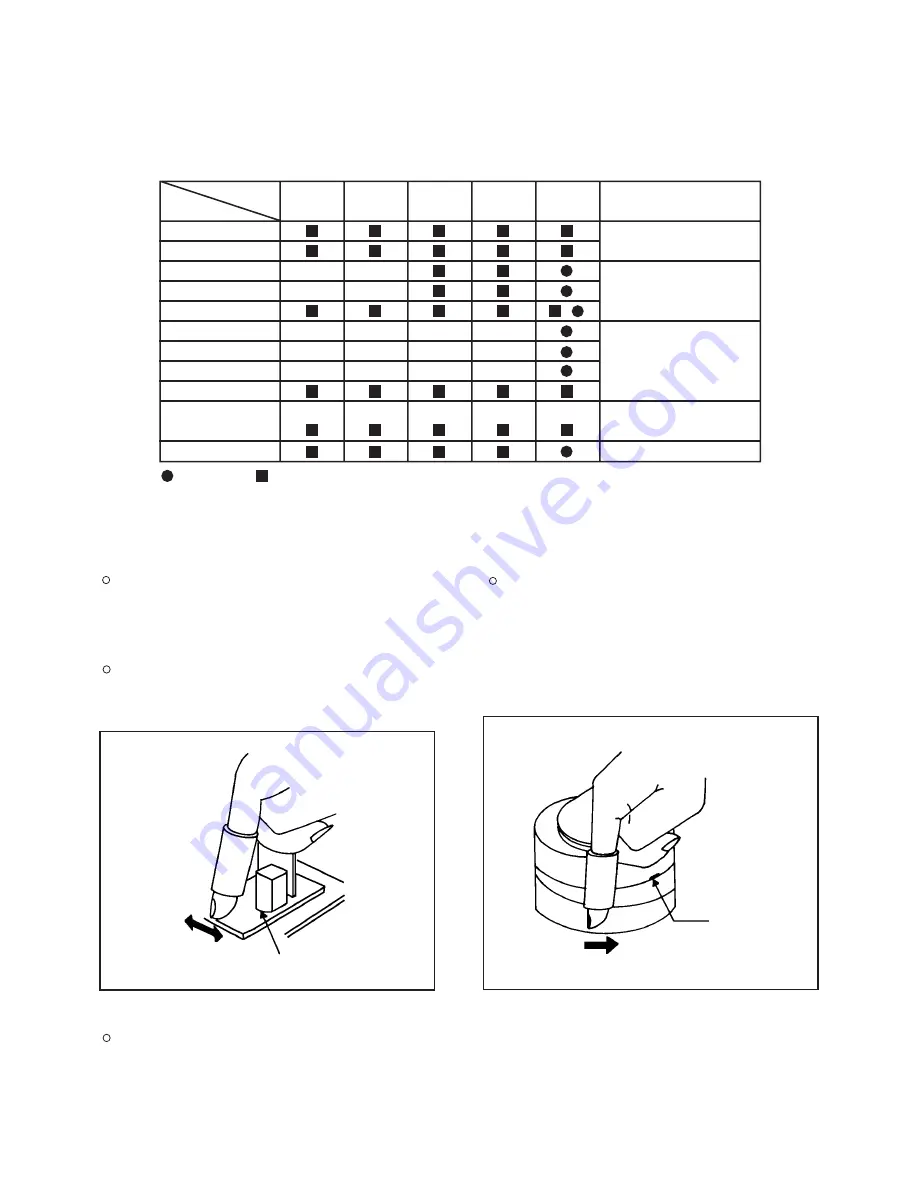
PREVENTIVE CHECKS AND SERVICE INTERVALS
The following standard table depends on environmental conditions and usage. Unless maintenance is properly
carried out, the following service intervals may be quite shortened as harmful effects may be had on other parts.
Also, long term storage or misuse may cause transformation and aging of rubber parts.
Notes
Time
Parts Name
CLEANING
NOTE
After cleaning the heads with isopropyl alcohol, do not
run a tape until the heads dry completely. If the heads
are not completely dry and alcohol gets on the tape,
damage may occur.
1. AUDIO CONTROL HEAD
Wrap a piece of chamois around your finger. Dip it in
isopropyl alcohol and clean the audio control head by
wiping it horizontally. Clean the full erase head in the
same manner. (Refer to the figure below)
2. TAPE RUNNING SYSTEM
When cleaning the tape transport system, use the gauze
moistened with isopropyl alcohol.
3. CYLINDER
Wrap a piece of chamois around your finger. Dip it in
isopropyl alcohol. Hold it to the cylinder head softly.
Turn the cylinder head counterclockwise to clean it (in
the direction of the arrow). (Refer to the figure below)
NOTE
Do not exert force against the cylinder head. Do not move
the chamois up or down since this can damage the head.
Always use a piece of chamois for cleaning.
Cylinder Head
Audio Control Head
Audio Control Head
Full Erase Head
Loading Motor Belt
Reel Belt
Pinch Roller
Capstan DD Unit
Loading Motor
Tension Band
Capstan Shaft
Tape Running
Guide Post
Cylinder Unit
Clean those parts in
contact with the tape.
Clean the rubber, and
parts which the rubber
touches.
Replace when rolling
becomes abnormal.
Clean the Head.
500
hours
1,000
hours
1,500
hours
2,000
hours
3,000
hours
: Replace
: Clean
C2-1