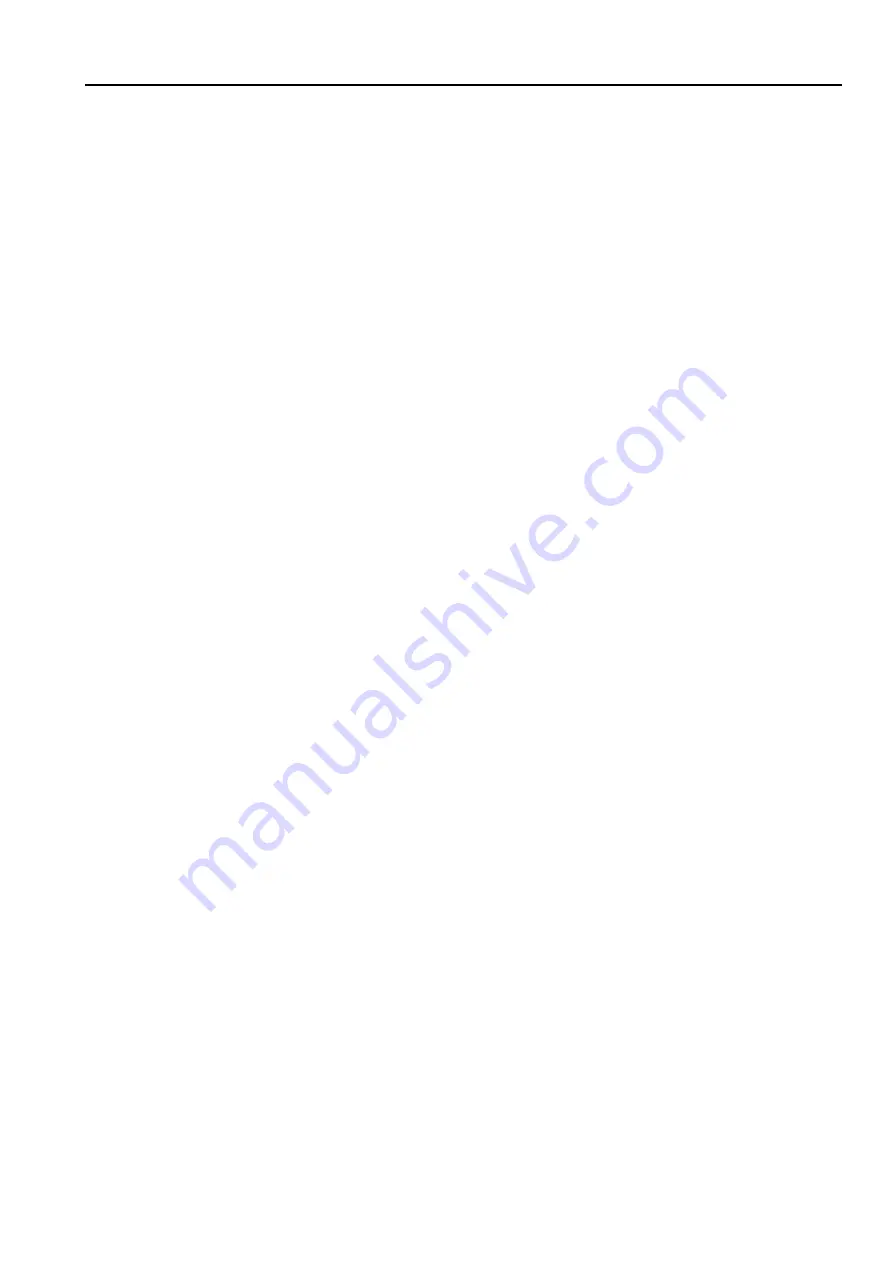
3
4.3.2
Shaft coupling and protection against accidental con-
tact
Shaft coupling according to DIN 740.
A protection against accidental contact
according to
DIN 24 295
is attached as soon as the scope of supply
comprises pump, coupling housing, shaft coupling and
drive.
!
According to the rules for the prevention of accidents,
the pump may be operated only with a protection against
accidental contact according to DIN 24 295.
If a protection against accidental contact is not sup-
plied, it must be installed by the customer.
5.
Installation/mounting
5.1
Installation
The pumps must be installed vertically with drive up-
wards.
Depending upon the immersion depth and pump speed,
it may be necessary to provide a supporting device for
the suction-side operation of the pump.
5.2
Foundation
The foundation design depends on the size of the pump
and/or the pump aggregate and the local installation
conditions. For exact data on the pump and aggregate
dimensions, please refer to our tables of dimensions.
The foundation may be designed as concrete founda-
tion or load-carrying foundation frame, for example of
the steel type.
All foundation designs are subject to the following: The
foundation must be designed so that it can take the
weight of the pump aggregate on the entire surface.
5.3
Assembly of pump and drive
The aggregate being completed at the place of service
only, the coupling must be assembled as follows:
1. Cover pump and drive shaft end with a filmy coat of
molybdenum disulfite (e.g. Molykote), and insert keys.
2. By means of a mounting device, push pump and
motor-side coupling halves on until the shaft end is
flush with the coupling hub.
If no mounting device is available, heating of the cou-
pling halves to approx. 100
h
C (without rubber buf-
fers) facilitates mounting.
3. By means of a grub screw according to DIN 916, fix
coupling halves axially.
4. When assembling pump and motor, geared motor
and/or variable-speed gear it must be ensured that
the coupling halves are accurately aligned. Depend-
ing upon the size of coupling, the distance between
the coupling halves must be 2–8 mm.
!
5.
Mount protection against accidental contact accor-
ding to DIN 24 295.
5.4
Drive by V-belt drive
In case of a V-belt reduction from the drive to the pump,
make sure that the two V-belt pulleys are aligned in
parallel.
The V-belt pulleys must be pushed onto the shaft ends
as far as possible. It must be possible to regulate the
tension of the V-belts sufficiently by means of a motor
rocker or by means of tensioning rails. They must be
slightly retightened after a short running-in period.
B
Excessive tensioning will destroy the
anti-friction bearings of the pump.
Our
separate instructions – V-belt drive – VM 706.0001 GB/
Ident No. 133 586 must be complied with.
5.5
Laying of pipelines
5.5.1
Nominal diameters
The nominal diameter of the suction line should be
designed according to the nominal pump branch dia-
meter. In case of considerable deviations please contact
the factory.
5.5.2
Supports and flange connections
By way of the flange connections, the pipelines must be
connected to the pump, stress-free. They must be sup-
ported close to the pump and should allow of easy scr-
ewing to avoid deformations. After the screws have
been slackened, the flanges must neither be inclined
nor springy nor rest on top of one another under pres-
sure. Any thermal stresses that may occur at the pipe-
lines must be kept away from the pump by taking appro-
priate measures, e.g. by the installation of compen-
sators.
5.5.3
Cleaning of tanks prior to attachment
Prior to mounting the pump, the suction-side tanks must
by all means be flushed and/or cleaned.
Items left over from assembly operations, e.g. screws,
nuts, welding beads, pieces of steel etc. will destroy the
pump internals. Any guarantee claims will expire if and
when damages are caused by such items.
5.6
Laying of auxiliary pipelines for additional facilities
All auxiliary pipelines for the supply of the shaft seal and
the double shell casing, if any, for heating and cooling of
the shaft sealing housing are to be connected, stress-
free and sealing.
In case of double-acting mechanical seal (design: G08,
G09), the lines for the sealing liquid are to be laid with
the largest possible flow cross section. The sealing
liquid outlet is at the highest connection of the mecha-
nical seal housing.
The flow direction of the flushing and sealing liquid is
shown by means of arrows in the sectional drawings.
In order to ensure automatic ventilation, the lines must
be laid continuously ascending, short and promoting
easy flow.
Air bag formation and gas bubble formation are to be
avoided, if required, ventilation connections must be
provided. The heating/cooling liquid outlet must be con-
nected at the highest connection of the double shell
casing, if any.
5.7
Safety and control devices
5.7.1
Pressure gauge
A pressure gauge must be connected to the discharge
line.
5.7.2
Safety element in the discharge line
If a shut-off element is fitted in the discharge line or if
there is a possibility of the discharge line becoming
blocked, a safety element must be provided. For exam-
ple: by-pass with built-in relief valve, bursting disk,
motor protection switch, etc.
!
Eccentric screw pumps are positive-displacement
pumps and can theoretically generate an infinitely high
pressure.
With the discharge line closed, e.g. by clogging or by
incidental closing of a valve, the pressure generated by
the pump may reach a multiple of the admissible pres-
sure of the plant. This may, for example, lead to the
bursting of lines which must be absolutely avoided
especially when handling dangerous products. Thus,
appropriate safety devices must also be installed in
the plant (e.g. pressure switches).
Series SLTP, SETP, SNTP, SLTBP, SETBP, SNTBP
ALLWEILER
a