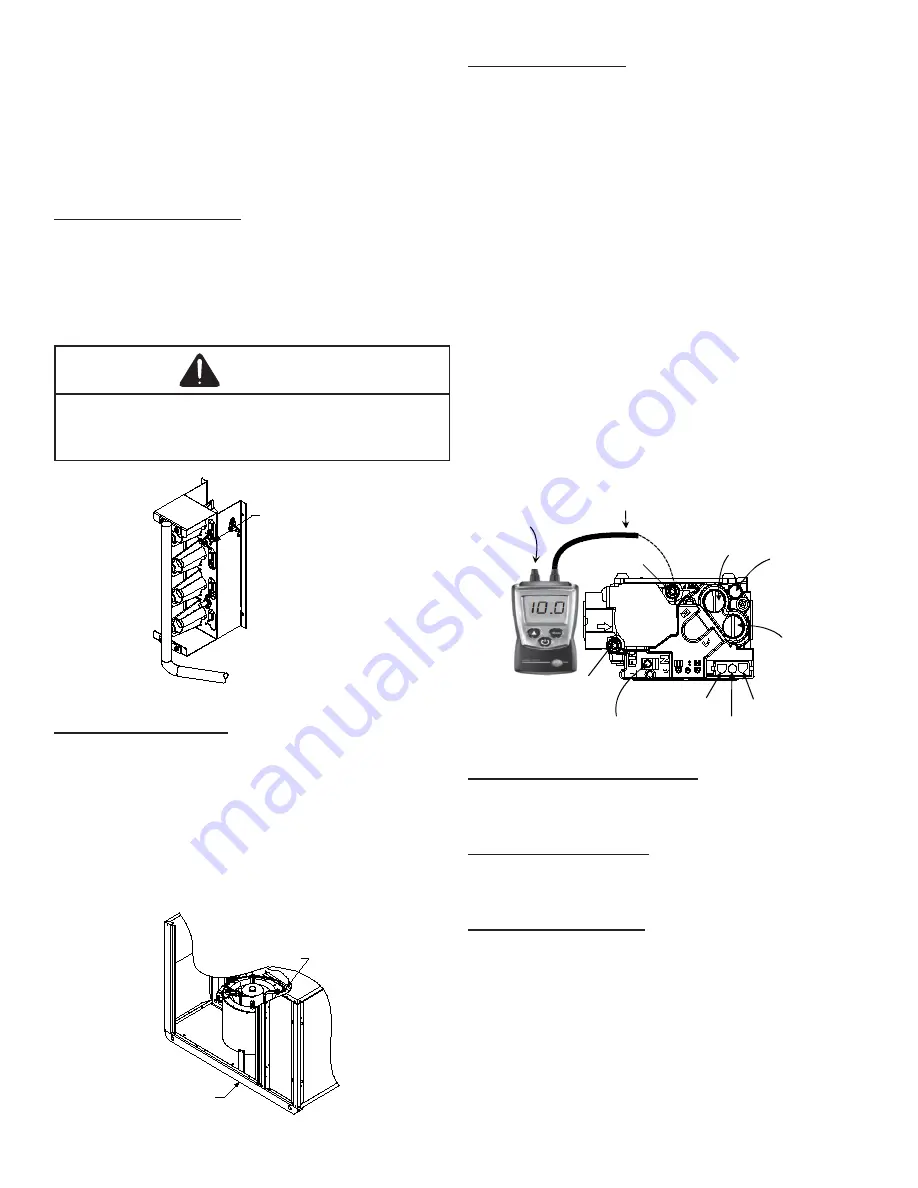
14
On new installations, or if a major component has been re-
placed, the operation of the unit must be checked.
Check unit operation as outlined in the following instructions.
If any sparking, odors, or unusual sounds are encountered,
shut off electrical power and check for wiring errors, or ob
-
structions in or near the blower motors.
Duct covers must
be removed before operating unit.
Rollout Protection Control
The rollout protection device opens, cutting power to the gas
valve, if the flames from the burners are not properly drawn
into the heat exchanger. The rollout protection device is lo-
cated on the burner bracket. The reason for elevated tem-
peratures at the control must be determined and repaired
prior to resetting this manual reset control.
WARNING
To avoid property damage, personal injury or death due to
fire or explosion, a qualified servicer must investigate the
reason for the rollout protection device to open BEFORE
manually resetting the rollout protection device.
Rollout Protection
Rollout Protection on Burner Bracket
Secondary Limit Control
The secondary limit control is located on the top of the blower
scroll assembly. This control opens when elevated tempera-
tures are sensed. Elevated temperatures at the control are
normally caused by blower failure. The reason for the opening
should be determined and repaired prior to resetting.
If the power to the unit is interrupted during the heating cy-
cle, it may cause the secondary limit to trip. Once the blower
compartment temperature drops below the limit reset tem-
perature, the limit will automatically reset.
Secondary
Control Limit
Back of Unit
Secondary Control Limit
Pre-Operation Checks
1. Close the manual gas valve external to the unit.
2. Turn off the electrical power supply to the unit.
3. Set the room thermostat to its lowest possible setting.
4. Remove the heat exchanger door on the side of the
unit by removing screws.
5. This unit is equipped with an ignition device which
automatically lights the main burner. DO NOT try to
light burner by any other method.
6. Move the gas control valve switch to the OFF position.
Do not force.
7. Wait five minutes to clear out any gas.
8. Smell for gas, including near the ground. This is
important because some types of gas are heavier than
air. If you have waited five minutes and you do smell
gas, immediately follow the warnings on page 3 of this
manual. If having waited for five minutes and no gas
smell is noted, move the gas control valve switch to
the ON position.
9. Replace the heat exchanger door on the side of the
unit.
10. Open the manual gas valve external to the unit.
11. Turn on the electrical power supply to the unit.
12. Set the thermostat to desired setting.
On/Off Switch
Inlet
Pressure Boss
High Fire
Coil Terminal (HI)
Low Fire
Regulator Adjust
Manometer
Manometer
Hose
A
High Fire Regulator
Adjust
Regulator
Vent
Common
Terminal (C)
Coaxial Coil
Terminal (M)
Outlet
Pressure Boss
Open to
Atmosphere
White-Rodgers Model 36G54 connected to Manometer
Gas Supply And Manifold Check
Gas supply pressure and manifold pressure with the burners
operating must be as specified on the rating plate.
Gas Inlet Pressure Check
Gas inlet pressure must be checked and adjusted in accor-
dance to the type of fuel being consumed.
With Power And Gas Off:
NOTE:
Use adapter kit #0151K00000S to measure gas
pressure on White-Rodgers 36G54 gas valves.
1. Back inlet pressure test screw (inlet pressure boss)
out one turn (counterclockwise, not more than one
turn).
Alternately, inlet gas pressure may be measured by
removing the cap from the dripleg and installing a
predrilled cap with a hose barb fitting.
2. Connect a water manometer or adequate gauge to
the inlet pressure tap of the gas valve (or hose barb
fitting on predrilled cap).