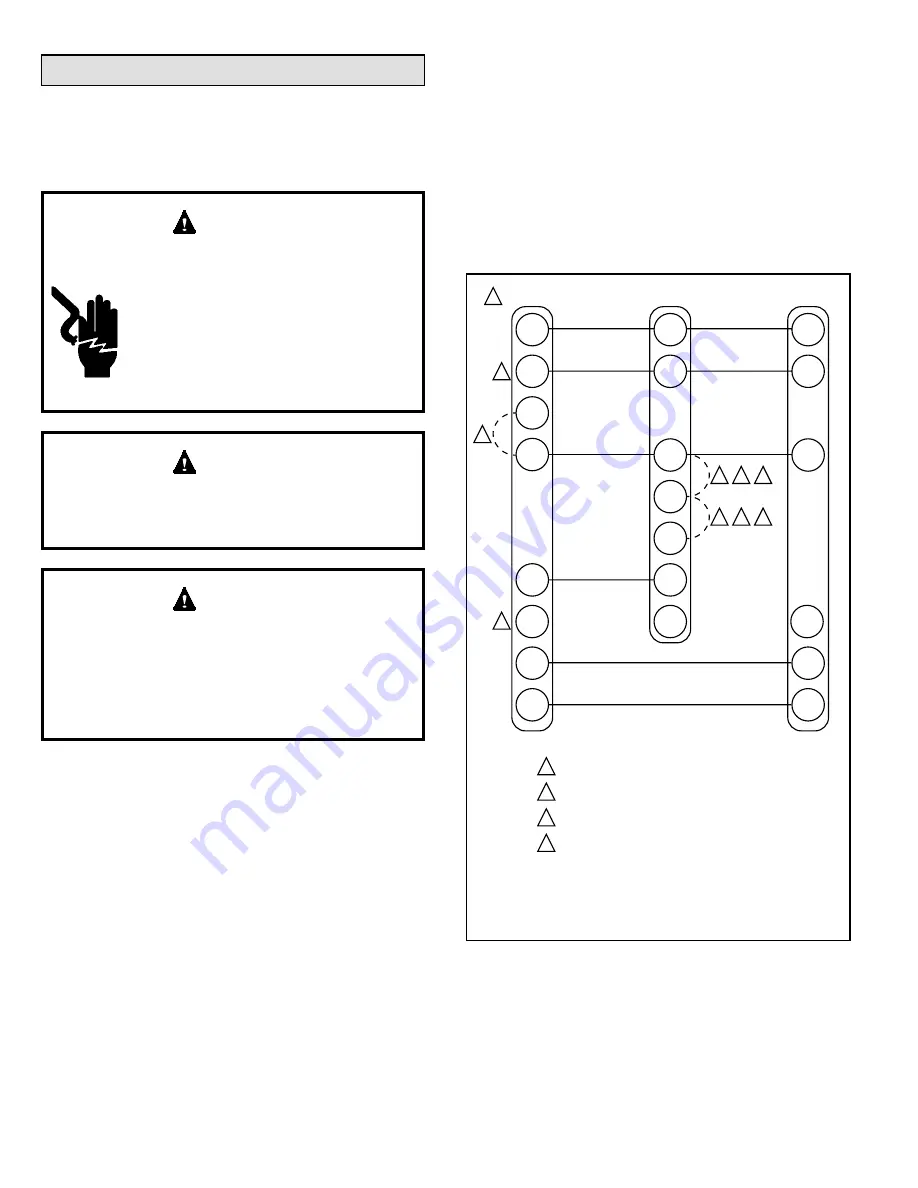
506762-03
Page 12 of 18
Issue 1946
Electrical Wiring
All field wiring must be done in accordance with the National
Electrical Code (NEC) recommendations, Canadian
Electrical Code (CEC) and CSA Standards, or local codes,
where applicable.
Electrical Shock Hazard!
Turn OFF electric power before connecting
unit, performing any maintenance or
removing panels or doors. More than one
disconnect may be required to turn off all
power.
FAILURE TO DO SO COULD RESULT IN
BODILY INJURY OR DEATH.
WARNING
Unit must be grounded in accordance with national and
local codes. Failure to ground unit properly can result in
personal injury or death.
WARNING
Line voltage is present at all components when unit is
not in operation on units with single pole contactors.
Disconnect all remote electric power supplies before
opening access panel. Unit may have multiple power
supplies. Failure to disconnect all power supplies could
result in personal injury or death.
WARNING
Refer to the furnace or blower coil Installation Instructions
for additional wiring application diagrams and refer to unit
rating plate for minimum circuit ampacity and maximum
overcurrent protection size.
1. Install line voltage power supply to unit from a properly
sized disconnect switch. Any excess high voltage field
wiring should be trimmed or secured away from the
low voltage field wiring.
2. Ground unit at unit disconnect switch or to an earth
ground. To facilitate conduit, a hole is in the bottom
of the control box. Connect conduit to the control box
using a proper conduit fitting. Units are approved for
use only with copper conductors. 24V Class II circuit
connections are made in the low voltage junction box.
A complete unit wiring diagram is located inside the
unit control box cover.
3. Install room thermostat according to thermostat
installation instruction and on an inside wall that is
not subject to drafts, direct sunshine, or other heat
sources.
4. Install low voltage wiring from outdoor to indoor unit
and from thermostat to indoor unit (see Figure 6).
5. Do not bundle any excess 24V control wire inside
control box. Run control wire through installed wire tie
and tighten wire tie to provide low voltage strain relief
and to maintain separation of field-installed low and
high voltage circuits.
1 Refer to thermostat installation instructions
2 If applicable
3 Refer to indoor unit installation instructions
4 “L” is used for any accessories (e.g. diagnostic /
warning / alarm), used to activate thermostat
warning light
W / W1 / W2 / W3 are auxiliary heat
(supplemental to heat pump).
“E” is emergency heat (disables heat pump).
NOTES:
W3
W2
R
R
R
C
C
C
W1
W/
W1
W1
Auxiliary Heat
(Heat Pump)
G
G
Indoor Blower Only
O
O
Heat Pump
Thermostat
Indoor Unit
Outdoor Unit
E
L
L
Y1
Compressor
Y1
4
1
3
1 2
3
1 2
1
1
L
Auxiliary Heat
(Heat Pump)
Figure 6. Thermostat Designations -
Non-Communicating