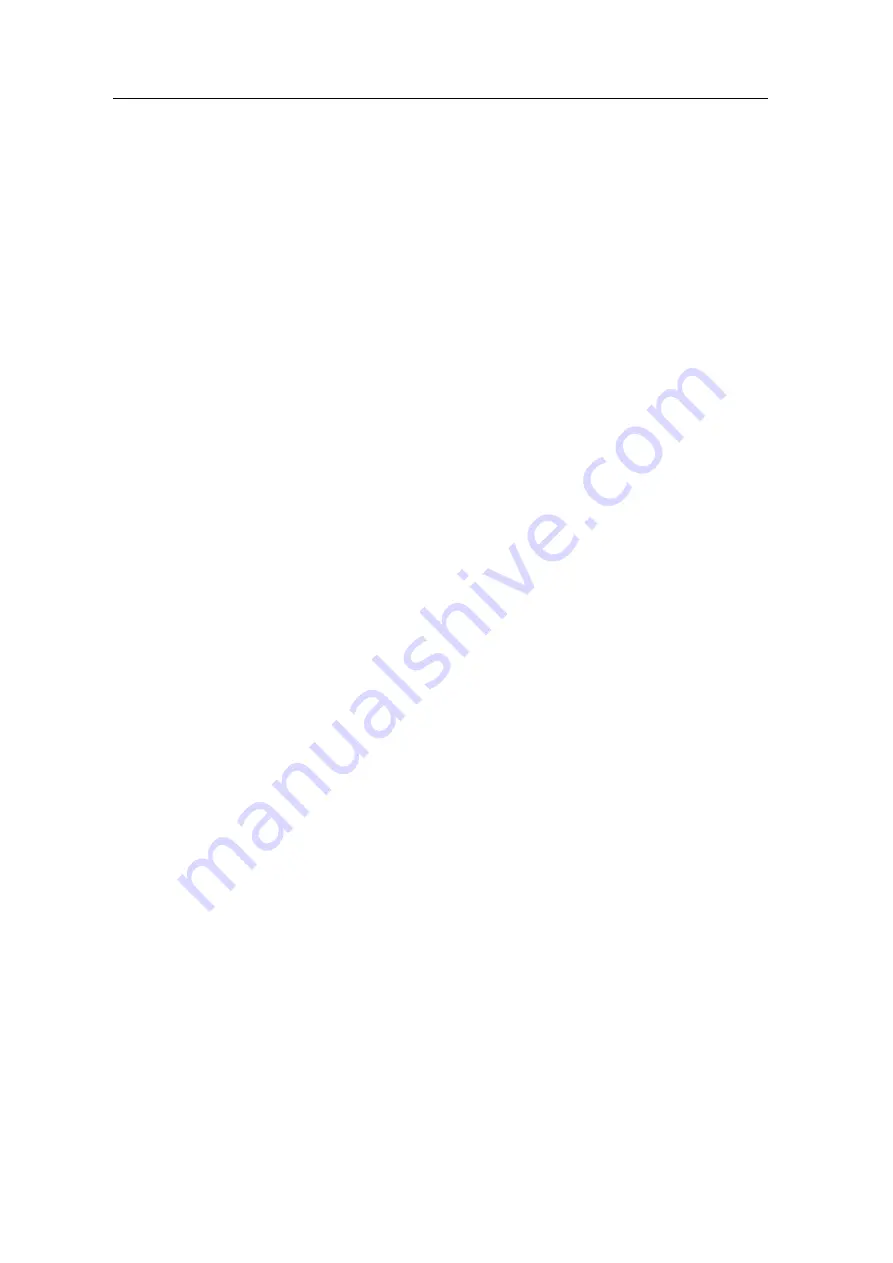
Claim
Procedure
Instruction Manual, Alfa Laval Toftejorg SaniMidget SB
Page 17
IM-TE91A720_EN2
Claim Procedure
In case of failure that needs assistance from Alfa Laval Tank Equipment A/S, it is essential for our
evaluation that the problem, as well as the working conditions of the machine, is described as detailed
as possible.
For description of the working conditions, fill in the form “Claim Report - Working Conditions”, which
you will find at the back of this manual.
How to contact Alfa Laval Tank Equipment A/S
For further information please feel free to contact:
Alfa Laval Tank Equipment A/S
Baldershoej 19
P.O. Box 1149
2635 Ishoej
Denmark
Phone no.: +45 43 55 86 00
Fax no.: +45 43 55 86 01
www.alfalaval.com
www.toftejorg.com
Contact details for all countries are continually updated on our websites.
Summary of Contents for Toftejorg SaniMidget SB Series
Page 2: ......
Page 8: ...Page 6 Instruction Manual Alfa Laval Toftejorg SaniMidget SB IM TE91A720_EN2 Blank page ...
Page 24: ...Page 22 Instruction Manual Alfa Laval Toftejorg SaniMidget SB IM TE91A720_EN2 ...
Page 25: ......
Page 26: ......
Page 27: ......