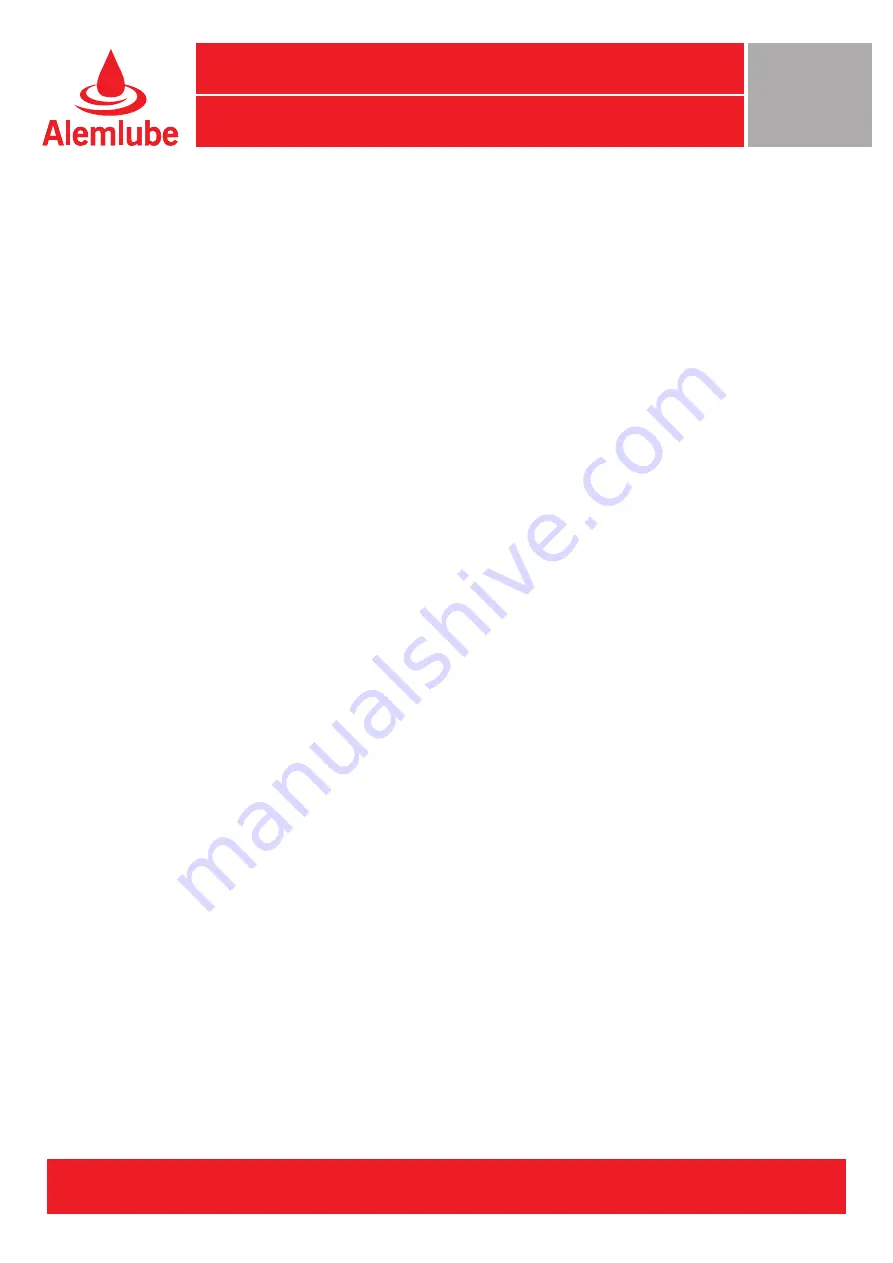
20KG Grease Kit
OWNER’S TECHNICAL MANUAL
G100120
Visit our website at
www.alemlube.com.au
or
www.alemlube.co.nz
NSW/ACT
TEL: (02) 9939 0711
FAX: (02) 9939 0411
QLD/PNG
TEL: (07) 3889 8480
FAX: (07) 3889 8490
VIC/TAS
TEL: (03) 8787 8288
FAX: (03) 8787 8266
WA
TEL: (08) 9209 3066
FAX: (08) 9209 3933
SA/NT
TEL: (08) 8241 7111
FAX: (08) 8241 7011
NZ
TEL: (09) 447 1007
FAX: (09) 447 1008
2
Safety Warning and Precautions
WARNING: The warnings, cautions, and instructions discussed in this instruction manual cannot cover all possible
conditions or situations that could occur. It must be understood by the operator that common sense
and caution are factors that cannot be built into this product, but must be supplied by the operator.
1. Keep the work area clean and dry. Damp or wet work areas can result in injury.
2. Keep children away from work area. Do not allow children to handle this product.
3. Use the right tool for the job. Do not attempt to force small equipment to do the work of larger industrial equipment.
There are certain applications for which this equipment was designed. It will do the job better and more safely
at the capacity for which it was intended. Do not modify this equipment, and do not use this equipment
for a purpose for which it Was not intended.
4. Check for damaged parts. Before using this product, carefully check that it will operate properly and perform its
intended function. Check for damaged parts and any other conditions that may affect the operation of this product.
Replace damaged or worn parts immediately.
5. Do not overreach. Keep proper footing and balance at all times to prevent tripping, falling, back injury, etc.
6. DO NOT use the equipment when tired or under the influence of drugs, alcohol, or medication.
A moment of inattention while operating this equipment may result in serious personal injury.
1. Read the following precautions and instructions before you begin assembly or using.
2. Failure to comply with these instructions could result in personal injury or property damage.
Keep these instructions in a convenient location for future reference.
Important Note:
The guarantee will be void if the pump has been altered in any way
Profile
Grease pumps are designed for transferring grease from a drum to where it would be used.
1. Compressed air operated reciprocating pumps are designed for high pressure greasing.
2. Be applicable to the manipulation of all types of grease (up to NLGI-2 consistency) from its original drums.
3. The pumps can be supplied as separate components or as a complete system with all the elements
– necessary for its installation.
4. The pumps can be assembled on mobile units as well as on fixed positions, connected to steel pipes.
5. This manual is applicable to the above pump only, please confirm your pump is included.