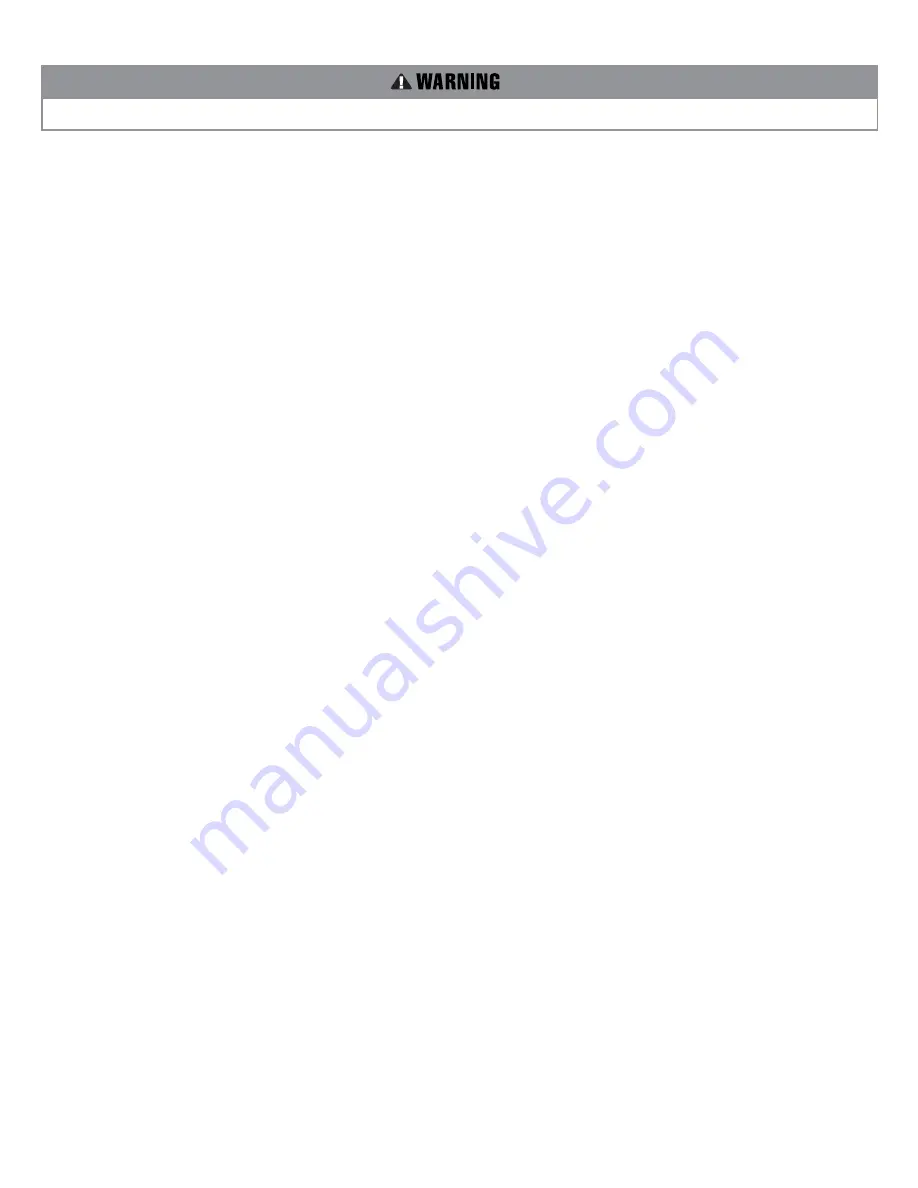
CHECKING SAFETY RELIEF VALVE:
SAFETY RELIEF VALVE MUST BE REPLACED IF IT CANNOT BE ACTUATED OR IT LEAKS AIR AFTER THE RING IS RELEASED.
1. The air compressor must be turned OFF.
2. Disconnect compressor from the power source.
3. Open tank drain to bleed off all air pressure before attempting any maintenance or repair.
4. Allow compressor to fully cool before attempting any maintenance or repair.
5. Grasp the wire ring on the safety relief valve.
6. Pull and release the ring a few times to ensure that the plunger moves in and out. Replace the safety relief valve if plunger does not move or
is difficult to move.
CHECKING AIR FILTER ELEMENT:
1. The air compressor must be turned OFF.
2. Disconnect compressor from the power source.
3. Open tank drain to bleed off all air pressure before attempting any maintenance or repair.
4. Allow compressor to fully cool before attempting any maintenance or repair.
5. Remove the face of the filter body to access the filter element by pushing and rotating the front portion of the filter body in a counter
clockwise direction to release the locking tabs.
6. Use compressed air to blow loose dirt and debris from the paper filter element. Replace filter element if it cannot be cleaned sufficiently.
7. Reinsert filter element into filter body and reinstall filter faceplate.
MOISTURE IN COMPRESSED AIR
Moisture is a normal by-product of compressing air. As the moisture builds during compressor use, it can be carried though the air hose. When
using paint spray gun or sandblasting gun, the use of a special filter to remove moisture from the air line is highly recommended. Moisture in
the compressed air will cause water spots in paint jobs and cause blasting media to clog the sandblasting gun.
12