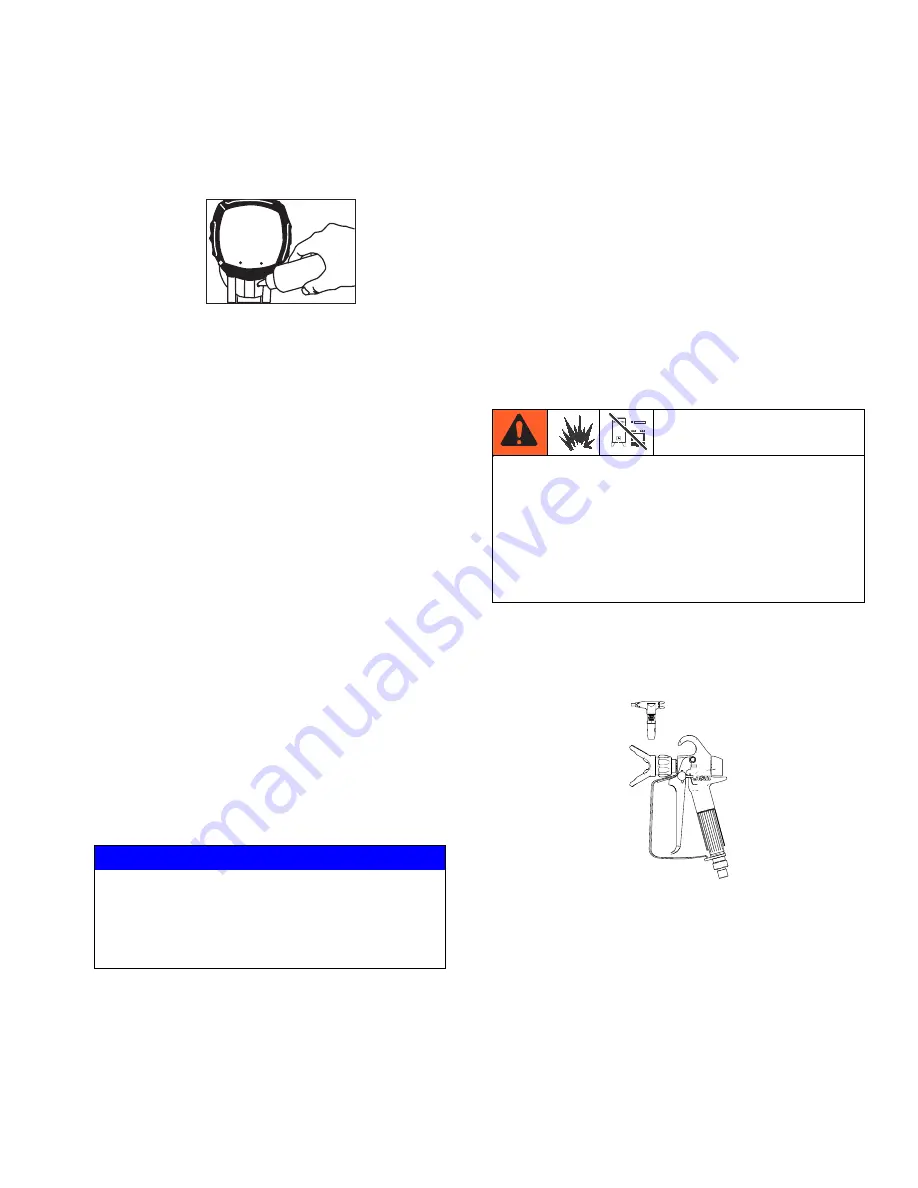
Operation
3A1186A
7
Fill the Packing Nut/Wet Cup
1.
Fill the Packing Nut/Wet Cup with 5 drops of Air-
lessco Throat Seal Oil (TSO).
Check the Engine Oil Level
1.
Unscrew the oil fill plug. The dipstick is attached to
the plug.
2.
Without threading the plug into place, check to be
sure the oil is up to the top mark of the dipstick.
3.
If oil is needed, refer to engine manual.
Fill the Fuel Tank
1.
Close the fuel shutoff valve.
2.
Use only clean, fresh, well-known brands of
unleaded regular grade gasoline.
3.
Remove the fuel cap and fill tank. Be sure the air
vent in the fill cap is not plugged so fuel can flow to
the carburetor, then replace the cap.
Flush the Sprayer
1.
Flush the sprayer. See
Flushing Procedure
on
page
7.
Prime and Flush Storage Fluid
Before beginning a new spraying project you need to
prime the sprayer and flush the storage fluid out of the
sprayer.
Oil- or Water-based Materials
•
When changing from water-based
material to oil
based material, flush with soapy water and then
mineral spirits.
•
When changing from oil based material to water
base material, flush with mineral spirits, followed by
soapy water, then a clean water flush.
•
When flushing with solvents, ground pail and gun.
•
Flush before changing colors, before fluid can dry in
the equipment, at the end of the day, before storing,
and before repairing equipment.
Flushing
1.
Make sure the gun trigger lock in engaged and there
is no spray tip in the gun. Refer to the separate
instruction manual provided with gun for safety fea-
tures and how to engage the trigger lock.
2.
Pour enough clean, compatible solvent into a large,
empty metal pail to fill the pump and hoses.
3.
Place the suction tube into the pail or place the pail
under the pump.
NOTICE
The equipment was tested with lightweight oil,
which is left in the fluid passages to protect parts.
To avoid contaminating your fluid with oil, flush the
equipment with a compatible solvent before using
the equipment for the first time.
ti16049a
• To reduce the risk of static sparking, which can
cause fire or explosion, always hold a metal part of
the gun firmly against the metal pail when flushing.
This also reduces splashing.
• Always remove the spray tip before flushing.
• Only metal pails, which are conductive, should be
used as solvent pails when flushing.
ti16028a
Summary of Contents for 3A1186A
Page 29: ...Notes 3A1186A 29 Notes ...