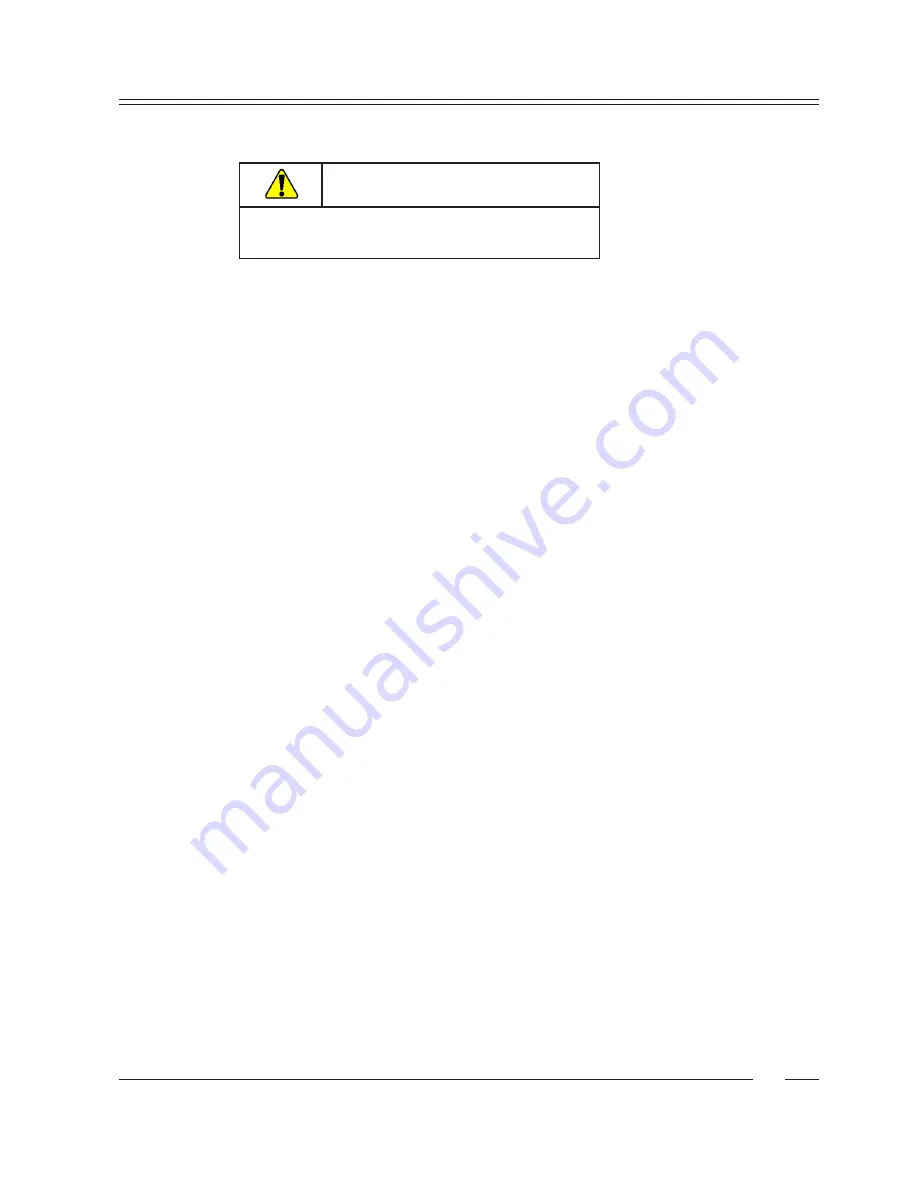
9
Important Safety Instructions
WARNING
To reduce the risk of fire, electric shock, serious injury or
death to persons when using your washer, follow these
basic precautions:
1. Read all instructions before using the washer.
2.
Refer to the GROUNDING INSTRUCTIONS in the installation Manual for the proper grounding of the
washer.
3. Do not wash textiles that have been previously cleaned, washed, soaked, or spotted with gasoline,
dry-cleaning solvents, or other flammable or explosive substances as they give off vapors that could
ignite or explode.
4.
Do not add gasoline, dry-cleaning solvents, or other flammable or explosive substances to the wash
water. These substances give off vapors that could ignite or explode.
5.
Under certain conditions, hydrogen gas may be produced in a hot water system that has not been
used for two weeks or more. HYDROGEN GAS IS EXPLOSIVE. If the hot water system has not been
used for such a period, before using a washing machine or combination washer-dryer, turn on all hot
water faucets and let the water flow from each for several minutes. This will release any accumulated
hydrogen gas. The gas is flammable, do not smoke or use an open flame during this time.
6. Do not allow children to play on or in the washer. This appliance is not intended for use by young
children or infirm persons without supervision. Young children should be supervised to ensure that
they do not play with the appliance.
7. Before the washer is removed from service or discarded, remove the door to the washing
compartment.
8. Do not reach into the washer if the wash drum is moving. This is an imminently hazardous situation
that, if not avoided, will cause severe personal injury or death.
9. Do not install or store the washer where it will be exposed to water and/or weather.
10. Do not tamper with the controls.
11.
Do not repair or replace any part of the washer, or attempt any servicing unless specifically
recommended in the user-maintenance instructions or in published user-repair instructions that the
user understands and has the skills to carry out.
12.
To reduce the risk of an electric shock or fire, DO NOT use an extension cord or an adapter to connect
the washer to an electrical power source.
13.
Use a washer only for its intended purpose, washing textiles.
14.
ALWAYS disconnect the washer from the electrical supply before attempting any service. Disconnect
the power cord by grasping the plug, not the cord.
15.
Install the washer according to the INSTALLATION INSTRUCTIONS. All connections for water, drain,
electrical power and grounding must comply with local codes and be made by licensed personnel
when required.
16.
To reduce the risk of fire, textiles which have traces of any flammable substances such as vegetable
oil, cooking oil, machine oil, flammable chemicals, thinner, etc., or anything containing wax or
chemicals such as in mops and cleaning cloths, must not be put into the washer. These flammable
substances may cause the fabric to catch on fire.
17. Do not use fabric softeners or products to eliminate static unless recommended by the manufacturer of
the fabric softener or product.
18. Keep washer in good condition. Bumping or dropping the washer can damage safety features. If this
occurs, have washer checked by a qualified service person.
19. Replace worn power cords and/or loose plugs.
20.
Be sure water connections have a shut-off valve and that fill hose connections are tight. CLOSE the
shut-off valves at the end of each wash day.
2