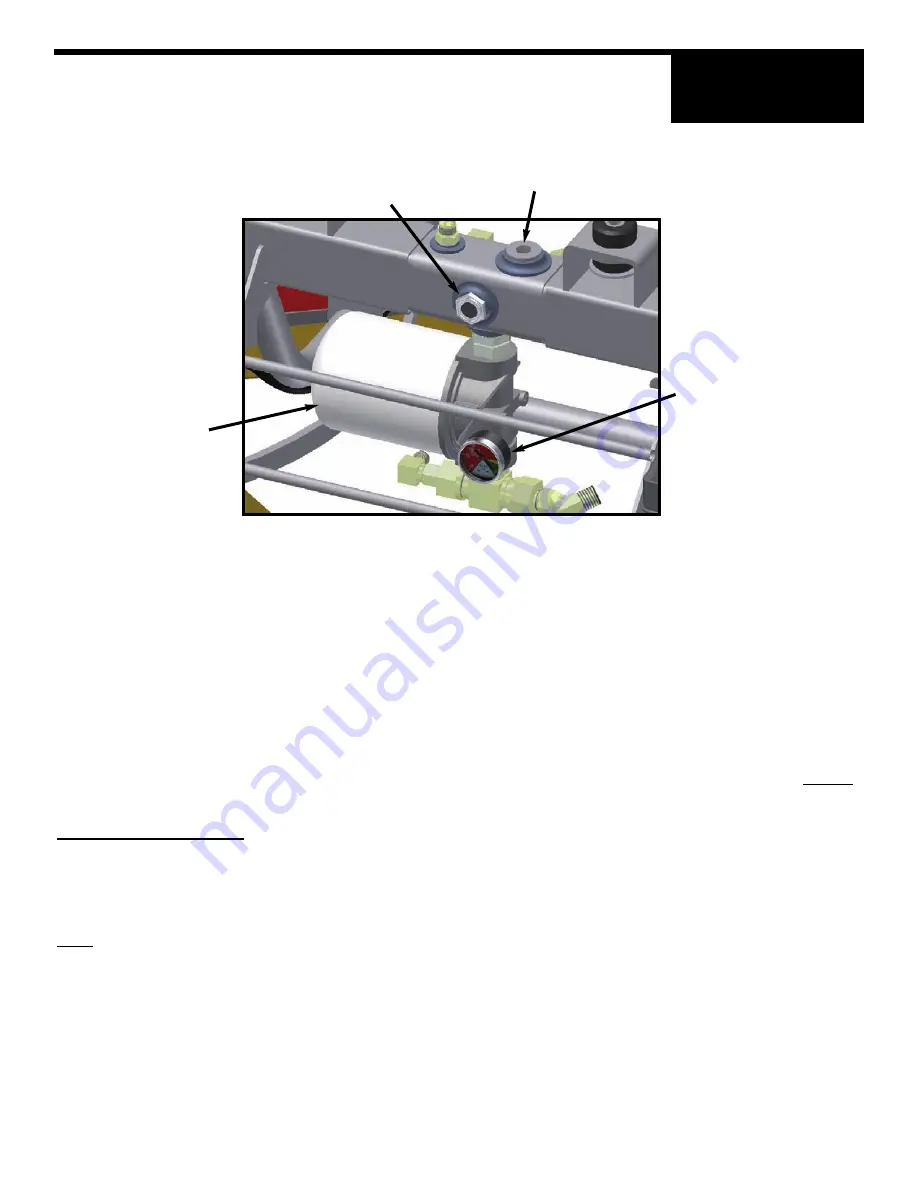
1A
OPERATIONS
1A-16
1. On a daily basis, check for leaks around all hydraulic fittings. Tighten if necessary.
2. On a daily basis, check hydraulic hoses for any wear that might occur during operations.
3. On a daily basis, visually inspect for scoring on cylinder rod ends.
3. On a daily basis, check the hydraulic fluid level on the sight gauge (A). If you can see that the oil is not all the way to
the top of the sight glass, then you will need add more hydraulic fluid using ISO 68 DTE26 hydraulic fluid . If tempera-
ture of hydraulic oil rises above 160 degrees, check to make sure the hydraulic oil is full. Also check to make sure that
no damage is done to the cooler or any other hydraulic components. If the problem still persist then contact Allen
Engineering Customer Service.
4. On a daily basis, check the gauge - 046242 (C) located on the hydraulic filter (B). If the needle on the gauge reach-
es 20 PSIG or is in the red, then the oil filter is dirty and needs to be replaced. Replace with Filter part number
048670
only.
NOTE: Failure to use Allen Engineering replacement filters will void all hydraulic warranties.
Steps for Replacing Filter:
> Remove and replace the filter - 048670 (B).
NOTE: It is a common practice when replacing oil filters to replace
the hydraulic oil as well.
> Tighten snug to ensure that the o-ring is properly seated.
Note:
If you do not experience any problems with the filter, it is a good practice to replace the filter every 100 hours of
operation. However, it is mandatory that the filter and hydraulic oil are replaced after the initial 50 hours of operation.
This is the “break-in” time for all the hydraulic components and new oil needs to be replaced at this time. The ISO
cleanliness specification must meet the following:
17-15-13
Put oil in the fill port (D).
5. On a yearly basis, grease joystick mechanisms. Also check for tears and cracks in the rubber boots.
A
1.19 Hydraulic Preventive Maintenance
C
B
D