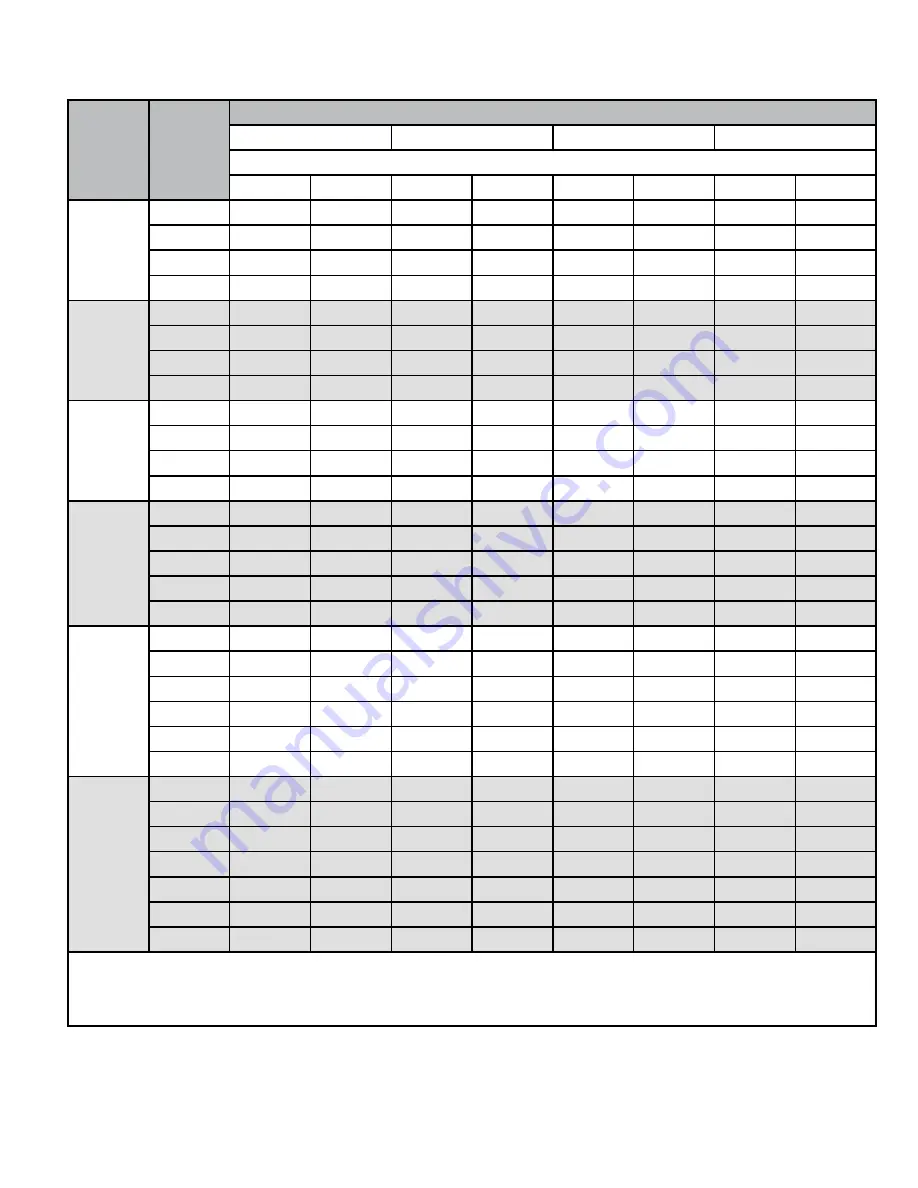
507335-02
Page 19 of 39
Issue 2001
Capacity of Type B Double Wall Vents with Single Wall Metal Connectors Serving a Single Category I Appliance
Table 4.
Height H
(feet)
Lateral L
(feet)
Vent and Connector Diameter - D (inches)
3 inch
4 inch
5 inch
6 inch
Appliance Input Rating in Thousands of Btu per Hour
MIN
MAX
MIN
MAX
MIN
MAX
MIN
MAX
6
0
38
77
59
151
85
249
126
373
2
39
51
60
96
85
156
123
231
4
NR
NR
74
92
102
152
146
225
6
NR
NR
83
89
114
147
163
220
8
0
37
83
58
164
83
273
123
412
2
39
56
59
108
83
176
121
261
5
NR
NR
77
102
107
168
151
252
8
NR
NR
90
95
122
161
175
243
10
0
37
87
57
174
82
293
120
444
2
39
61
59
117
82
193
119
287
5
52
56
76
111
105
185
148
277
10
NR
NR
97
100
132
171
188
261
15
0
36
93
56
190
80
325
116
499
2
38
69
57
136
80
225
115
337
5
51
63
75
128
102
216
144
326
10
NR
NR
95
116
128
201
182
308
15
NR
NR
NR
NR
158
186
220
290
20
0
35
96
54
200
78
346
114
537
2
37
74
56
148
78
248
113
375
5
50
68
73
140
100
239
141
363
10
NR
NR
93
129
125
223
177
344
15
NR
NR
NR
NR
155
208
216
325
20
NR
NR
NR
NR
186
192
254
306
30
0
34
99
53
211
76
372
110
584
2
37
80
55
164
76
281
109
429
5
49
74
72
157
98
271
136
417
10
NR
NR
91
144
122
255
171
397
15
NR
NR
115
131
151
239
208
377
20
NR
NR
NR
NR
181
223
246
357
30
NR
NR
NR
NR
NR
NR
NR
NR
NOTE
:
Single appliance venting configurations with zero lateral lengths are assumed to have no elbows in the vent system. For
all other vent configurations, the vent system is assumed to have two 90 ° elbows. For each additional 90° elbow or equivalent (for
example two 45° elbows equal one 90° elbow) beyond two, the maximum capacity listed in the venting table should be reduced by 10
percent (0.90 x maximum listed capacity).