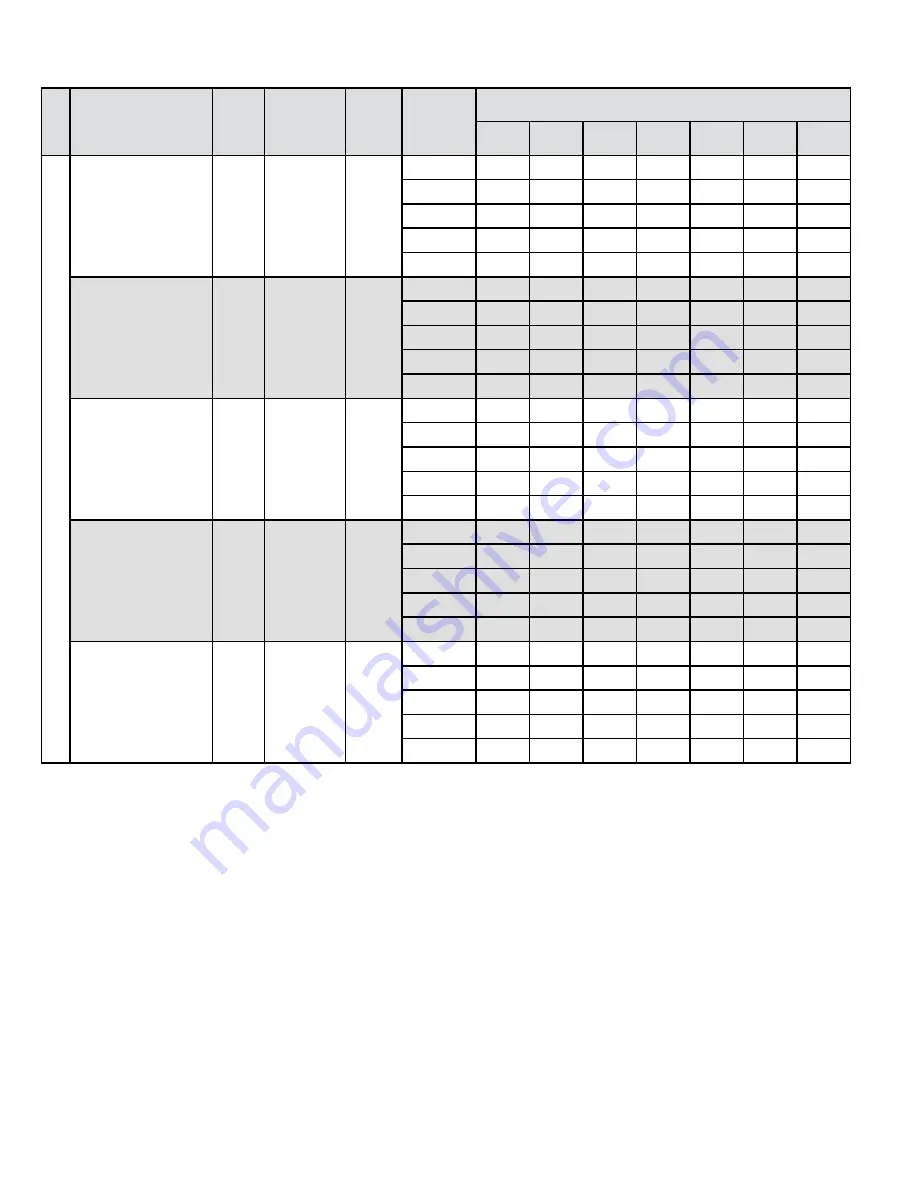
508142-01
Issue 2047
Page 6 of 33
BL
OWER PERFORMANCE DATA
Model
Motor
Size
(hp)
Blower
Size
Temp
Rise
(°F)
Blower
Speed
CFM @ External Static Pressure - " w.c.
0.20
0.30
0.40
0.50
0.60
0.70
0.80
Downflow
80G10DF045AE12
1/2
10 x 8
15 - 45
High
1375
1335
1320
1275
1245
1215
1175
Med/High
1145
1120
1075
1045
1000
970
925
Med
950
915
870
835
785
745
695
Med/Low
840
790
745
715
655
605
555
Low
725
665
625
565
520
455
400
80G1DF070AE12
1/2
10 x 10
30 - 60
High
1420
1400
1375
1340
1285
1210
1140
Med/High
1195
1180
1150
1120
1075
1065
1020
Med
1115
1070
1045
1010
985
955
920
Med/Low
1090
1055
1025
990
955
915
890
Low
920
900
845
820
770
730
675
80G1DF070BE12
1/2
10 x 10
30 - 60
High
1400
1360
1310
1280
1250
1220
1165
Med/High
1230
1205
1155
1110
1060
1000
935
Med
1125
1085
1050
985
935
865
795
Med/Low
1110
1055
1000
950
865
815
750
Low
900
845
790
705
645
590
480
80G1DF090CE16
3/4
10 x 10
30 - 60
High
1695
1660
1615
1570
1545
N/A
N/A
Med/High
1470
1425
1395
1360
1295
1265
1215
Med
1340
1290
1250
1210
1165
1120
1080
Med/Low
1280
1225
1185
1145
1085
1040
1000
Low
1105
1040
1005
945
865
810
755
80G1DF110CE20
1
11-1/2 x 10
30 - 60
High
2325
2280
2235
2165
2125
2090
2035
Med/High
2010
1940
1895
1845
1800
1755
1700
Med
1760
1705
1635
1595
1545
1510
1460
Med/Low
1570
1500
1440
1380
1320
1285
1255
Low
1375
1320
1265
1200
1170
1100
1030