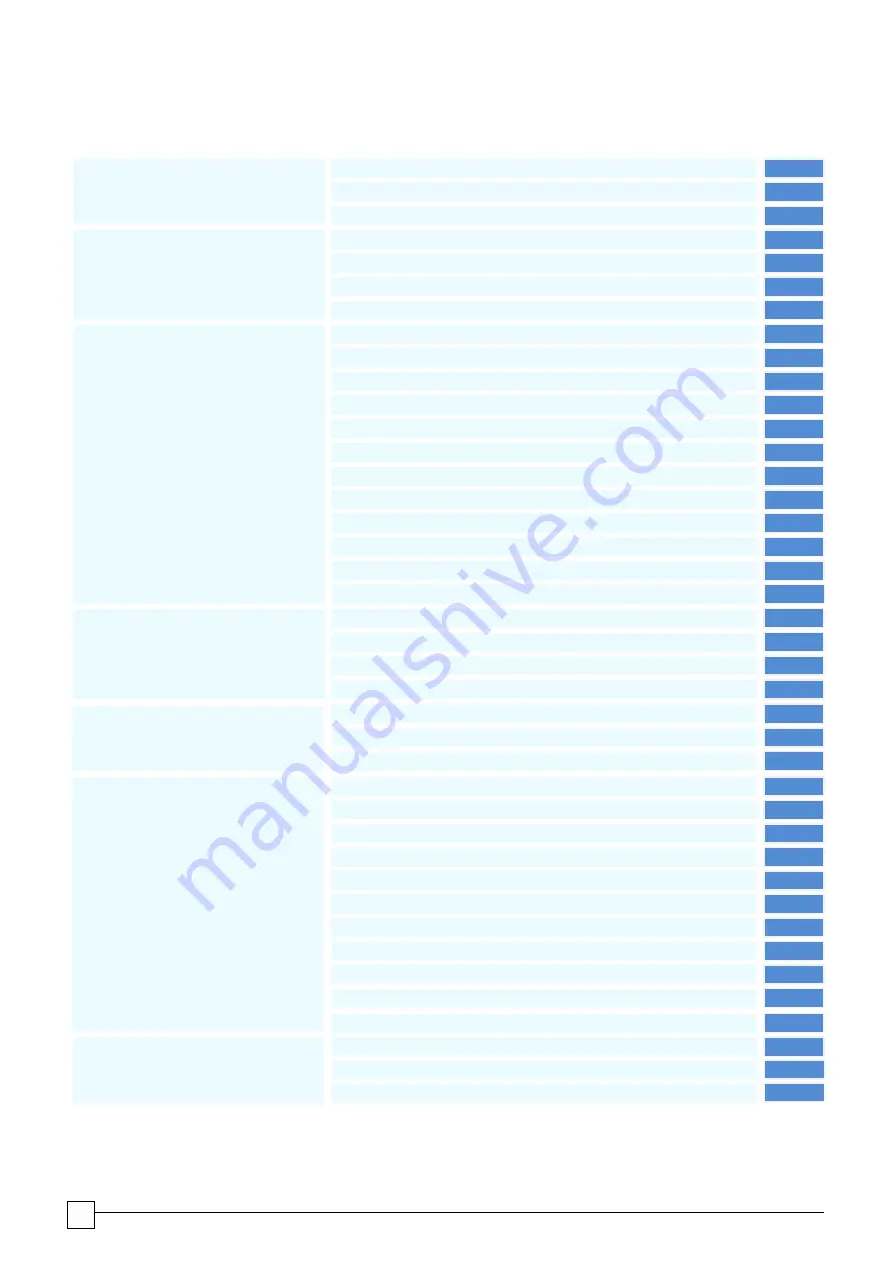
1
Installation, Operation & Maintenance Manual
fgfgffhfgfggbffgfV11:0212212121
CONTENTS
34
General
General
Unloading & Handling
General Installation
Fans
Speed Controlled Fans
Storage
4
4
5
Packaged Controls
Dampers
6
6
10
10
10
11
Locating Equipment
10
EC Fans
Thermal Wheels
Recuperators
Dampers
13
12
13
13
15
15
Maintenance of Units Containing Refrigerants
Routine Maintenance Schedule
Refrigeration Maintenance
15
WARRANTY
DELIVERY
& INSTALLATION
General
COMMISSIONING
& TESTING
MAINTENANCE
HEALTH
& SAFETY
General
Cautionary Notes
Water treatment
3
3
3
Heating & Cooling Coils
12
Invalidation of Warranty
3
8
Electrical Connections
8
Ductwork Connections
Procedure
2
2
Safety symbols
3
7
Assembly of Multiple Sections
8
Motor Wiring Diagrams
9
Pipework Connections
9
Water Coils, Steam Coils & DX Coils
10
Condensate Drains
Air Filters
14
Seasonal Shutdown
16
17
Fault Finding
DECOMMISSION
& DISPOSAL
Electric Air Heater Batteries
12
OPERATION
Fans
11
Inverters
11
End of Life Disassembly
Disassembly Guide
17
18