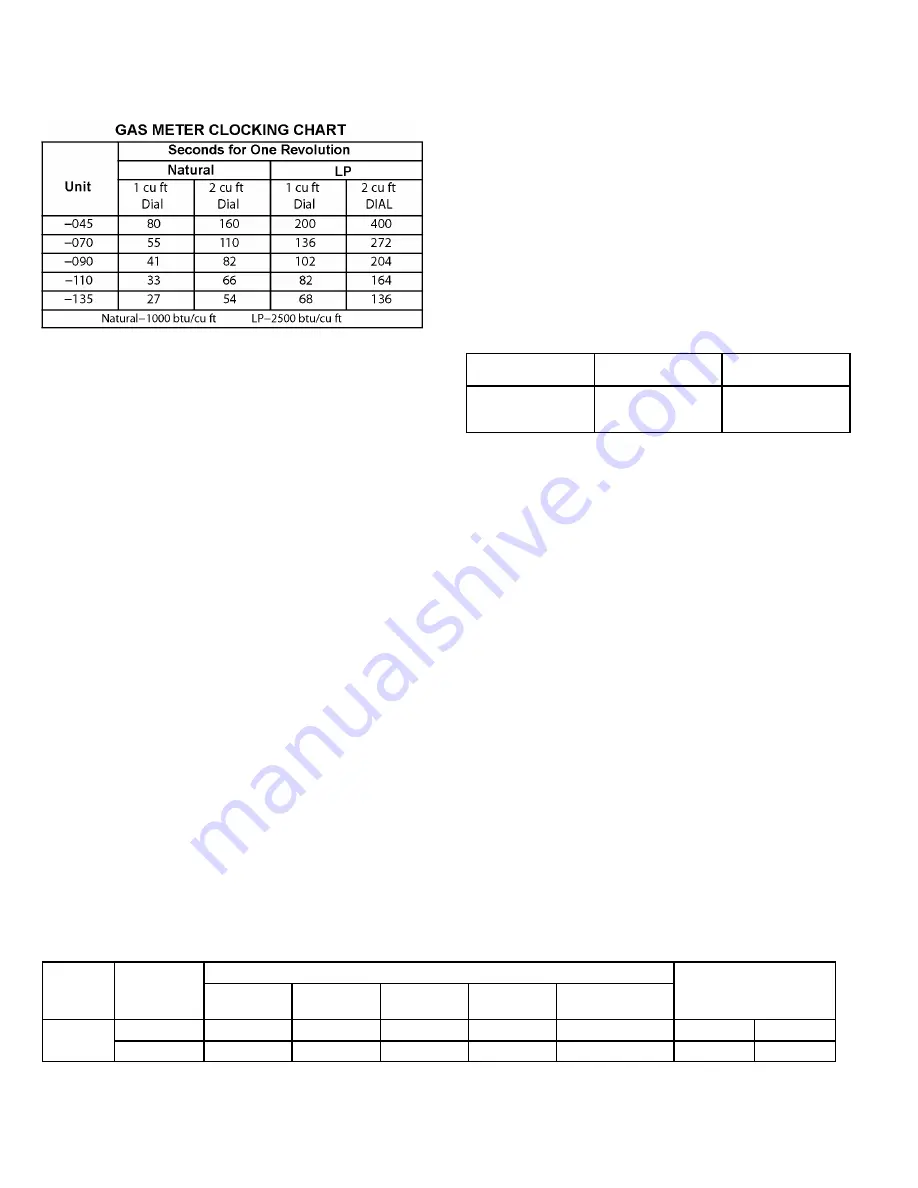
507270-03
Page 46 of 60
Issue 1621
Gas Pressure Adjustment
Gas Flow (Approximate)
Furnace should operate at least 5 minutes before checking
gas flow. Determine time in seconds for
two
revolutions of
gas through the meter. (Two revolutions assures a more
accurate time.)
Divide by two
and compare to time in
Table 11. If manifold pressure matches Table 12 and rate
is incorrect, check gas orifices for proper size and restriction.
Remove temporary gas meter if installed.
NOTE:
To obtain accurate reading, shut off all other gas
appliances connected to meter.
Supply Pressure Measurement
When testing supply gas pressure, use the 1/8” N.P.T.
plugged tap or pressure post located on the gas valve to
facilitate test gauge connection. See Figure 65. Check gas
line pressure with unit firing at maximum rate. Low pressure
may result in erratic operation or underfire. High pressure
can result in permanent damage to gas valve or overfire.
On multiple unit installations, each unit should be checked
separately, with and without other units operating. Supply
pressure must fall within range listed in Table 12.
Manifold Pressure Measurement
1. Remove the threaded plug from the outlet side of the gas
valve and install a field provided barbed fitting. Connect
to a manometer to measure manifold pressure.
2. Start unit and allow 5 minutes for unit to reach steady
state.
High Altitude Information
NOTE:
In Canada, certification for installations at elevations
over 4500 feet (1371 m) is the jurisdiction of local authorities.
Units may be installed at altitudes up to 10,000 ft. above
sea level. See table 13 for de-rate manifold values. Units
installed at altitude of 7501 - 10,000 feet require an orifice
change. Units installed at altitudes of 4,501 - 10,000 feet
(1371 -3048 m) may require a pressure switch change which
can be ordered separately.
Table 14 lists required pressure switch changes and orifice
conversion kits at varying altitudes.
The combustion air pressure switches are factory set and
require no adjustment.
Proper Combustion
Furnace should operate minimum 15 minutes with correct
manifold pressure and gas flow rate before checking
combustion. Take combustion sample beyond the flue outlet
and compare to the tables below.
Page 1
10/13
*2P1013*
507280-01
*P507280-01*
TABLE 1
Manifold and Supply Line Pressure 0-10,000ft.
Unit
Gas
Manifold Pressure in. wg.
Supply Line Pressure
in. w.g.
0 - 10000 ft.
0-4500 ft.
4501-5500 ft.
5501-6500 ft.
6501 - 7500ft.
7501 - 10000ft.
All Sizes
Natural
3.5
3.3
3.2
3.1
3.5
4.5
13.0
LP/propane
10.0
9.4
9.1
8.9
10.0
11.0
13.0
NOTE -
A natural to L.P. propane gas changeover kit is necessary to convert this unit. Refer to the changeover kit installation instruction for the conversion
procedure.
TABLE 2
Manifold and Supply Line Pressure 0-10,000ft.
Unit
Gas
Manifold Pressure in. wg.
Supply Line
Pressure
in. w.g.
0 - 10000 ft.
0-4500 ft.
4501-5500 ft.
5501-6500 ft.
6501 - 7500ft.
7501 - 10000ft.
Low
Fire
High
Fire
Low
Fire
High
Fire
Low
Fire
High
Fire
Low
Fire
High
Fire
Low
Fire
High
Fire
Min
Max
All
Sizes
Natural
1.7
3.5
1.6
3.3
1.5
3.2
1.5
3.1
1.7
3.5
4.5
13.0
LP/propane
4.9
10.0
4.6
9.4
4.4
9.1
4.3
8.9
4.9
10.0
11.0
13.0
NOTE -
A natural to L.P. propane gas changeover kit is necessary to convert this unit. Refer to the changeover kit installation instruction for the conversion
procedure.
Table 12
Table 11
3. While waiting for the unit to stabilize, observe the flame.
Flame should be stable and should not lift from burner.
Natural gas should burn blue.
4. After allowing unit to stabilize for 5 minutes, record
manifold pressure and compare to value given in Table
12.
NOTE:
Shut unit off and remove manometer as soon as an
accurate reading has been obtained. Take care to remove
barbed fitting and replace threaded plug.
Table 13
Unit
CO
2
% for Nat
CO
2
% for L.P.
All
7.2 - 7.9
8.6 - 9.3
The maximum carbon monoxide reading should not exceed 100 ppm.
Summary of Contents for 92G1UH-P
Page 3: ...507270 03 Page 3 of 60 Issue 1621 EXPANDED VIEW Figure 1 ...
Page 22: ...507270 03 Page 22 of 60 Issue 1621 Figure 26 Figure 25 ...
Page 26: ...507270 03 Page 26 of 60 Issue 1621 Figure 31 ...
Page 27: ...507270 03 Page 27 of 60 Issue 1621 Figure 32 ...
Page 29: ...507270 03 Page 29 of 60 Issue 1621 Figure 36 ...
Page 30: ...507270 03 Page 30 of 60 Issue 1621 Figure 37 ...
Page 37: ...507270 03 Page 37 of 60 Issue 1621 Figure 55 Trap Drain Assembly Using 1 2 PVC or 3 4 PVC ...
Page 39: ...507270 03 Page 39 of 60 Issue 1621 Figure 58 Figure 57 ...
Page 40: ...507270 03 Page 40 of 60 Issue 1621 Table 10 ...
Page 43: ...507270 03 Page 43 of 60 Issue 1621 TYPICAL WIRING DIAGRAM Figure 63 ...
Page 50: ...507270 03 Page 50 of 60 Issue 1621 ...
Page 51: ...507270 03 Page 51 of 60 Issue 1621 ...
Page 52: ...507270 03 Page 52 of 60 Issue 1621 BLOWER DATA A95UH1D 95F1UHD ...