace wiring diagram).
Verify that the unit is operating at the desired speed and
within the rise range as shown on the unit rating plate.
The
correct replacement motor must be installed as soon
as possible to ensure continued satisfactory operation
of the furnace.
Emergency Fuel Pump Replacement
If replacement of the A2EA6520 fuel pump becomes
necessary, replace it with another Beckett CleanCut
fuel pump. In an emergency situation where the correct
replacement parts are not available, an A2VA7116 fuel
pump could be used. This option can produce a smoky
start-up and shutdown that could result in fouling of a heat
exchanger.
This is only a short-term option and should
be used only until the correct parts can be obtained
and installed.
Complete National Fuel Gas Codes are available from:
1. American Gas Association
1515 Wilson Boulevard
Arlington, VA 22209
2. National Fire Protection Association, Inc.
1 Battery March Park
Quincy, MA 02269
3. American National Standards Institute, Inc.
Publications Sales Department
11 West 42nd Street
New York, NY 10036
MAINTENANCE AND SERVICE
Oil Burner
It is recommended that the nozzle and oil filter be checked
before each heating season. Also recheck the conditions
shown on the
OIL FURNACE START-UP CHECKLIST
found on page 2.
Close the oil line shutoff valve if the burner is shut down
for an extended period of time.
Flue Pipe
Have the flue pipe inspected annually by a qualified service
technician. If any soot or ash has formed inside the flue
pipe, remove and clean. If the flue pipe has any holes or is
rusted out, replace with a new flue pipe of the same size.
Inspect the flue draft control device and replace if defective.
Blower
Blower motor is pre-lubricated and sealed for extended
operation. No further lubrication is required. The blower
assembly may be removed from the cabinet for cleaning
and servicing of the blower. Disconnect power to the unit
before servicing.
Heat Exchanger
To clean the heat exchanger:
1. Remove the vent pipe from the furnace.
2. Remove the locking screws and the caps from the two
cleanout tubes; remove the flue access elbow.
3. Using a long spiral wire brush, sweep down the outer
drum of the heat exchanger. Using a shop vacuum hose
attachment, vacuum out all loose debris.
4. Remove the locking screw and cap from the inspection
tube and with the spiral wire brush reach upward
toward the rear of the heat exchanger to clean out the
crossover tube; replace the locking screw and cap on
the inspection tube.
5. Do not attempt to clean the combustion chamber, as it
can be easily damaged.
6. Replace the three previously removed cleanout caps
and flue access elbow, making sure to re-install the
locking screws.
7. Brush out and vacuum the vent outlet area of the outer
drum and reattach the vent pipe.
8. Clean up around burner, blower deck, and vestibule area.