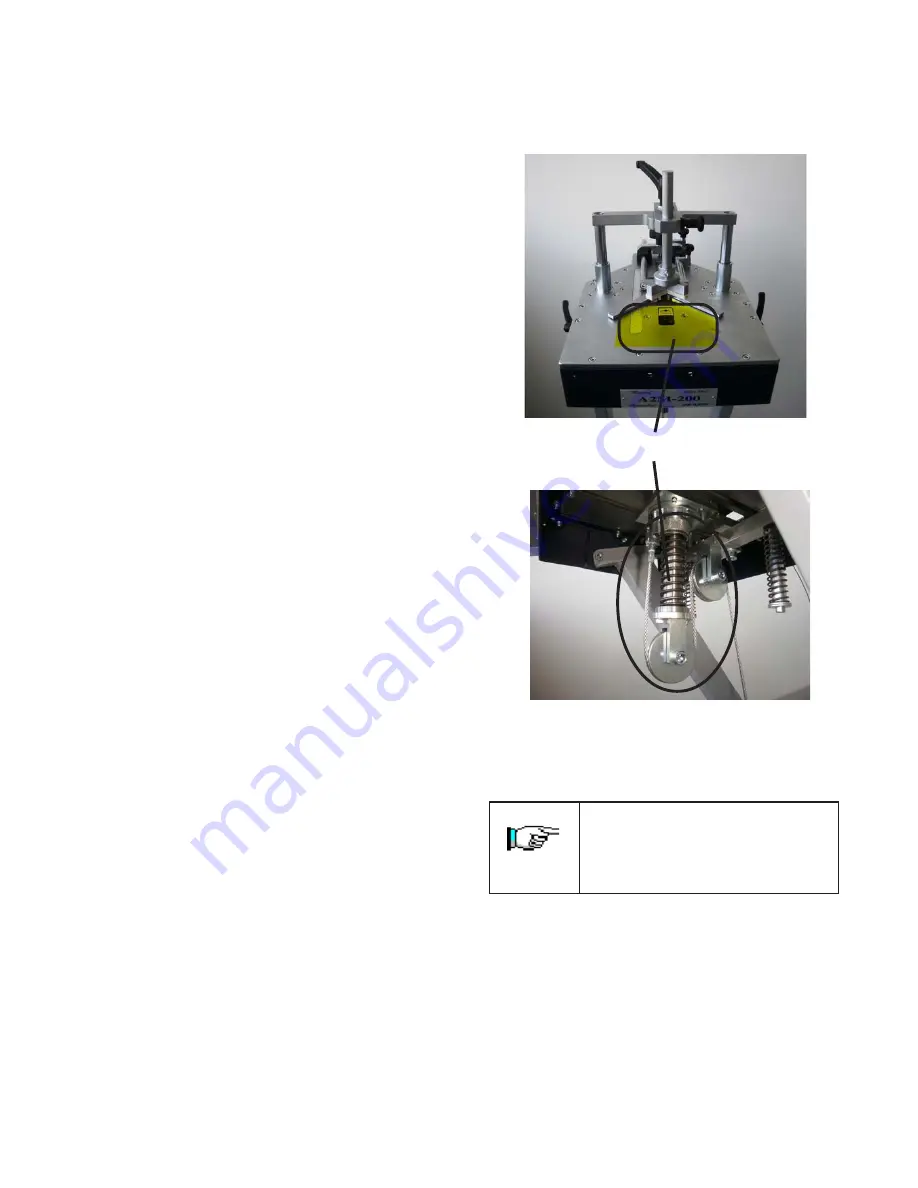
7
A2M 200
3.1
GENERAL WARNINGS
The operator must read paying the maximum attention to the
information written on this Handbook, expressively about
proper precautions for Safety listed in this chapter.
It is indispensable for the operator to follow the warnings
list here below:
•
Keep clean and ordered the machine and the working
premises
•
Provide appropriate containers to stock both just worked
pieces and ready to work ones.
•
Use the Machine only in normal psycho physical
condition
•
Wear an adequate clothing to avoid obstacles and/or
dangerous entangles to/from the machine
•
Wear the individual protection gears prescribed by
instructions handbook, regarding the effected operations
•
Do not remove or alter the warning plates and adhesive
signs
•
Keep the fingers away from the working area
•
Keep the foot separated from the pedal during Machine
regulation
3.2
SCHEDULED USE
The Machine is designed and constructed to execute
junctions of frames made in wood, plastic or MDF.
The machine is designed for manual use only.
3.4
DANGEROUS AREAS
The area of frames leaning is defined “working area”
The dangerous areas of machine, include the movable parts
and surrounding zones.
3 . 6 SAFE WORKING PROCEDURES
The other risks related with manual working way, are the
fingers crushing in the vertical clamp working area
It is necessary to follow carefully the following instructions:
1
Keep the fingers away from the vertical clamp working
area
2
Keep the foot away from the pedal during machine
regulation
3
Do not insert any fingres or things between the
mechanical parts of the wheels mechanism
3. SAFETY
The machine is projected and realized to
eliminate any risk connected with its use.
The utilizer is requested to achieve an
adequate training to be instructed by
Alfamacchine’s technicians.
3.3
INADVISABLE USE
The machine has not to be used:
•
For uses different from those listed in 3.2 paragraph
•
In explosive or aggressive atmosphere, at high density
of dust or oily substances suspended in the air
•
In flammable atmosphere
•
Outside in all weather severity
•
For working materials not suitable with machine
characteristics
Figure 3.4.A-Dangerous areas
3 . 5 RESIDUAL RISKS
During the normal working cycle and while maintenance,
the operators are exposed to several residual risks that,
because of operations own nature, can not be totally
eliminated.
-
Risk of finger crushing due to the presence of vertical
clamping
-
Risk of injury and finger crushing in the wheels and
springs mechanism
Dangerous areas