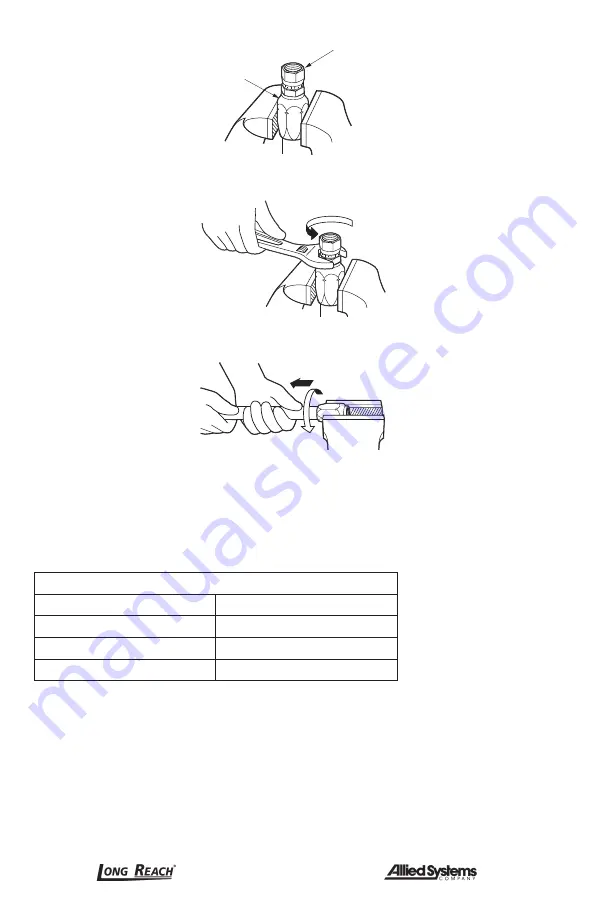
45-008 REV. 1/22
23
Fitting
Socket
Fitting
Insert
2. Unscrew the fitting insert from the fitting socket.
3. Unscrew the hose clockwise from the fitting socket.
4.6 Assemble Fitting
The hose inserts into the fitting socket to the depth shown in the following table, and
as indicated by the marks on the fitting wrench flats. Make sure the hose is not cut
too short for proper installation. Cut the hose to the desired length using a fine toothed
hacksaw or hose cutoff machine.
Hose Insertion Depth
Hose Size
Screw hose in to:
No. 4
1 in. (25 mm)
No. 6
1.15 in. (29 mm)
No. 8
1.18 in. (30 mm)
1. Lubricate the fitting insert and the inside diameter of the hose.
2. Measure from the end of the hose and mark the hose insertion depth using the
marks on the wrench flats or the table above.
3. Screw the hose into the fitting socket counterclockwise (CCW) to the hose insertion
depth mark.