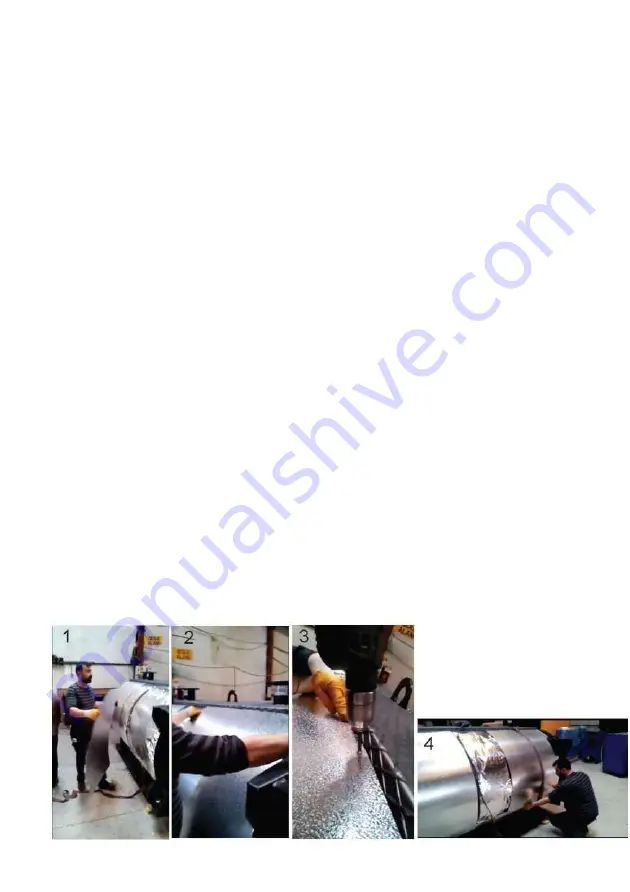
20
• After the installation of the heating system, all system equipment connections
(water, fuel, flue gas lines, electricity) must be checked for leakage.
• CGS2 and CGS3 boilers have a condensate outlet. This outlet must be
connected to a suitable conduit via a siphon to prevent liquid gas leakage.»
Condensate discharge must comply with applicable regulations.
• The weight of the flue gas ducts must not get carried by the boiler's flue gas
connection point and a flanged or leak-tight connection must be used for easy
maintenance.
• The total weight of the large and heavy burners should not get carried by the
boiler front cover, and the weight of the burner should get carried by the
ground with the help of a suitable adjustable support.
• The length of the burner connection bolts should not exceed the total thickness
of the burner flange, gasket and adapter plate.
• If the gap between the burner barrel and the boiler refractory is more than 10
mm, this area must be filled tightly with 1200 °C resistant ceramic fiber
material.
• The responsibility for the installation and commissioning of the control and
safety system of the heating system in compliance with the applicable
standards and regulations is in the units that implement the system project,
installation and operation. The minimum information is given as a preliminary
reference in accordance with the standards in force at the date of the
preparation of the installation part of this manual.
• For the types with 800.000 kcal/hr and under, they have a prismatic cabinet for
closing the thermal insulation. Cabin steel plates are delivered separately and
our authorized service department assembles them.
•
For the types with 1.000.000 kcal/hr and above, insulation closure sheet
plates are rolled and packed and put in the combustion chamber.
Our
authorized service assembles them as shown in the following pictures
1-2-3-4.