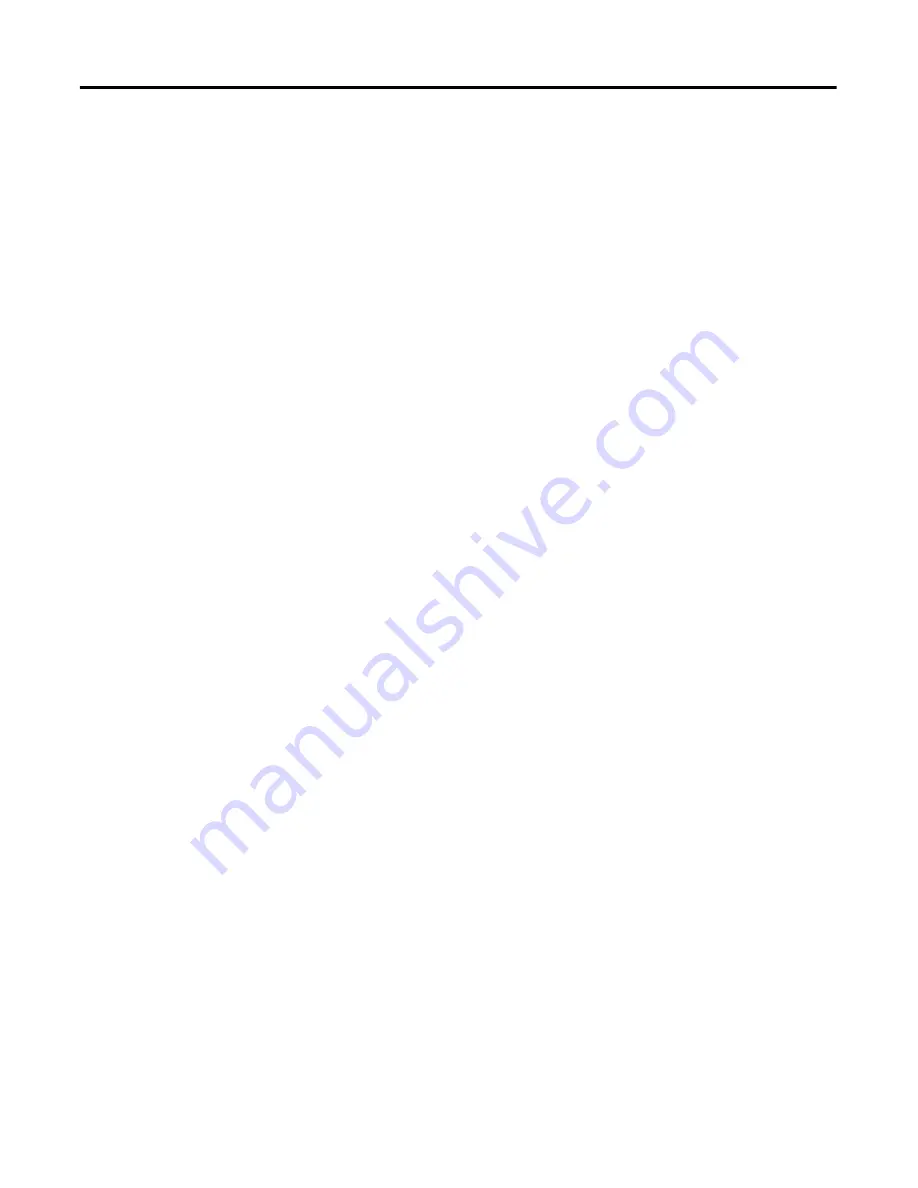
70
Rockwell Automation Publication 825-UM004D-EN-P - November 2012
Chapter 6
Configuring Protection & Logic Functions
Overload (Thermal Model)
The 825-P motor thermal element provides integrated protection for all of the
following motor operating conditions:
•
Locked rotor starts
•
Running overload
•
Imbalance current/negative-sequence current heating
•
Repeated or frequent starting
When overload protection is enabled, the relay configures a thermal curve based
on the motor Full Load Amps, Service Factor, Locked Rotor Amps, Hot Locked
Rotor Time, and Acceleration Factor settings. See Figure 32 for selected settings
of Thermal Overload curves.
The relay operates a thermal model with a trip value defined by the relay settings
and a present heat estimate that varies with time and changing motor current.
The relay expresses the present motor thermal estimate as % Thermal Capacity.
When the % Thermal Capacity reaches 100%, the relay trips.
If the thermal model is turned off (Overload Enable := N), the thermal model is
disabled, the output of the thermal model is blocked, and the relay reports the
% Thermal Capacity as 999 as noted in Chapter 7: Metering & Monitoring.
NOTE:
You can set the Run State Time Constant of the thermal overload curve. If the Run State Time
Constant is not known, set it to Auto; the relay configures the overload curve continuous
with the locked rotor curve.
Summary of Contents for 825-P
Page 1: ...Modular Protection System for Motors Catalog Number 825 P User Manual...
Page 4: ...4 Rockwell Automation Publication 825 UM004D EN P November...
Page 64: ...64 Rockwell Automation Publication825 UM004D EN P November 2012 Chapter 5 Using MPS Explorer...
Page 234: ...234 Rockwell Automation Publication 825 UM004D EN P April 2012 Chapter B ParameterList...
Page 265: ......