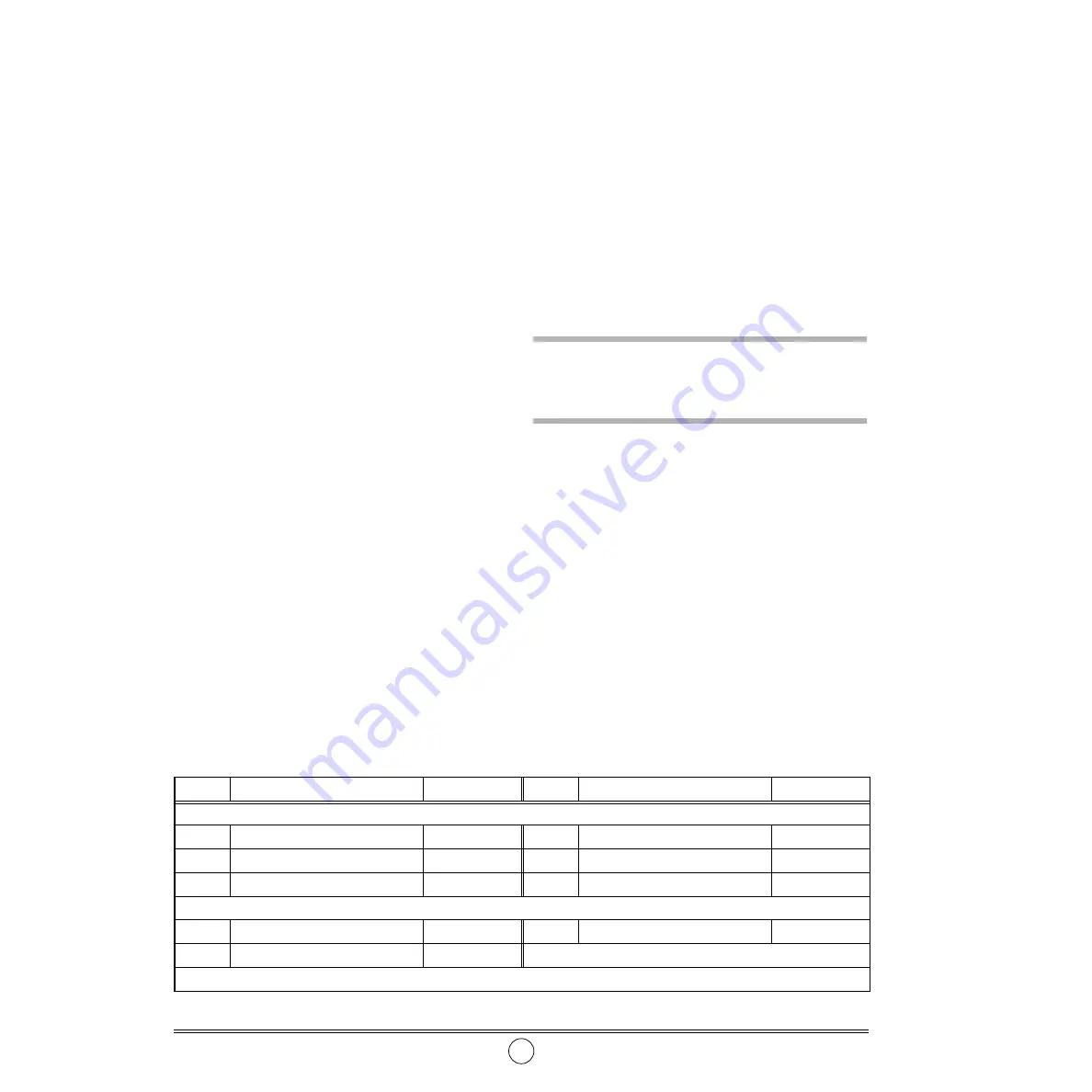
SER 9616-A
Low-Pressure Transfer Pump
Revision (10-98)
6
Alemite Corporation
3. Install O-Rings (
10
) onto both ends of the Outlet
Body.
4. Install Retaining Ring (
19
) onto Rod (
18
).
IMPORTANT: Make sure the ground side of
Plate (
22
) contacts Fluid Piston (
20
).
5. Install Fluid Piston (
20
) [segmented side first], Gasket
(
21
), and Plate (
22
) [ground side first] onto the bottom
of the Rod.
6. Install Nut (
5
) that secures the Plate to the Rod.
• Tighten the Nut securely.
• Place an appropriate size punch or other suitable tool
into the hole of the Rod.
CAUTION
Install the Rod assembly into the Body with a
twisting motion. Use care not to damage the Seals.
7. Install the Rod assembly into the bottom of the Outlet
Body.
• Position the Fluid Piston flush with the bottom of the
Body.
8. Install Washer (
9
), O-Ring (
8
), and Air Piston (
6
)
(observe THIS SIDE UP] onto the Rod.
9. Install Nut (
5
) that secures the Air Piston to the Rod.
• Tighten the Nut securely.
• Place an appropriate size punch or other suitable tool
into the hole of the Rod.
10. Install O-Ring (
7
) onto the Air Piston.
11. Screw Stop (
23
) into Cylinder (
26
) until it seats.
12. Install Pin (
24
) into the Stop.
• Make sure the Pin does not protrude from either side
of the Stop.
Clean and Inspect
1. Clean all metal parts in cleaning solvent. The solvent
should be environmentally safe.
2. Inspect all parts for wear and/or damage.
• Replace as necessary.
3. Inspect Air Piston (
6
) and Fluid Piston (
20
) for fatigue
cracks.
• Replace as necessary.
4. Inspect Rod (
18
) closely. Use a magnifying glass to
detect any score marks on the Rod.
• Replace as necessary.
5. Closely inspect the mating surfaces of all check valve
components for any imperfections. Ensure a smooth
and clean contact is obtained when assembled.
EXAMPLE
: Place Ball (
29
) into Seat (
31
).
Fill the Seat with solvent. Make sure no
leakage occurs.
Assembly
NOTE
: Prior to assembly, certain compo-
nents require lubrication. Refer to
Table 3
for details.
Pump Tube Assembly
NOTE
: Refer to
Figure 4
for a section view
of the pump tube assembly.
Outlet Body
1. Install and seat Seal (
13
) [stem end first], Lantern Ring
(
14
) [stepped end first], Seal (
15
) [stem end first], and
Washer (
16
) into Outlet Body (
11
).
2. Secure the components with Retaining Ring (
17
).
• Make sure the Retaining Ring seats properly in the
groove.
Item No.
Description
Notes
Item No.
Description
Notes
Clean Oil
10
O-Ring, 2-3/4 " ID x 3 " OD (Lower)
Pump Tube Portion
25
O-Ring, 1-7/16 " ID x 1-5/8 " OD
13
Seal, 1/2 " ID x 3/4 " OD
30
O-Ring, 1-1/4 " ID x 1-3/8 " OD
15
Seal, 1/2 " ID x 7/8 " OD
33
O-Ring, 1-15/16 " ID x 2-1/8 " OD
Magnalube-G Teflon Grease
7
O-Ring, 2-5/8 " ID x 3 " OD
10
O-Ring, 2-3/4 " ID x 3 " OD (Upper)
Air Motor Portion
8
O-Ring, 3/8 " ID x 1/2 " OD
Coat the Inside Diameter of the Air Motor Assembly
Table 3
Lubricated Components
1-800-548-1191-http://www.partdeal.com-info@partdeal.com