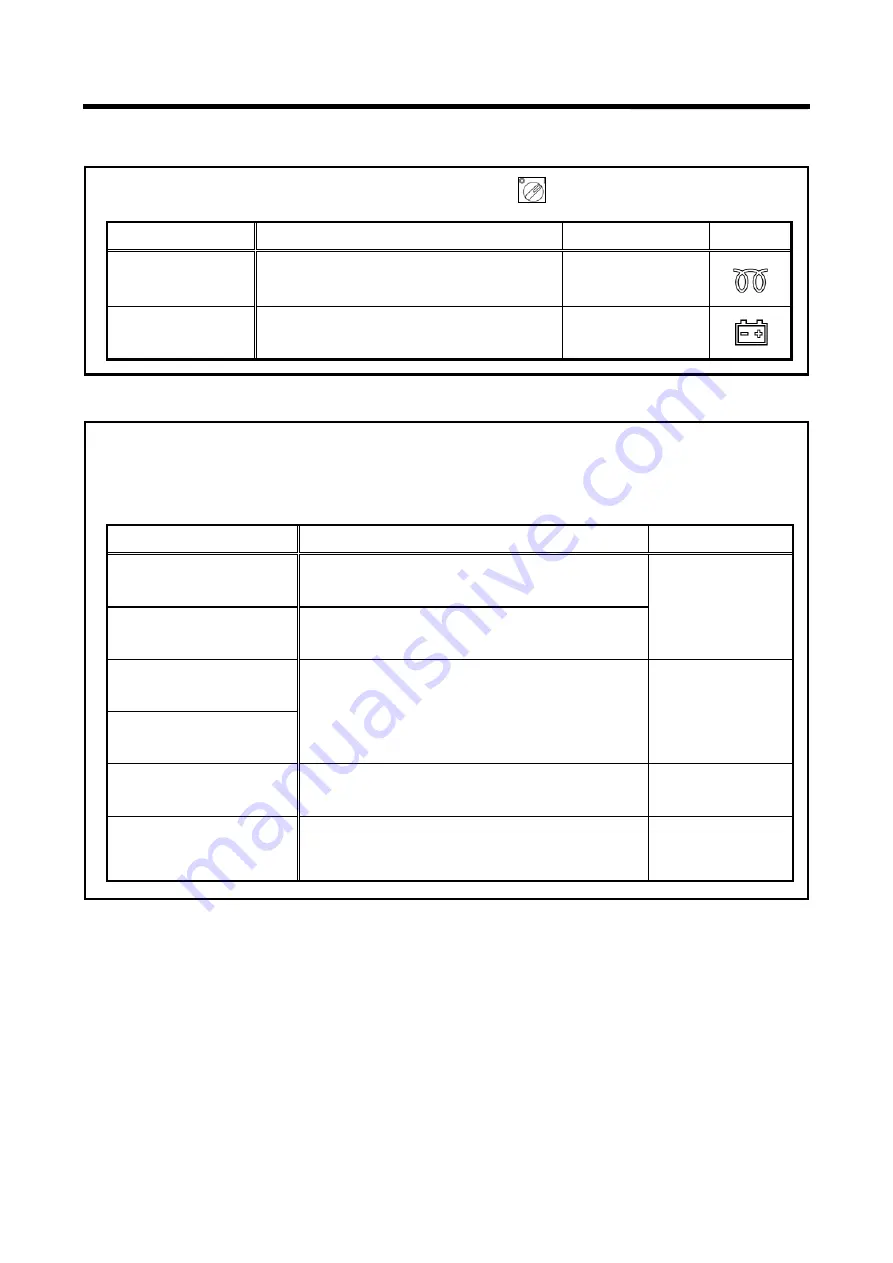
4
Failure cause and measures
4-2
4.1.2
Indicator lamp and Warning / Emergency display
[Indicator lamp]
Turn the CONTROL POWER switch to
position. Then the lamp goes on.
Item Contents
Measures
Monitor
Glow
When the unit is switched on, the preheat
indicator will be displayed briefly during
preheating.
―
Charge
The battery indicator will be displayed
when it is not being charged.
Check wiring.
Check alternator.
[Warning d isplay]
This displays such trouble of less importance when it occurs during
operation, but the unit continues operating.
When any abnormality happens, a trouble button flickers. In this time when trouble button is
pressed, a failure code will be displayed.
Display
Contents
Measures
DISCHARGE TEMP.H
Displayed when the air temperature at the
outlet of the air-end reaches
239°F (115
℃
)
.
See 4.2
“Troubleshooting”
ENGINE WATER
TEMP.H
Displayed when coolant temperature reaches
212°F (100
℃
)
.
COMP.AIR FILTER
CLOGGING
D
isplayed when air filter gets clogged and
suction resistance increases.
[Actuating resistance is more than
0.9PSI.
]
Clean/Change
ENGINE AIR FILTER
CLOGGING
ENGINE CHARGE
DEFECT
Belt loosened and/or cut
Faulty generation of alternator
Check/Change
SEPARATOR TEMP.H
Displayed when the air temperature at the
outlet of the separator reaches
239°F (115
℃
)
.
See 4.2
“Troubleshooting”
Go
to
Discount-Equipment.com
to
order
your
parts