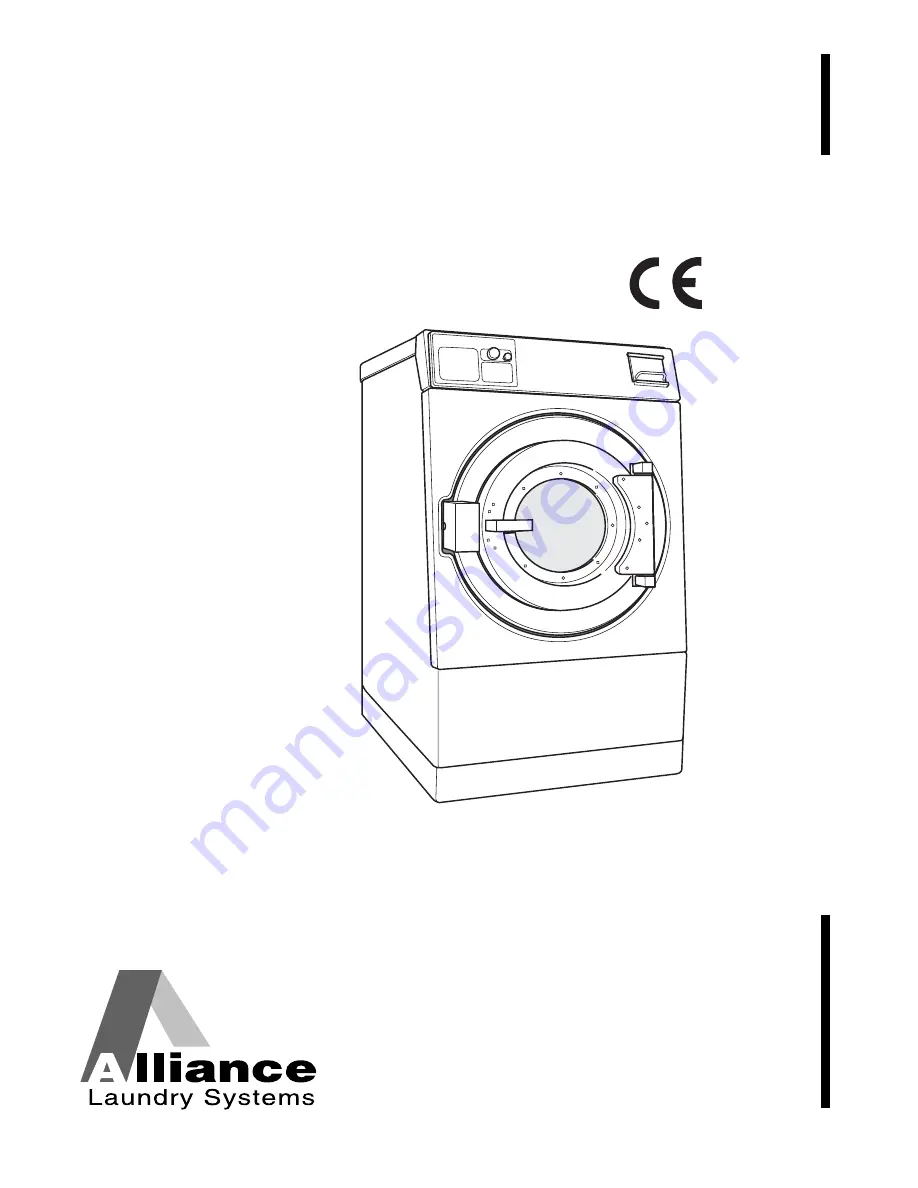
www.alliancelaundry.com
Installation/Operation/Maintenance
Washer-Extractors
Pocket Hardmount Variable-Speed
Refer to Page 6 for Model Identification
PHM1397C
PHM1397C
Part No. C003292ENR1
November 2013
Original Instructions
Keep These Instructions for Future Reference.
(If this machine changes ownership, this manual must accompany machine.)