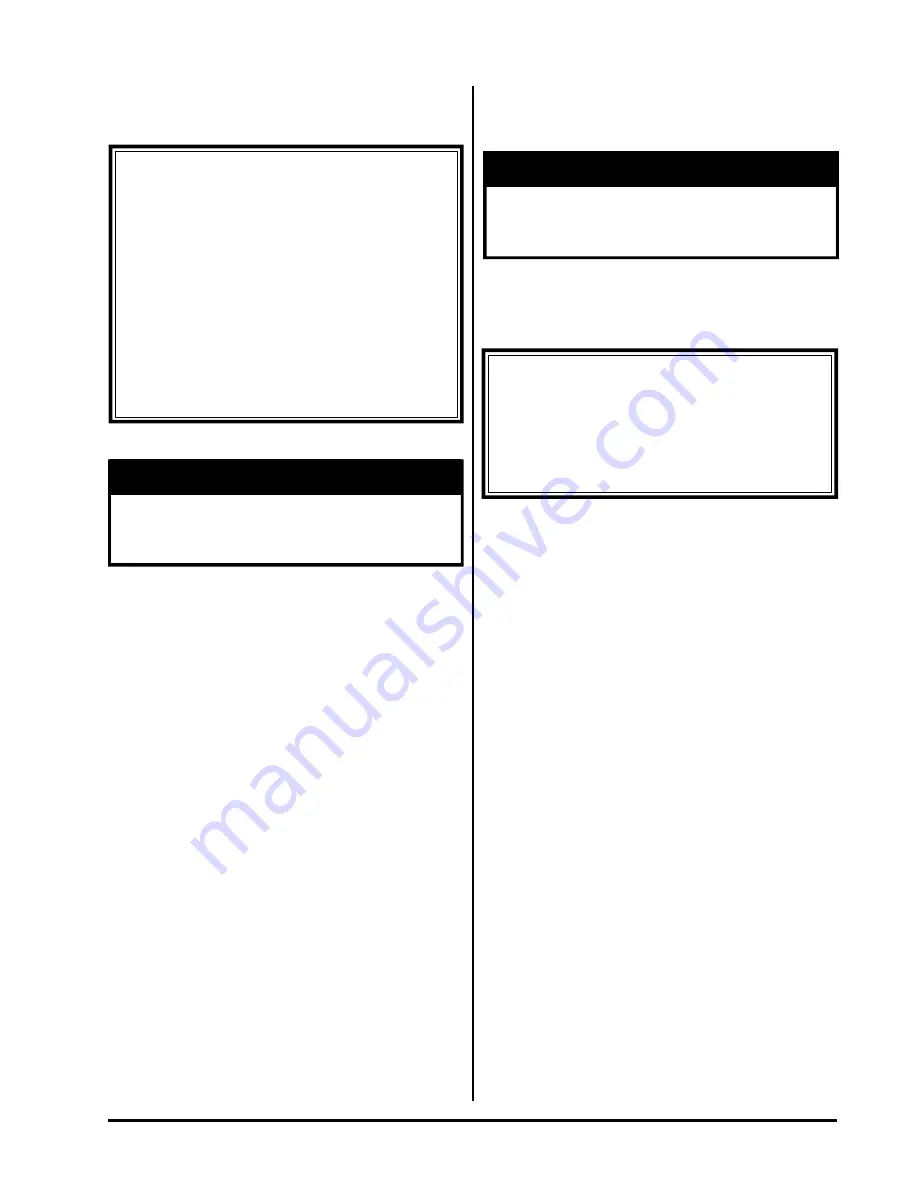
© 1999 Amada
11
4.0
Prestart-Up Check
(See Figure 1)
On hoppers with drum arrangements, make sure
that all the connections are airtight.
3.6
Compressed Air Supply Installation
(See Figure 1)
1. Remove the plastic pipe plug from the end of
the unit's compressed-air manifold and
connect the compressed-air supply line.
2. The compressed-air supply line should be
installed with a safety exhaust shutoff valve,
a bleed-type regulator with a gauge adjusted
to 90-psi, and a coalescing filter with an
automatic drain, all supplied by others. Use
pipe sealant on all compressed-air
connections and locate components for
convenient service.
3. Be sure that all compressed-air components
are adequately sized to meet the maximum
system requirements of 1.1 scfm per pulse at
90- psi supply pressure.
Check that the blower-fan exhaust is free
of debris before starting.
CAUTION
NOTE
Check that the hopper discharge is sealed
and not open to the atmosphere. Too
much airflow to the blower fan will cause
electrical failure.
Turn compressed-air supply OFF and bleed
supply lines before performing service work.
NOTE
• The compressed-air supply must be
both oil and moisture free.
Contamination in the compressed-air
used to clean filter cartridges will result
in poor cleaning or cleaning valve
failure and poor collector performance.
• Purge compressed-air lines to remove
debris before connecting to the
compressed-air manifold on the unit.
CAUTION
Summary of Contents for ADF4
Page 22: ...Replacement Parts List...
Page 32: ...1999 Amada 33 Notes...
Page 33: ...1999 Amada 34 Notes...