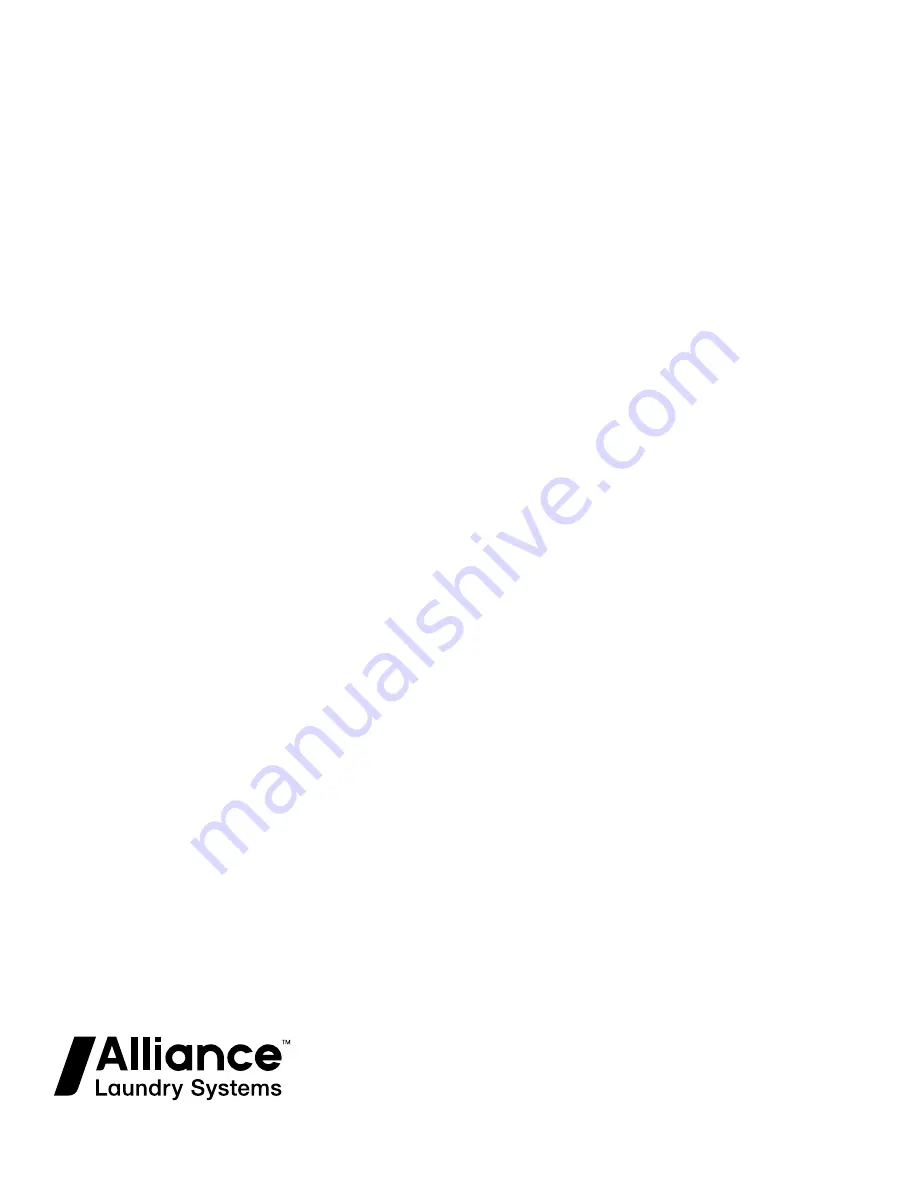
Installation/Operation/Maintenance
Washer-Extractors
Cabinet Freestanding
Refer to Page 9 for Model Identification
Original Instructions
Keep These Instructions for Future Reference.
CAUTION: Read the instructions before using the machine.
(If this machine changes ownership, this manual must accompany machine.)
www.alliancelaundry.com
Part No. D1598ENR10
February 2021
Summary of Contents for UY105 PRO
Page 2: ......