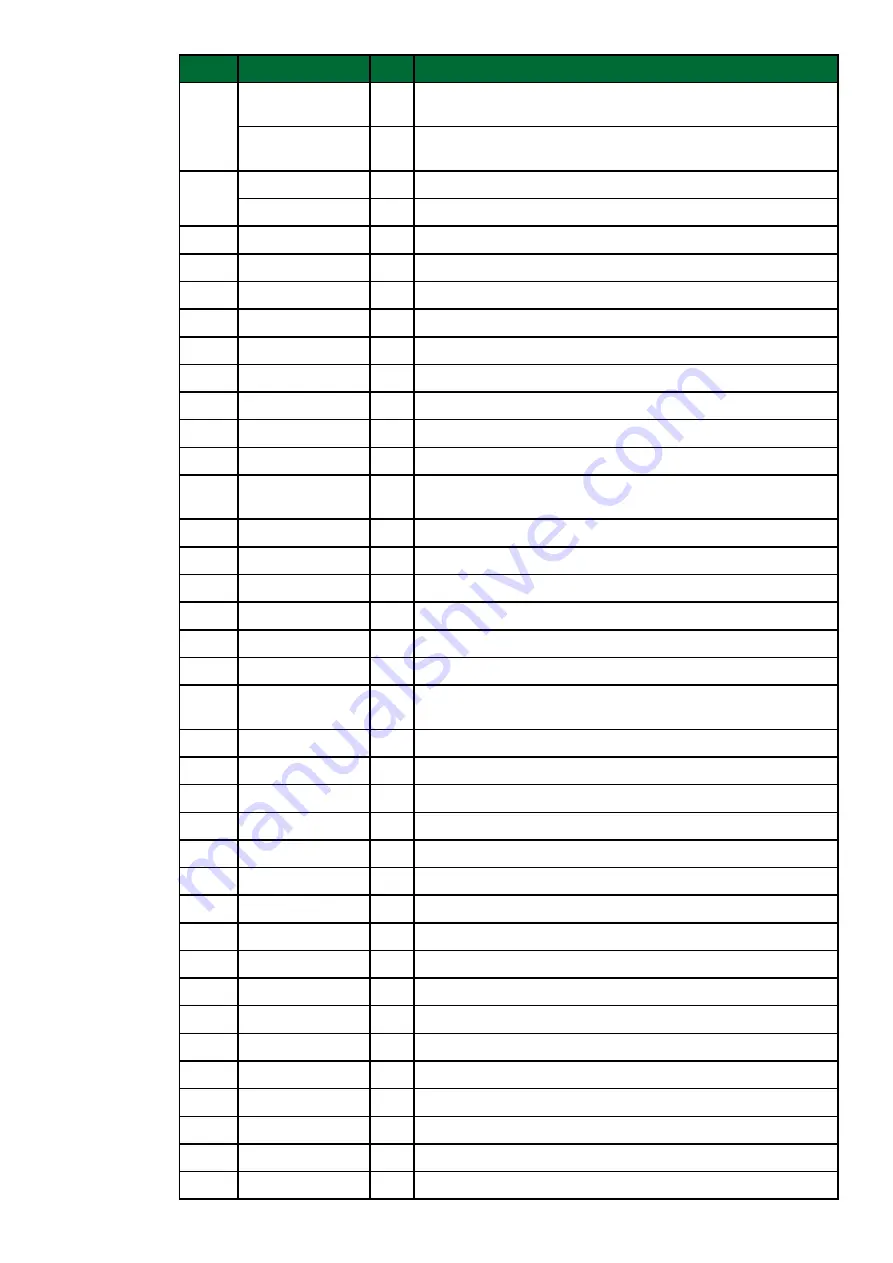
Item:
P/N:
Qty: Description:
19
705019
1
Rotor drive chain - ASA160SH, 119 p joiner link
(Sapphire)
704189
1
Rotor drive chain - ASA160SH, 119 p joiner link
(Diamond)
20
705029
1
Joiner link - ASA160 – 1 pitch - slip fit (Sapphire)
704099
1
Joiner link - ASA160 – 1 pitch - slip fit (Diamond)
21
FP160-007-0013
1
Front rotor spacer
22
EF207-34
1
Rotor Sprocket - 104-tooth ASA160
23
FP160-007-0037 2
Rotor front cover assembly (Auxiliary & square seal)
24
FP280-048-0445
1
Rotor chain tensioner pivot pin assembly
25
FP380-048-0046
1
Rotor chain tensioner arm assembly 2
26
FP200-048-0251
1
Rotor chain tensioner compression spring & seat assembly
27
FP200-009-0025
1
Auger front cover - Lower plate
28
FP200-009-0026
1
Auger front cover - Upper plate
29
703753
1
F516A bearing housing & cover
30
701457
1
H316, 70mm bore adaptor sleeve, ring nut & castellated
washer
31
704122
1
Bearing spacer ring, SR140 x 10
32
700847
1
22216K bearing insert
33
700281
1
M16 x 90mm Bolt
34
FP280-048-0452
1
Rotor drive chain tensioner wear block
35
700283
3
M16 Lock nut
36
FP380-048-0043
1
Rotor chain tensioner arm assembly 1
37
FP200-048-0252
1
Rotor chain tensioner spring seat shaft assembly
(345/365/380)
38
704196
1
Compression spring - 12mm wire, 80mm OD, 280mm long
39
FP160-048-0148
1
Chain tensioner lower spring seat
40
FP160-048-0147
1
Chain tensioner lower spring seat locking nut
41
705862
1
M16 x 175mm bolt
42
FP160-048-0145
1
Chain tensioner lower spring seat adjuster tube assembly
43
700246
2
M12 x 25mm setscrew
44
FP280-048-0395
1
Idler shaft thrust washer
45
FP280-048-0396 6
Idler shaft thrust shim (2mm)
46
FP200-048-0160
1
X18 steel housing bearing with bearing puller shoulder plate
47
FP200-048-0162
1
Idler shaft front bearing mounting plate assembly
48
FP280-048-0386
1
Front idler bearing bolt positioning ring assembly
49
FP200-037-0071
1
PTO guard – MF345/MF365
50
FP160-048-0194 8
Bearing bolt hole reducer & collar (FYH bearing)
51
705145
2
FYH UCF308 40mm bearing with cast 4-bolt flange housing
52
700628
1
Z6 Spline shaft with 8-tooth ASA120 Sprocket
53
FP200-048-0153
1
Idler shaft assembly 2
54
705828
1
Oil Level window
67
Revision A04 July 2018
Summary of Contents for KEENAN MechFiber345
Page 2: ...CONTENTS 2 Revision A04 July 2018 ...
Page 50: ...8 2 Chassis Parts 50 Revision A04 July 2018 ...
Page 52: ...8 3 Front Cover Parts 52 Revision A04 July 2018 ...
Page 54: ...8 4 Standard Feedout Tray Parts 54 Revision A04 July 2018 ...
Page 56: ...8 5 Fold Down Tray Parts Optional Extra Option 56 Revision A04 July 2018 ...
Page 57: ...57 Revision A04 July 2018 ...
Page 64: ...8 10 Driveline Parts 64 Revision A04 July 2018 ...
Page 65: ...65 Revision A04 July 2018 ...
Page 82: ...14423 akgraphics ie keenansystem com KEENAN System KEENANsystem ...