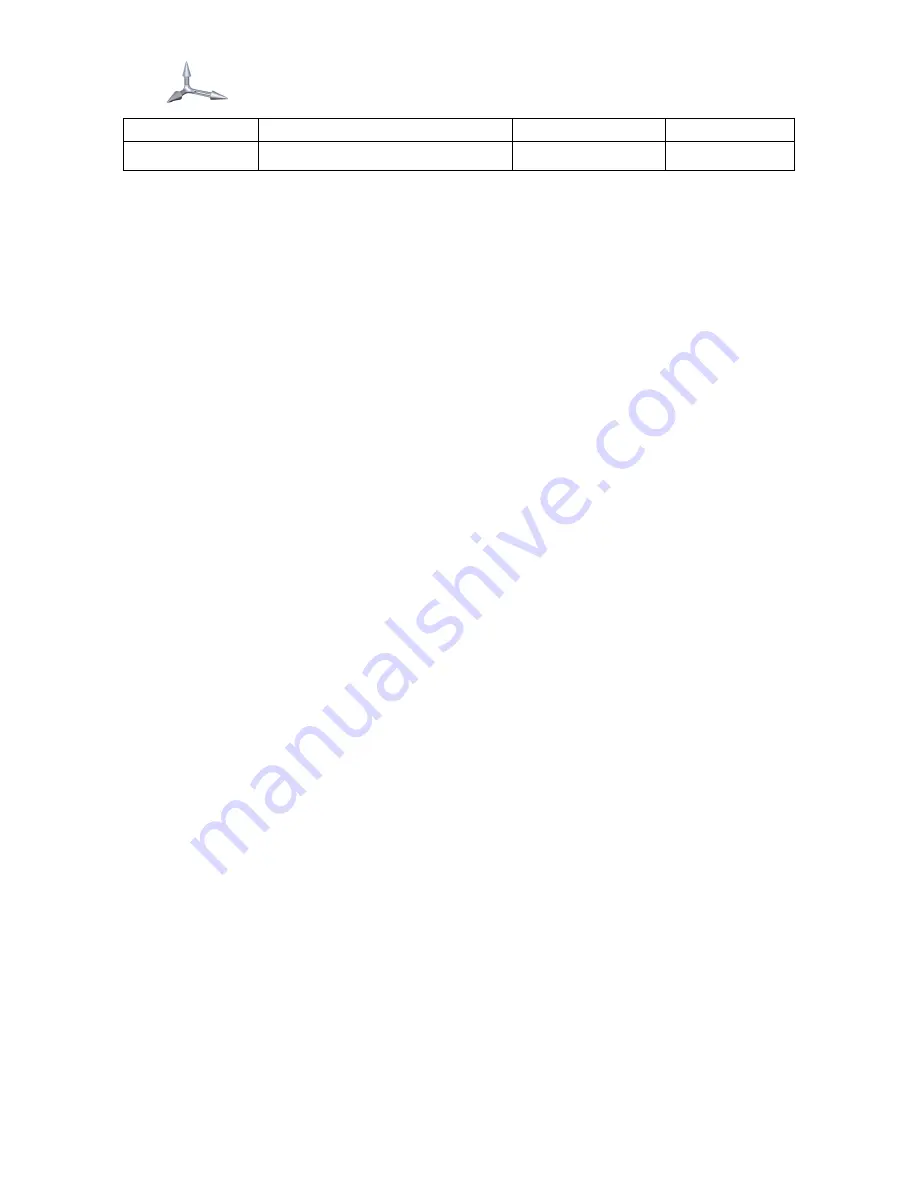
Technical Reference Manual for
OMNI-A0092
Author
C. Vale
Creation Date
2010-04-29
Product
OMNI-A0092
Revision Date
Name:OMNI-A0092_TRM.doc
Company Confidential
Version 1.0
Page 1 of 55
Table of Contents
1
Introduction ......................................................................................................................... 3
2
Installation Instructions ....................................................................................................... 4
3
Operation Instructions ....................................................................................................... 20
4
Suggested storage and handling ........................................................................................ 32
5
Maintenance ...................................................................................................................... 33
6
Specifications .................................................................................................................... 35
7
Appendix A: Clark Mast Maintenance Manual ................................................................ 40
8
Appendix B: Compressor Instruction Manual .................................................................. 50
Table of Figures
Figure 1: The antenna ................................................................................................................. 3
Figure 2: OMNI-A0092 Antenna system block diagram ........................................................... 5
Figure 3: Items to be bolted to mounting surface (e.g. container) ............................................. 6
Figure 4: Detail of mechanical interface for bolting down the main antenna assembly ............ 7
Figure 5: Top view of main antenna assembly .......................................................................... 9
Figure 6: Winch installation drawing ....................................................................................... 11
Figure 7: Anchor fitting ............................................................................................................ 13
Figure 8: Compressor ............................................................................................................... 14
Figure 9: Power connector ....................................................................................................... 14
Figure 10: Power connector with cable attached (not provided) ............................................. 15
Figure 11: Remote control with cable ...................................................................................... 15
Figure 12: Schematic of the RF load unit ................................................................................ 17
Figure 13: Loosening the mast securing clamp ........................................................................ 22
Figure 14: The antenna just before hoisting out of the enclosure ............................................ 23
Figure 15: The mast in the vertical position ............................................................................. 25
Figure 16: The antenna when fully deployed ........................................................................... 27
Figure 17: Measured VSWR .................................................................................................... 35
Figure 18: Antenna efficiency .................................................................................................. 36