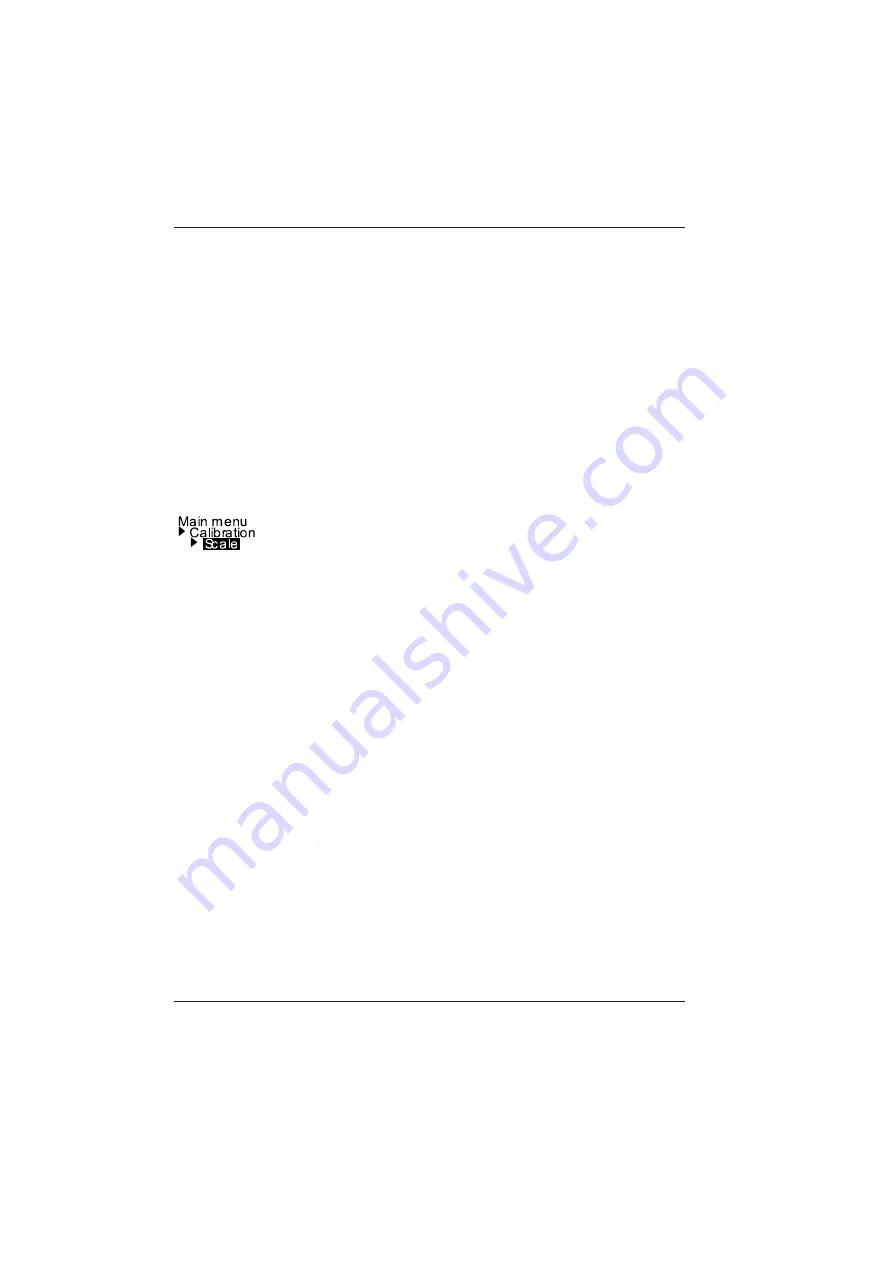
30
Measurement techniques
7.2 Anodized aluminum and other metal surfaces
The measuring unit is equipped with an extended
measuring range for measuring samples with a very
high reflectance.
The reflectance of non-metallic surfaces increases
with the angle of incidence. The reflective properties of
metals do not always behave in this manner. Because
of double reflection, the light is partially reflected on
the coating and partially on the metal underneath. For
a complete understanding of the reflective properties
of such surfaces, it is recommended to measure them
at all geometries.
In addition to the reference to a black glass standard
(gloss units), it is also common in the area of metals
to relate the reflectometer value to the amount of
irradiated light and to express it as a % (reflectance).
You can select this in the Scale menu.
Notes
Proper measurements are only possible on level
surfaces.
Measurements on dirty, scratched or otherwise
distorted areas of the test specimen are not meaning-
ful except as a way of determining the degree of such
imperfections by means of a gloss measurement.
Since it cannot be assumed that the gloss capacity is
not constant over the entire surface of the test
specimen, the reflectometer value can be measured
at several different places and the standard deviation
can be determined.
If the sample exhibits structures or directionally
dependent gloss properties, the structural features
and the direction of the incident light should be
specified for the measurement in the test report.
Samples that must be measured several times over
the course of an examination (for example weathering
samples) should be marked accordingly to ensure
that the measurement is made at the same point
during repeated tests.