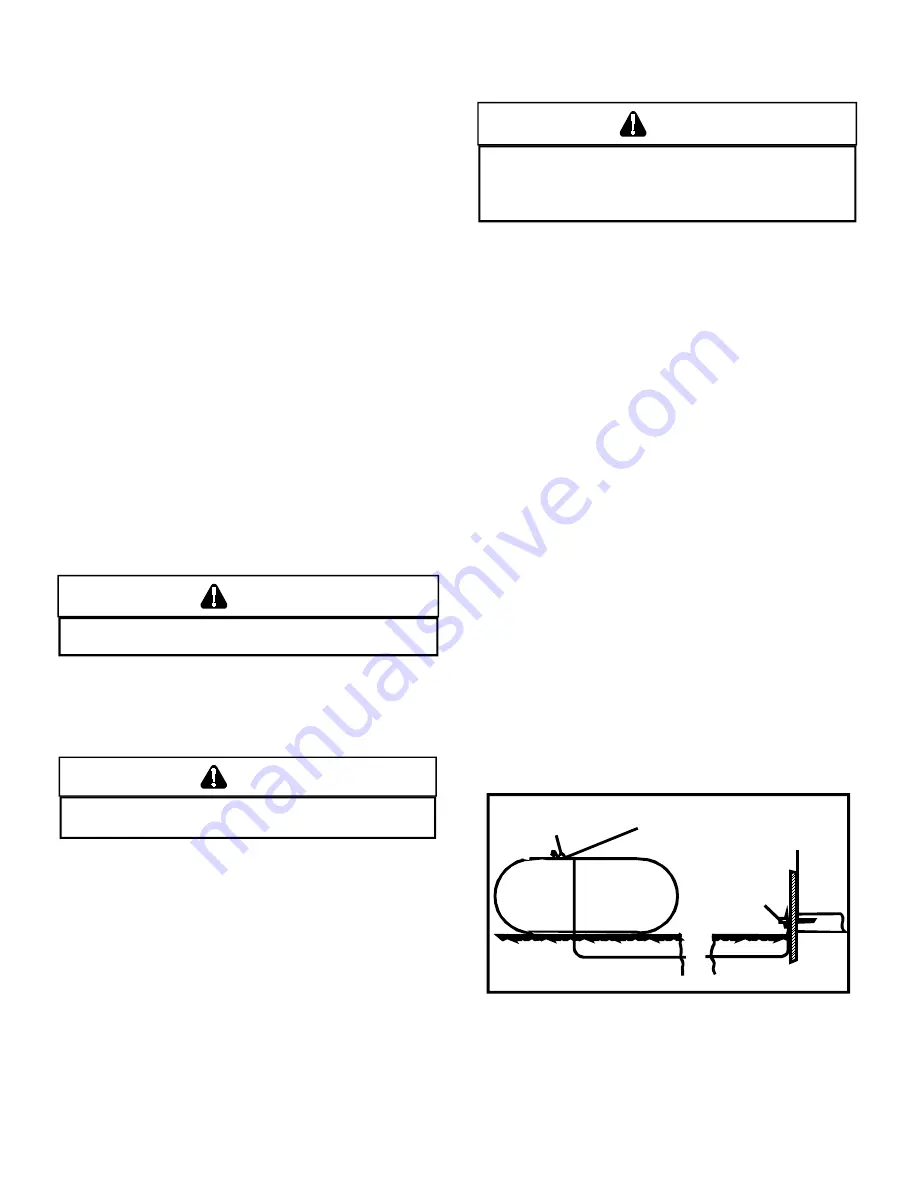
PRODUCT DESIGN
29
7. Install a manual shutoff valve between the gas meter
and unit within six feet of the unit. If a union is in-
stalled, the union must be downstream of the manual
shutoff valve, between the shutoff valve and the fur-
nace.
8. Tighten all joints securely.
9. Connect the furnace to the building piping by one of
the following methods:
– Rigid metallic pipe and fittings.
– Semi-rigid metallic tubing and metallic fittings. Alumi
-
num alloy tubing must not be used in exterior locations.
In order to seal the grommet cabinet penetration, rigid
pipe must be used to reach the outside of the cabinet.
A semi-rigid connector to the gas piping may be used
from there.
10. Use listed gas appliance connectors in accordance with
their instructions. Connectors must be fully in the same
room as the furnace.
11. Protect connectors and semi-rigid tubing against phys-
ical and thermal damage when installed. Ensure alumi-
num-alloy tubing and connectors are coated to protect
against external corrosion when in contact with masonry,
plaster, or insulation, or subjected to repeated wetting by
liquids such as water (except rain water), detergents, or
sewage.
CAUTION
E
DGES OF SHEET METAL HOLES MAY BE SHARP.
U
SE GLOVES A PRECAUTION
WHEN REMOVING HOLE PLUGS.
GAS PIPING CHECKS
Before placing unit in operation, leak test the unit and gas
connections.
WARNING
T
O AVOID THE POSSIBLITY OF EXPLOSION OR FIRE, NEVER USE A MATCH
OR OPEN FLAME TO TEST FOR LEAKS.
Check for leaks using an approved chloride-free soap and
water solution, an electronic combustible gas detector, or
other approved testing methods.
NOTE:
Never exceed specified pressures for testing. Higher
pressure may damage the gas valve and cause subsequent
overfiring, resulting in heat exchanger failure. Disconnect this
unit and shutoff valve from the gas supply piping system be-
fore pressure testing the supply piping system with pressures
in excess of 1/2 psig (3.48 kPa). Isolate this unit from the
gas supply piping system by closing its external manual gas
shutoff valve before pressure testing supply piping system
with test pressures equal to or less than 1/2 psig (3.48 kPa).
PROPANE GAS TANKS AND PIPING
WARNING
P
ROPANE GAS IS HEAVIER THAN AIR AND ANY LEAKING GAS CAN SETTLE IN
ANY LOW AREAS OR CONFINED SPACES.
T
O PREVENT PROPERTY DAMAGE,
PERSONAL INJURY, OR DEATH DUE TO FIRE OR EXPLOSION CAUSED BY A
PROPANE GAS LEAK, INSTALL A GAS DETECTION WARNING DEVICE.
A gas detecting warning system is the only reliable way to
detect a propane gas leak. Iron oxide (rust) can reduce the
level of odorant in propane gas. Do not rely on your sense of
smell. Contact a local propane gas supplier about installing
a gas detecting warning system. If the presence of gas is
suspected, follow the instructions on this page.
All propane gas equipment must conform to the safety
standards of the National Board of Fire Underwriters, NBFU
Manual 58.
For satisfactory operation, propane gas pressure must be
11 inch WC at the furnace manifold with all gas appli ances
in operation. Maintaining proper gas pressure depends on
three main factors:
1. Vaporization rate, depending on temperature of the liquid,
and “wetted surface” area of the con tainer or containers.
2. Proper pressure regulation. (Two-stage regulation is
recommended for both cost and efficiency).
3. Pressure drop in lines between regulators, and between
second stage regulator and the appliance. Pipe size will
depend on length of pipe run and total load of all appli-
ances.
Complete information regarding tank sizing for vaporiza-
tion, recommended regulator settings, and pipe sizing is
available from most regulator manufacturers and propane
gas suppliers.
Always use a pipe sealant approved for natural gas and LP
gas.
Refer to the following illustration for typical propane gas
installations and piping.
200 PSIG
Maximum
5 to 15 PSIG
(20 PSIG Max.)
Continuous
11" W.C.
Second Stage
Regulator
First Stage
Regulator
Typical Propane Gas Installation