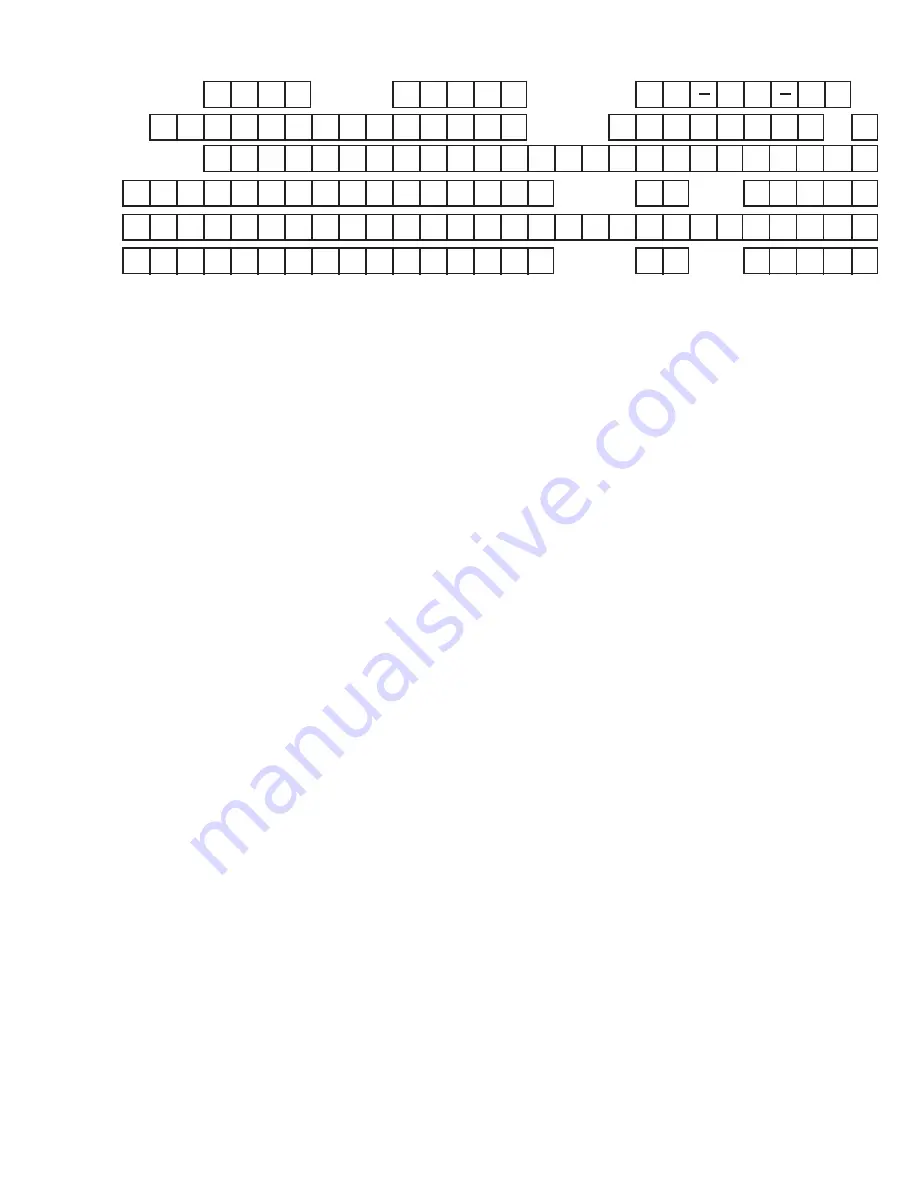
Purchaser's Signature _________________________ Date __________ Dealer's Signature ________________________ Date __________
PRE-DELIVERY SERVICE
CHECK AND ADJUST OR LUBRICATE AS REQUIRED
See Operator’s Manual for Details
Inspection Performed - Warranty and Safety Procedures Explained - Installation Complete
•
I have informed the Purchaser of this product of Warranty terms, provisions, and procedures that are applicable, reviewed the contents of the Operator’s Manual
including safety equipment, safe operation, and maintenance, reviewed the Safety Signs on implement (and tractor if possible), and Purchaser’s responsibility to
train his operators in safe operation.
•
IMPLEMENTS
: I have explained that Deflectors, Chain Guards, or Solid Skirts must be maintained in good repair and installed except in areas where persons,
vehicles, livestock, or other property will not be endangered by thrown objects and where such safety equipment would prevent the mower’s reasonable performance
of its assigned task.
•
DRIVELINES:
I have made certain that all driveline, gearbox, and other shields are in good repair and fastened securely in place to prevent injuries from
entanglement or thrown objects.
•
HYDRAULIC MACHINES:
I have explained the necessity of using clean hydraulic oil, changing filters as instructed, stopping leaks, damage caused by
operating with over-heated oil, caring for hoses, using hoses of proper rating, the necessity of maintaining the specified operating pressure, and the potential hazard
of oil's penetrating the skin.
•
BOOM-TYPE or FOLDING-TYPE IMPLEMENTS:
I have explained that it is not possible to guard against thrown objects when the head is lifted off ground
and that operator is responsible to watch out for persons in the area. I have explained that the lifted mower head or boom can contact overhead obstructions with
damage to cables and telephone lines and possible injury. I have explained that the extended head or boom or retracted boom can contact power lines with resulting
electrocution injury or death and that operator is responsible for keeping clear of such hazards.
Dealer’s Signature ___________________________________ Date ______________
I have been instructed on the paragraphs above, received and have been instructed in the contents of the Operator’s Manual including safety signs, safety
equipment, safe operation, maintenance, and the potential hazards of unauthorized alteration or modification of the product. I have been informed of the warranty
provisions and know that the warranty is not in effect until this form is received by Alamo Group.
I understand the Implement Guarding statements above and the potential hazards of operating without such guards. I understand that the operator is responsible for
the safety of others in the area. I have examined the product and accept it as being complete and in satisfactory condition with all required guards.
Purchaser’s Signature ___________________________________ Date ______________
Alamo Ind. Model
Serial No.
Purchase Date
M.I.
First Name
Purchaser
Last Name
Street & No., RFD,
Box, &/or Apt. No.
State or
Province
State or
Province
ZIP
ZIP
City
City
Dealer
MONTH
DAY
YEAR
ALAMO INDUSTRIAL
®
WARRANTY REGISTRATION INFORMATION
TEAR • TEAR • TEAR • TEAR • TEAR • TEAR • TEAR • TEAR • TEAR • TEAR • TEAR • TEAR • TEAR • TEAR • TEAR • TEAR • TEAR • TEAR •
TEAR • TEAR • TEAR • TEAR • TEAR • TEAR • TEAR
LUBRICATION & HYDRAULICS
Gearbox Speed Increaser (Oil Levels)
Hydraulic Oil Level (External. Tank)
Tractor Hydraulic Oil Level
Hydraulic Hoses (Not Kinked Tighten Connections)
Front Pump Drive (Assembly Is Tight And Shaft Properly Aligned)
MOWER
Spindle And Motor Bolts Properly Torqued
Spindle Oil Level
Blade Carrier Bolts Properly Torqued / Retaining Pin In Place
Mower Cutting Height And Level Adjusted
Belt Alignment And Tension Adjusted
Cutting Shaft Bearings Lubricated
All Hardware Properly Torqued
Tire And Air Pressure / Lug Nuts (Correct Torque)
Wheel Bearings (Check, Grease, And Preload)
ATTACHMENTS & INSTALLATION
Deflectors Front And Rear
Shredding Attachments
Correct Blade Rotation Direction
Axle Arms And Beams
Tongue And Control Rods (Installed And Adjusted)
All Bolts - Pins And Nuts (Proper Torque)
MOWER TO TRACTOR CONNECTION
Draw Bar Length (Check And Set)
A-Frame Pivot & Links
Control Rods (Adjusted Equal)
Axle Height (Adjusted)
Cutting Height (Adjust)
Mount Kit Pre-Operation Check Complete
Mower Wing (Adjust Level With The Center)
Mower Wing (Check For Proper Raising Operation)
C.V. Drivelines (Check Max Turn Radius)
Pull Type Hitch (Height Adjustment)
Mounting Hardware Properly Torqued
SAFETY ITEMS
Protective Shields (Operation And Installation)
Driveline Clutch (Torque Limiter) (Adjust And Run In)
Safety Decals (Installed)
Operator’s Manual (Supplied)
Tractor PTO Shield (Installed)
S.M.V. Emblem (Installed If Needed)
Neutral Safety & Cut - Off Switches
Safety Tow Chain (Installed)
1. PRINT FIRMLY. 2. REMOVE WHITE COPY FOR CUSTOMER RECORDS. 3. REMOVE YELLOW COPY FOR DEALERS RECORDS. 4. MAIL LAST CARD POSTAGE FREE.
CUSTOMER COPY
Summary of Contents for HYDRO 88
Page 2: ......
Page 4: ......
Page 10: ......
Page 11: ...Safety Section 1 1 HYDRO 88 96 04 02 2003 Alamo Group Inc SAFETY SECTION ...
Page 31: ...Introduction Section 2 1 HYDRO 88 96 03 94 2003 Alamo Group Inc INTRODUCTION SECTION ...
Page 35: ...Assembly Section 3 1 HYDRO 88 96 03 94 2003 Alamo Group Inc ASSEMBLY SECTION ...
Page 38: ......
Page 39: ...OPERATION SECTION Operation Section 4 1 2002 Alamo Group Inc ...
Page 72: ......
Page 73: ...Operation Section 4 1 HYDRO 88 96 03 94 2003 Alamo Group Inc MAINTENANCE SECTION ...
Page 88: ......
Page 89: ...HYDRO 88 96 03 94 2003 Alamo Group Inc PARTS SECTION ...
Page 92: ...GENERAL ASY HYDRO 88 96 08 04 2004 Alamo Group Inc Parts Section 4 ...
Page 96: ...SPEED INCREASER P N 02897900 OLD STYLE HYDRO 88 96 08 04 2004 Alamo Group Inc Parts Section 8 ...
Page 106: ...MOWER ASY 88 HYDRO 88 96 08 04 2004 Alamo Group Inc Parts Section 18 ...
Page 108: ...MOWER ASY 88 HYDRO 88 96 08 04 2004 Alamo Group Inc Parts Section 20 ...
Page 110: ...MOWER ASY 96 HYDRO 88 96 08 04 2004 Alamo Group Inc Parts Section 22 ...
Page 112: ...MOWER ASY 96 HYDRO 88 96 08 04 2004 Alamo Group Inc Parts Section 24 ...
Page 116: ...HYDRO 88 96 OMWPL 08 04 Printed U S A P N 803342 ...