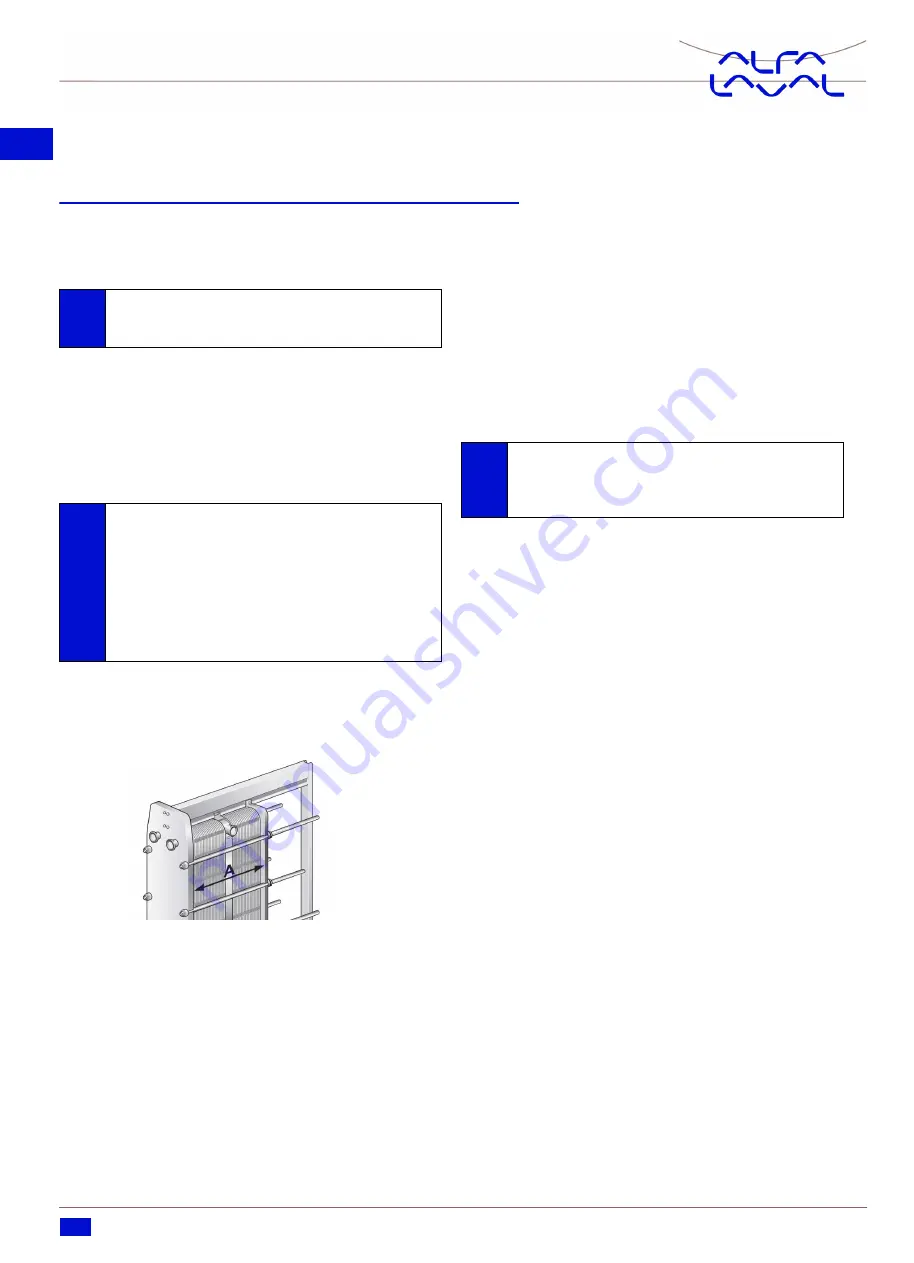
English
Operation
-14
Plate Heat Exchanger
3490008529 rev 2012-01
EN
EN
DE
FR
ES
PT
IT
SV
DA
FI
NL
RU
PL
NO
HU
SK
CS
SL
LV
LT
ET
EL
BG
RO
ZH
BG
Operation
Start-up
During start-up check that no visible leakages appear
from plate pack, valves or piping system.
Centrifugal pumps must be started against closed
valves and valves must be operated as smoothly as
possible.
Do not run pumps temporarily empty on the suction
side.
1
Before start-up check that all tightening
bolts are firmly tightened and that the
dimension A is correct, refer to PHE draw-
ing.
2
Check that the valve is closed between the
pump and the unit controlling the system
flow rate to avoid pressure surge.
3
If there is a vent valve installed at the exit,
make sure it is fully open.
4
Increase the flow rate slowly.
5
Open the air vent and start the pump.
6
Open the valve slowly.
7
When all air is expelled, close the air vent.
8
Repeat steps 1 – 7 for the second media.
Note!
If several pumps are included in the system, make sure
you know which one should be activated first.
Note!
Adjustments of flow rates should be made slowly in
order to avoid the risk of
pressure surge (water ham-
mer)
.
Water hammer is a short lasting pressure peak that can
appear during start-up or shut-down of a system, caus-
ing liquids to travel along a pipe as a wave at the speed
of sound. This can cause considerable damage to the
equipment.
Note!
Avoid rapid temperature changes in the PHE. With
media temperatures over 100 °C, slowly increase the
temperature preferably at least for one hour.